UV Flatbed Printer: The Basics of Media Pre-Treatment and Coating
In the realm of digital printing, UV flatbed printers have revolutionized the way we approach print production, especially when it comes to printing on a wide variety of substrates. These versatile machines offer unparalleled flexibility, enabling printers to produce high-quality images on materials ranging from rigid boards and plastics to textiles and even glass. However, achieving optimal print results isn’t solely reliant on the printer’s capabilities; it also hinges significantly on proper media pre-treatment and coating. This article delves into the fundamentals of these crucial steps, shedding light on why they are indispensable for ensuring the success of any UV flatbed printing project.
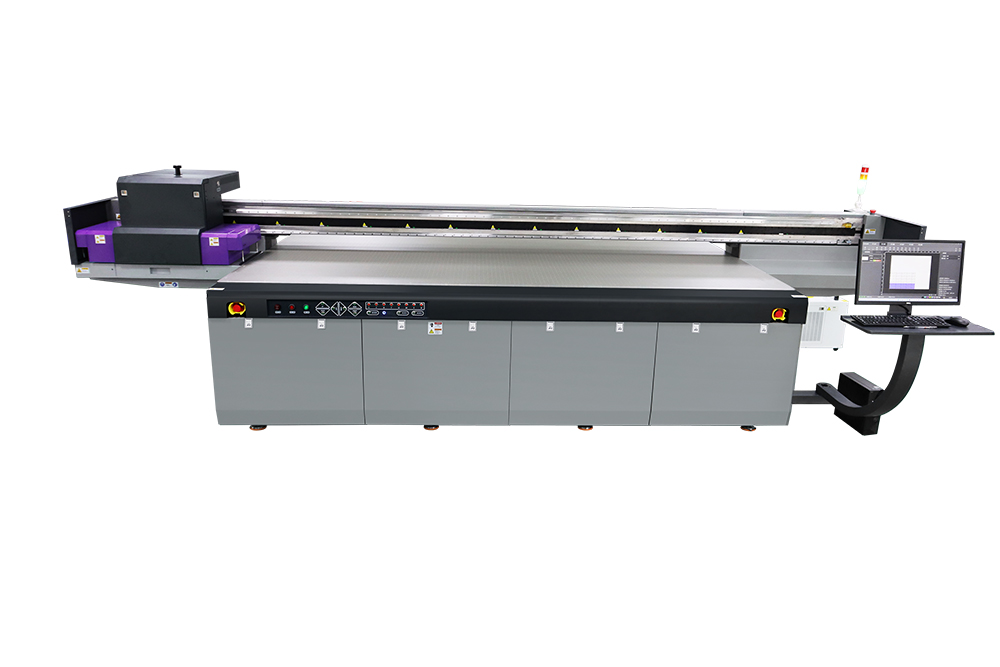
Understanding the Importance of Media Pre-Treatment
Media pre-treatment is a preparatory process that enhances the surface properties of the substrate to be printed. It is a vital step because it directly influences the adhesion of the ink to the material, the overall print quality, and the durability of the printed image. Different substrates have varying surface characteristics, such as porosity, texture, and chemical composition, which can affect how ink interacts with them.
Surface Cleaning: The first step in pre-treatment is cleaning the substrate to remove any dust, dirt, grease, or contaminants that might interfere with ink adhesion. A clean surface ensures better contact between the ink and the material, leading to more vivid colors and sharper details.
Surface Activation: Some substrates, particularly those with low surface energy, require activation to improve their wettability. This can be achieved through methods like corona treatment or plasma treatment, which modify the surface to make it more receptive to ink.
Priming: For certain materials, applying a primer can further enhance ink adhesion. Primers create a more uniform surface for the ink to bond to, reducing the risk of ink bleeding or peeling off.
The Role of Coating in UV Flatbed Printing
While pre-treatment prepares the substrate, coating adds an extra layer that optimizes the printing process and the final output. Coatings can serve multiple purposes, including enhancing image quality, providing protection against environmental factors, and enabling special effects.
Adhesion Promotion: Specialized coatings improve the bonding of the UV ink to the substrate. These coatings create a compatible layer that the ink can adhere to more effectively, ensuring that the print remains intact over time.
White Underbase: Printing on transparent or dark-colored materials can pose challenges in achieving vibrant colors and opacity. A white underbase coating solves this issue by providing a solid, opaque foundation for the colored inks to adhere to. This results in more vivid and true-to-life colors.
Scratch and UV Resistance: UV flatbed printers often use inks that cure instantly upon exposure to ultraviolet light. However, additional coatings can provide extra protection against scratches, fading, and other forms of wear and tear. These coatings extend the lifespan of the printed materials, making them suitable for outdoor or high-traffic applications.
Special Effects: Coatings can also be used to create unique textures, finishes, and special effects. For example, a glossy coating can add shine and depth to an image, while a matte coating can provide a subtle, sophisticated look. Some coatings even allow for the creation of raised textures, adding a tactile element to the printed piece.
Application Techniques for Coatings
Applying coatings correctly is as important as choosing the right type of coating. There are several methods for applying coatings, each with its own advantages and considerations.
Spray Coating: This method involves spraying the coating onto the substrate using a specialized spray gun. It is ideal for small to medium-sized projects and allows for even coverage and control over the coating thickness.
Roll Coating: Roll coating uses rollers to apply the coating evenly across the substrate. This method is suitable for larger volumes and ensures consistent coating application.
Flood Coating: In flood coating, the substrate is immersed in or passed through a bath of coating material. This technique is efficient for coating large, flat surfaces uniformly.
Screen Printing: For more targeted or patterned coating applications, screen printing can be used. It allows for precise placement of the coating, making it ideal for creating specific textures or effects.
Best Practices for Media Pre-Treatment and Coating
To ensure the best results, follow these best practices when it comes to media pre-treatment and coating:
Test Before Production: Always conduct tests on sample substrates to determine the most effective pre-treatment and coating methods. This helps avoid costly mistakes and ensures that the final product meets quality standards.
Follow Manufacturer Guidelines: Adhere to the guidelines provided by the printer and coating manufacturers. They offer specific recommendations based on the equipment and materials used.
Consistency is Key: Maintain consistent conditions throughout the pre-treatment and coating processes. Variations in temperature, humidity, and application techniques can affect the outcome.
Quality Control: Implement quality control measures to monitor the effectiveness of the pre-treatment and coating. Regularly inspect the substrates and printed materials for any signs of issues such as poor ink adhesion or coating defects.
Storage and Handling: Properly store and handle coated substrates to prevent contamination or damage. Use clean, dry, and temperature-controlled environments to maintain the integrity of the materials.
Media pre-treatment and coating are integral parts of the UV flatbed printing process. They play a critical role in ensuring that the ink adheres properly to the substrate, the print quality is high, and the final product is durable and visually appealing. By understanding the importance of these steps and following best practices, printers can achieve outstanding results that meet or exceed customer expectations.
Whether you’re printing on rigid materials, flexible substrates, or something in between, investing time and effort into proper pre-treatment and coating will pay off in the form of vibrant, long-lasting prints that stand the test of time. As technology continues to advance, so too will the methods and materials used in media pre-treatment and coating, further enhancing the capabilities of UV flatbed printers and expanding the possibilities for digital print production.