UV Flatbed Printer: The Advantages of Printing with Primer
UV Flatbed Printer: The Advantages of Printing with Primer
In the realm of digital printing, UV flatbed printers have emerged as a versatile and efficient solution for a wide array of applications. These printers utilize ultraviolet (UV) light to instantly dry and cure inks onto various substrates, offering unparalleled speed, precision, and versatility. Among the many techniques and enhancements that can further elevate the performance of UV flatbed printers, the use of primer stands out as a critical yet often underappreciated aspect. This article delves into the advantages of printing with primer on a UV flatbed printer, highlighting how it can transform the quality, durability, and adaptability of printed materials.
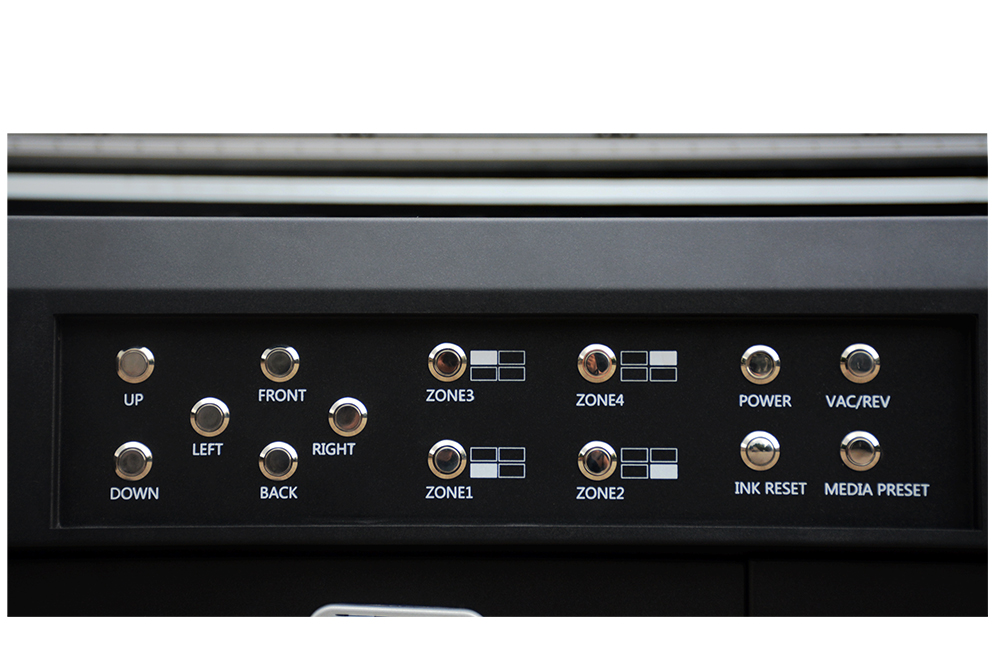
Understanding Primers: The Foundation for Superior Prints
A primer is a preparatory coating applied to a substrate before the main ink or paint layer is added. Its primary function is to create an optimal surface for adhesion, ensuring that the subsequent ink layers bond securely and evenly. In the context of UV flatbed printing, primers serve a dual purpose: they enhance the substrate’s compatibility with UV inks and improve the overall print quality.
Primers can be formulated for specific substrates, such as metals, plastics, woods, glass, and ceramics, addressing the unique surface properties of each material. By modifying the substrate’s surface energy, primers facilitate better wettability and penetration of UV inks, leading to more uniform and durable prints.
Advantages of Using Primer in UV Flatbed Printing
1. Improved Adhesion
One of the most significant advantages of using primer in UV flatbed printing is the improvement in ink adhesion. Many substrates, especially non-porous ones like metals and plastics, can be challenging for UV inks to bond with directly. Primers act as a bridge, providing a layer with a high affinity for both the substrate and the ink. This ensures that the printed image remains securely attached, minimizing the risk of cracking, peeling, or fading over time.
Moreover, primers can help to fill in small imperfections or pores on the substrate surface, creating a smoother and more uniform base for the ink to adhere to. This contributes to a more consistent print quality, with fewer defects and a higher overall appearance.
