UV Flatbed Printer: The Best Practices for Loading and Unloading Materials
UV Flatbed Printer: The Best Practices for Loading and Unloading Materials
In the realm of digital printing, UV flatbed printers have emerged as a game-changer, offering unparalleled versatility, precision, and speed. These printers are designed to print directly onto a wide variety of substrates, ranging from rigid materials like wood, metal, and glass to flexible ones such as textiles and plastics. However, to harness the full potential of a UV flatbed printer, it is crucial to adhere to best practices when loading and unloading materials. This article delves into the finer details of these practices, ensuring optimal print quality, material handling efficiency, and printer longevity.
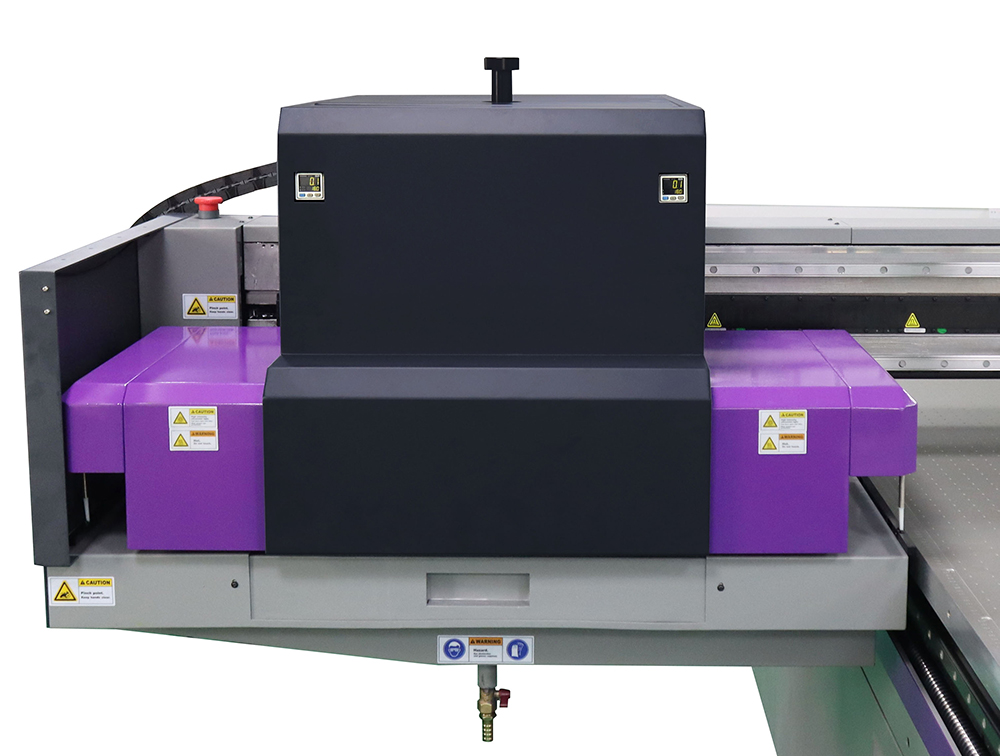
Understanding the Importance of Proper Material Handling
Proper loading and unloading of materials on a UV flatbed printer are not merely procedural steps; they are fundamental to achieving high-quality prints and maintaining the printer’s integrity. Improper handling can lead to a multitude of issues, including:
Print Quality Defects: Misaligned or warped materials can result in blurred images, streaking, and color inconsistencies.
Material Damage: Rough handling can scratch, dent, or tear sensitive substrates, rendering them unsuitable for printing.
Printer Malfunction: Incorrect loading can jam the printer, causing mechanical failures and potential downtime.
Wasted Resources: Poor handling often leads to wasted ink, substrate, and time, increasing production costs.
Best Practices for Loading Materials
Preparation
Material Selection and Inspection
Ensure that the material meets the printer’s specifications in terms of thickness, flatness, and compatibility with UV inks.
Inspect materials for defects such as warping, scratches, or contamination that could affect print quality.
Cleaning and Preparation
Clean the material surface to remove dust, debris, and fingerprints. Use a lint-free cloth and appropriate cleaners to avoid damaging the substrate.
If necessary, apply a primer or coating to enhance ink adhesion and printability.
