UV Flatbed Printer: Technical Aspects of Double-Sided Printing
In the realm of digital printing technology, UV flatbed printers have emerged as a versatile and efficient solution for a wide array of printing needs. Among the myriad capabilities these printers possess, double-sided printing stands out as a particularly intriguing and useful feature. This technical capability not only enhances the aesthetic appeal and functionality of printed materials but also opens up new avenues for creativity and application. In this article, we delve into the technical aspects of double-sided printing with UV flatbed printers, exploring its mechanisms, benefits, challenges, and the future prospects of this innovative technology.
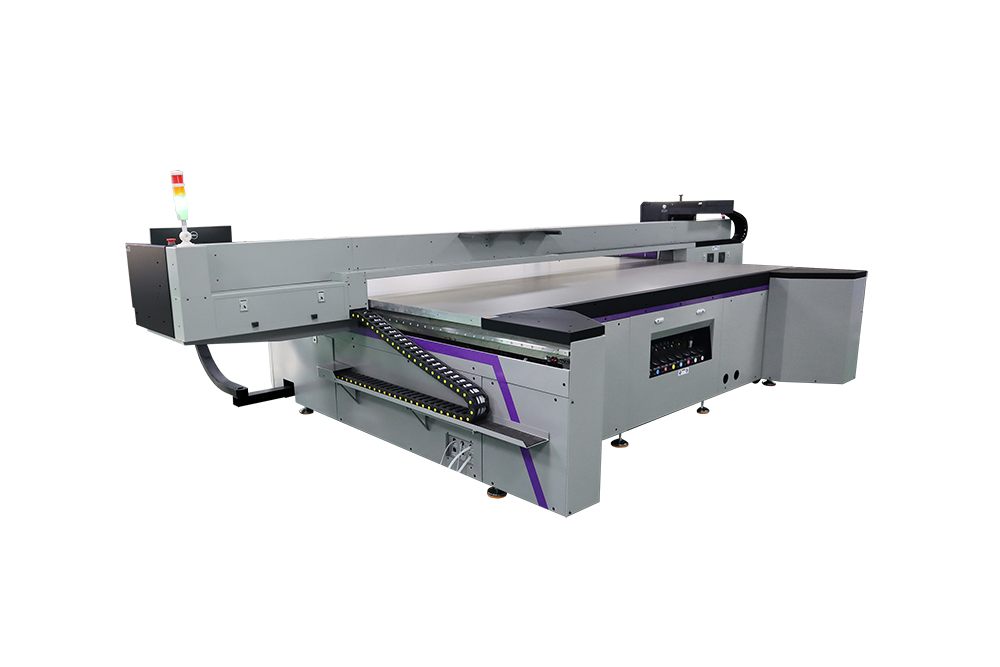
Introduction to UV Flatbed Printers
UV flatbed printers are a type of digital printing equipment that utilize ultraviolet (UV) light to cure or dry the ink immediately after it is applied to the substrate. This process allows for high-quality, durable prints on a variety of materials, including rigid substrates like wood, glass, metal, and plastics, as well as flexible materials like fabrics and vinyl. The flatbed design enables the printer to handle substrates of varying thicknesses and sizes, making it ideal for a range of applications from signage and packaging to artistic reproductions and personalized products.
The Mechanics of Double-Sided Printing
Double-sided printing, also known as duplex printing, involves printing on both sides of a substrate simultaneously or in a sequential manner. In the context of UV flatbed printers, achieving this requires a combination of precise mechanical engineering, advanced software control, and specialized ink delivery systems.
Printer Design and Configuration
Dual Print Heads: Some UV flatbed printers are equipped with dual print heads, one for each side of the substrate. These heads are strategically positioned to ensure accurate alignment and consistent ink application.
Flipper Mechanisms: In printers designed for sequential double-sided printing, a flipper mechanism is used to turn the substrate over after the first side has been printed. This mechanism must be highly precise to maintain the correct orientation and positioning of the substrate for the second print pass.
