UV Flatbed Printer: The Role of Temperature and Humidity in the Printing Process
UV Flatbed Printer: The Role of Temperature and Humidity in the Printing Process
In the realm of modern printing technology, UV flatbed printers have emerged as a versatile and efficient solution for a wide range of applications, from advertising materials to industrial labeling. These printers utilize ultraviolet (UV) light to cure ink instantly, producing high-quality, durable prints on various substrates. However, the success of the UV printing process is not solely dependent on the printer’s mechanics or ink quality; environmental factors, particularly temperature and humidity, play a crucial role in ensuring optimal print outcomes. This article delves into the intricacies of how temperature and humidity influence UV flatbed printing and highlights strategies to mitigate their potential negative effects.
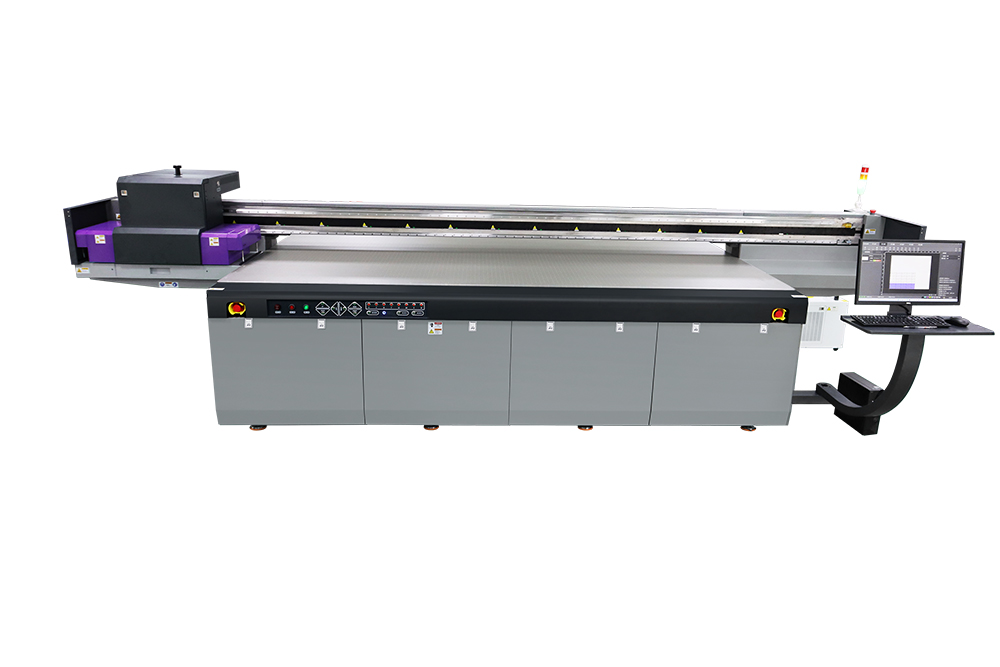
The Science Behind UV Printing
UV flatbed printers work by depositing ink onto a substrate and then immediately curing it with UV light. This curing process involves the polymerization of the ink’s resin components, transforming the liquid ink into a solid film. The speed and efficiency of this reaction are vital for achieving sharp, vibrant prints with excellent adhesion and durability.
The Impact of Temperature
Temperature is a fundamental factor that significantly affects the performance of UV inks and the overall printing process. Here’s how:
Ink Viscosity
Ink viscosity, or its resistance to flow, is directly influenced by temperature. At lower temperatures, UV inks become thicker, which can lead to poor ink flow through the printer’s nozzles, resulting in uneven ink distribution and potential nozzle clogging. Conversely, high temperatures can cause the ink to become too thin, leading to excessive ink spread, reduced image sharpness, and even ink dripping.
Curing Efficiency
The UV curing process relies on a chemical reaction that is temperature-sensitive. Ideally, UV inks require a stable operating temperature within a specific range (usually around 20-25°C) to cure properly. Lower temperatures can slow down the polymerization reaction, leading to incomplete curing and reduced print durability. On the other hand, excessively high temperatures can accelerate the curing process, potentially causing the ink to cure prematurely on the printhead or within the ink delivery system, leading to print defects.