2. Enhanced Durability
Durability is a crucial factor in many printing applications, especially those that involve exposure to environmental elements or physical wear and tear. Primers can significantly enhance the durability of UV flatbed prints by creating a protective barrier between the substrate and the ink.
This barrier can provide additional resistance to scratching, chemicals, UV light, and moisture. In outdoor applications, where prints are exposed to direct sunlight and weather conditions, primer-treated prints are likely to retain their color vibrancy and structural integrity longer than those without primer.
3. Increased Color Vibrancy and Opacity
UV inks are known for their vibrant and saturated colors, but the quality of these colors can vary depending on the substrate. Primers can help to amplify color vibrancy by creating a more receptive surface for the inks. They can also improve opacity, ensuring that even light-colored or transparent inks appear rich and solid on darker substrates.
By optimizing the substrate’s surface for ink absorption, primers enable more consistent and even ink distribution. This results in prints with more uniform color density and fewer visible ink dots or banding, enhancing the overall visual appeal.
4. Widened Substrate Compatibility
UV flatbed printers are known for their versatility in handling a wide range of substrates. However, not all substrates are inherently compatible with UV inks. Primers can expand the range of printable materials by preparing surfaces that would otherwise be incompatible.
For example, certain plastics or woods may have surfaces that are too smooth or too reactive with UV inks to produce high-quality prints without primer. By applying a suitable primer, these materials can be transformed into suitable substrates for UV flatbed printing, unlocking new creative possibilities and applications.
5. Cost-Effective Printing
While the use of primer adds an additional step to the printing process, it can often lead to cost savings in the long run. By improving ink adhesion and durability, primers reduce the need for costly reprints or replacements due to failed prints. They also enable the use of less expensive substrates that may require primer treatment to achieve high-quality prints.
Furthermore, primers can optimize ink consumption, ensuring that less ink is wasted on poor adhesion or uneven distribution. This leads to more efficient ink usage and lower operational costs per print.
6. Facilitated Problem-Solving
Printing challenges, such as ink bleeding, beading, or poor coverage, can be difficult to address without the right tools. Primers offer a practical solution to these problems by modifying the substrate’s surface properties to be more conducive to UV printing.
For instance, primers can help to reduce ink bleeding by creating a more absorbent surface that quickly draws the ink into the primer layer. They can also prevent beading by ensuring that the ink spreads evenly across the surface, avoiding the formation of small ink droplets.
By addressing these common printing issues, primers can streamline the printing process, reducing downtime and enhancing productivity.
Considerations for Choosing and Applying Primer
While the advantages of using primer in UV flatbed printing are numerous, selecting and applying the right primer requires careful consideration. Here are some key factors to keep in mind:
Compatibility with Substrate and Ink: Ensure that the primer is formulated for the specific substrate you are working with and is compatible with the UV inks you intend to use.
Application Technique: The method of primer application (e.g., spray, brush, roll) can affect its effectiveness. Follow the manufacturer’s instructions for the best results.
Drying and Curing: Primers need to be fully dried and cured before applying UV inks. Ensure that you have adequate time and equipment for this process.
Coating Thickness: The thickness of the primer layer can impact the final print quality. Apply an even and consistent coat, avoiding excess or insufficient primer.
Environmental Conditions: Humidity, temperature, and air circulation can affect primer performance. Monitor and control these conditions to maintain optimal primer effectiveness.
Conclusion
UV flatbed printers have revolutionized the digital printing industry with their speed, precision, and versatility. However, to fully harness their potential, it is essential to consider the role of primer in the printing process. By improving adhesion, durability, color vibrancy, substrate compatibility, and cost-effectiveness, primers offer a critical enhancement to UV flatbed printing.
As the printing industry continues to evolve, the strategic use of primers will remain a cornerstone of achieving high-quality, durable, and versatile prints. By understanding the benefits and considerations of primer application, printers can unlock new creative possibilities and optimize their UV flatbed printing processes for maximum efficiency and impact.