Ink Curing Systems: UV lamps or LEDs are positioned to cure the ink instantly after it is applied. For double-sided printing, the curing system must be configured to accommodate both sides of the substrate without causing ink smearing or damaging the freshly printed surface.
Software and Control
Print Job Management: Sophisticated software algorithms are used to manage the print job, ensuring that the correct image is printed on each side of the substrate. This includes handling file preparation, color management, and print queue optimization.
Alignment and Registration: Achieving perfect alignment between the front and back prints is critical. The printer’s software uses registration marks or sensors to ensure that the second side is printed in exact alignment with the first.
User Interface: The printer’s control panel or software interface should provide intuitive options for selecting double-sided printing modes, adjusting print settings, and monitoring the print process.
Benefits of Double-Sided Printing
The adoption of double-sided printing in UV flatbed printers offers several advantages:
Enhanced Aesthetic Appeal: Double-sided prints provide a more professional and finished look, particularly for applications like book covers, packaging, and display materials.
Increased Functionality: In the case of packaging or signage, double-sided printing can convey more information or create a more engaging visual experience for the viewer.
Cost Efficiency: By printing both sides of a substrate in one pass or with minimal handling, double-sided printing can reduce material waste, labor costs, and production time.
Versatility: The ability to print on both sides of a variety of materials expands the range of potential applications, from marketing materials to functional products like coasters, menu boards, and more.
Challenges and Considerations
While double-sided printing offers numerous benefits, it also presents some technical and operational challenges:
Ink Adhesion and Curing: Ensuring that the ink adheres properly to both sides of the substrate and cures without issue can be complex. Different substrates may require specific ink formulations and curing parameters.
Print Alignment: Achieving precise alignment between the front and back prints is crucial but can be challenging, particularly for substrates that are prone to shrinkage or expansion during the printing process.
Substrate Handling: Managing the physical handling of the substrate, especially for larger or thicker materials, can be complex. Flipper mechanisms must be robust and precise to avoid damaging the substrate or the printed image.
Software Complexity: The software controlling the printer must be capable of managing the additional complexity of double-sided printing, including file handling, color management, and print job scheduling.
Overcoming Challenges
To address these challenges, manufacturers of UV flatbed printers are continuously innovating, developing new technologies and methodologies to improve double-sided printing capabilities:
Advanced Ink Systems: Specialized inks and curing technologies are being developed to improve adhesion and cure performance across a wider range of substrates.
Enhanced Registration Techniques: Improved registration systems, using cameras or other sensors, ensure more accurate alignment between front and back prints.
Automated Handling Systems: Advanced substrate handling systems, including robotic arms and conveyors, minimize manual intervention and improve the precision of substrate flipping and positioning.
Software Optimizations: Print management software is being refined to better handle the complexities of double-sided printing, offering more intuitive interfaces and robust job management tools.
Future Prospects
The future of double-sided printing in UV flatbed printers is promising. As technology continues to advance, we can expect to see:
Increased Adoption: As the benefits of double-sided printing become more widely recognized, and the technology becomes more accessible, its adoption will likely increase across various industries.
Technological Innovations: Continued innovation in ink formulations, curing technologies, and substrate handling systems will further enhance the capabilities and reliability of double-sided printing.
Expanded Applications: The versatility of double-sided printing will drive the development of new and innovative applications, particularly in areas like packaging, personalized products, and artistic reproductions.
Integration with Other Technologies: Double-sided printing will increasingly be integrated with other advanced manufacturing technologies, such as 3D printing and automation, to create more complex and multifunctional products.
Double-sided printing in UV flatbed printers represents a significant advancement in digital printing technology, offering enhanced aesthetic appeal, increased functionality, and cost efficiency. While it presents certain technical and operational challenges, ongoing innovation and technological developments are continuously improving the capabilities and reliability of this process. As the technology matures, we can expect to see double-sided printing become a more integral part of the digital printing landscape, enabling new applications and driving creativity and innovation across various industries.