Sizing and Cutting
Measure and cut materials accurately to fit the printer’s bed size, ensuring there is enough margin for registration marks and potential trimming.
Use high-quality cutting tools to prevent material damage.
Loading Procedure
Alignment and Positioning
Place the material on the printer bed, aligning it precisely with the guides or registration marks provided.
Use clamps or vacuum systems, if available, to secure the material and prevent movement during printing.
Software Setup
In the printer software, ensure that the material settings (such as type, thickness, and coating) are correctly configured.
Verify the print layout, including margins, bleeds, and registration marks.
Printer Calibration
Perform a test print to ensure that the printer is correctly aligned and calibrated for the loaded material.
Adjust the printer settings if necessary to achieve optimal print quality.
Best Practices for Unloading Materials
Post-Print Handling
Cooling and Drying
Allow the printed material to cool and dry thoroughly before unloading. UV inks require a certain amount of time to cure fully, as specified by the ink manufacturer.
Use fans or drying racks to accelerate the cooling process, if necessary.
Gentle Removal
Unclamp or release the vacuum system, and carefully lift the material from the printer bed.
Avoid using sharp tools or excessive force, which could scratch or damage the printed surface.
Inspection and Quality Control
Inspect the printed material for any defects, such as missed areas, color inconsistencies, or scratches.
Perform quality control checks, such as measuring color accuracy and resolution, using tools like colorimeters or spectrophotometers.
Storage and Further Processing
Proper Storage
Store the printed materials in a clean, dry environment to prevent damage from dust, moisture, or temperature fluctuations.
Stack materials flat to avoid bending or warping.
Post-Processing
If required, apply protective coatings or laminates to enhance the durability and appearance of the prints.
Trim or cut the printed materials to the final dimensions using precision tools.
Handling Sensitive Materials
For delicate substrates, such as textiles or thin plastics, use extra care during unloading and post-processing to avoid tearing or stretching.
Consider using specialized handling equipment, such as suction cups or soft-grip tools, to minimize damage.
Tips for Optimizing Material Handling Efficiency
Automation and Mechanization
Invest in automated material handling systems, such as conveyors or robotic arms, to streamline the loading and unloading process.
Use software to automate print job setup and material tracking, reducing manual errors and improving workflow efficiency.
Training and Staff Development
Train operators on proper material handling techniques, printer operation, and quality control procedures.
Encourage continuous learning and skill development to keep up with the latest advancements in UV flatbed printing technology.
Maintenance and Upkeep
Regularly clean and maintain the printer bed, clamps, and vacuum systems to ensure they function correctly and do not damage materials.
Perform routine printer maintenance, such as cleaning the print heads and校准 sensors, to maintain optimal print quality and performance.
Workflow Optimization
Optimize the workflow to minimize downtime between print jobs. This can include batching similar materials together, pre-cutting materials in advance, and using efficient scheduling software.
Implement quality control checks at multiple stages of the production process to catch potential issues early and reduce waste.
Addressing Common Challenges
Material Warping
Use thicker or more rigid substrates to reduce warping.
Apply a temporary adhesive or tape to the edges of the material to keep it flat during printing.
Consider using a heated printer bed or an environmental chamber to control temperature and humidity during printing.
Ink Adhesion Issues
Ensure that the material surface is clean and compatible with the UV inks being used.
Test different primers or coatings to find the one that provides the best ink adhesion for the specific substrate.
Adjust the ink curing time and temperature according to the ink manufacturer’s recommendations.
Printer Malfunctions
Keep a detailed log of printer malfunctions and their causes to identify patterns and prevent future occurrences.
Regularly update printer software and firmware to benefit from the latest improvements and bug fixes.
Have a maintenance contract with the printer manufacturer for timely repairs and preventive maintenance.
Conclusion
Loading and unloading materials on a UV flatbed printer is a critical aspect of the printing process that can significantly impact print quality, material handling efficiency, and printer longevity. By adhering to best practices, such as proper material preparation, precise loading procedures, gentle unloading techniques, and efficient workflow optimization, printers can harness the full potential of their UV flatbed printers. By addressing common challenges and continuously improving material handling practices, printers can achieve consistently high-quality prints, reduce waste, and enhance overall production efficiency. With the right approach, UV flatbed printing can be a powerful tool for creating stunning visuals on a wide range of substrates, meeting the diverse needs of customers in various industries.