Substrate Behavior
Temperature also affects the behavior of the substrate. Different materials expand and contract with temperature changes, which can impact print registration and dimensional stability. For instance, printing on a cold substrate might result in ink cracking or poor adhesion, while a hot substrate could cause the ink to spread excessively, affecting image clarity.
Managing Temperature in UV Printing
Given the importance of temperature control, several strategies can be employed to maintain optimal conditions:
Climate-Controlled Environment: Operating the UV flatbed printer within a climate-controlled environment is crucial. This involves maintaining a consistent temperature and minimizing temperature fluctuations.
Heating and Cooling Systems: Installing heating and cooling systems, such as HVAC units, can help regulate the ambient temperature within the printing area.
Substrate Preheating: For certain materials, preheating the substrate to the recommended temperature before printing can ensure better ink adhesion and reduce the risk of ink cracking.
Ink Temperature Management: Some printer models come equipped with ink temperature control systems that maintain the ink at a constant temperature, ensuring optimal viscosity and flow.
The Role of Humidity
Humidity, or the amount of moisture in the air, is another critical environmental factor that can profoundly affect UV printing.
Ink Absorption
High humidity levels can cause the substrate to absorb more moisture, leading to swelling or warping. This can result in ink bleeding, poor image registration, and reduced print quality. Conversely, low humidity can cause the substrate to dry out, leading to ink cracking or poor adhesion.
Static Electricity
Low humidity environments are prone to static electricity, which can cause dust and debris to adhere to the substrate or printhead, leading to print defects. Static can also disrupt the ink flow, causing nozzle misfires and uneven ink distribution.
Ink Drying
Humidity can also influence the ink’s drying process. In high-humidity conditions, the ink may take longer to dry, which can affect print quality and increase the risk of smudging. On the other hand, excessively low humidity can cause the ink to dry too quickly on the printhead, leading to clogging and reduced print quality.
Managing Humidity in UV Printing
To mitigate the effects of humidity on the UV printing process, the following strategies can be implemented:
Humidity Control Systems: Installing humidity control systems, such as dehumidifiers or humidifiers, can help maintain a stable humidity level within the printing environment. The ideal humidity range for UV printing typically falls between 40-60% relative humidity.
Substrate Storage: Storing substrates in a controlled environment with stable humidity levels before printing can help prevent moisture-related issues.
Anti-Static Devices: Using anti-static devices, such as ionizers, can help neutralize static electricity, reducing the risk of dust adhesion and ink flow disruptions.
Proper Ventilation: Ensuring proper ventilation in the printing area can help remove excess moisture and maintain a balanced humidity level.
The Synergy Between Temperature and Humidity
Temperature and humidity are intertwined factors that must be managed in tandem. A balance between these two elements is essential for achieving optimal print quality. For example, high temperatures combined with high humidity can lead to excessive ink spread and substrate swelling, while low temperatures and low humidity can cause ink cracking and static issues.
Real-World Applications and Challenges
In various industries, such as advertising, signage, and industrial manufacturing, UV flatbed printers are used to produce a wide range of products, including banners, posters, labels, and decorative items. Each application may present unique challenges related to temperature and humidity control. For instance, printing on flexible materials like vinyl or fabric may require careful management of both temperature and humidity to prevent material distortion and ink bleeding.
Advanced Solutions and Future Trends
As UV printing technology continues to evolve, manufacturers are developing more sophisticated systems to better manage environmental factors. Some printers now feature advanced sensors that monitor temperature and humidity in real-time, adjusting print parameters accordingly. Additionally, the development of new ink formulations and substrate treatments is aimed at improving ink adhesion and durability across a wider range of environmental conditions.
Conclusion
In conclusion, temperature and humidity are critical factors that significantly influence the performance of UV flatbed printers. Proper management of these environmental conditions is essential for achieving high-quality, durable prints. By implementing strategies such as climate control, substrate preheating, ink temperature management, and humidity control, printer operators can mitigate the negative effects of temperature and humidity, ensuring optimal print outcomes. As UV printing technology continues to advance, the development of more sophisticated systems and materials will further enhance the ability to control these environmental factors, pushing the boundaries of what is possible in the world of digital printing.