UV Flatbed Printer: Tips for Achieving Consistent Print Results Across Multiple Jobs
In the realm of digital printing, UV flatbed printers have revolutionized the way we approach print production, especially for a wide range of materials and applications. From signage and graphics to decorative items and packaging, UV flatbed printers offer versatility, high resolution, and durability. However, achieving consistent print results across multiple jobs can be a challenge, even for seasoned professionals. Inconsistencies can stem from various factors, including ink performance, media handling, printer settings, and environmental conditions. To help you master the art of consistency, here are some comprehensive tips and best practices.
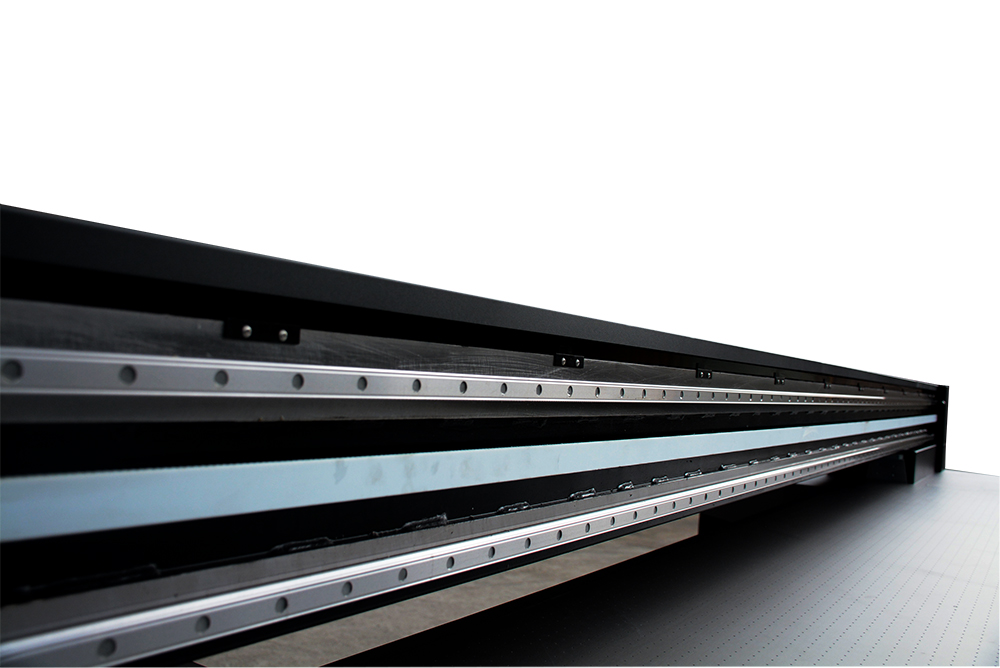
1. Understanding Your Printer and Materials
Printer Calibration
Regular calibration of your UV flatbed printer is crucial for maintaining consistent print quality. Calibration ensures that the printer heads are aligned correctly, the ink droplets are deposited accurately, and the colors are mixed precisely. Most modern UV printers come with built-in calibration tools, but manual checks and adjustments may also be necessary, especially after replacing printer heads or performing major maintenance.
Material Compatibility
Not all materials are created equal, and their compatibility with UV inks can vary significantly. It’s essential to test different substrates before committing to large-scale production. Factors such as material absorbency, surface texture, and chemical composition can affect ink adhesion, drying times, and overall print quality. Keep a log of your test results to refer back to when choosing materials for future jobs.
2. Ink Management
Ink Quality and Consistency
Using high-quality UV-curable inks is fundamental to achieving consistent print results. Inferior inks may lead to color fading, poor adhesion, or clogging of printer heads. Additionally, ensure that the ink is stored correctly, away from direct sunlight and extreme temperatures, as these factors can alter ink properties over time.
Ink Mixing and Circulation
UV printers often use a system of ink tanks and cartridges. Ensuring that the ink is well-mixed and circulated properly can prevent settling and ensure that the ink color remains consistent throughout the print job. Some printers have automatic ink stirring mechanisms, while others may require manual agitation before starting a job.
3. Printer Settings and Profiles
Custom Profiles
Creating custom printer profiles for different materials and job types can significantly enhance consistency. These profiles include settings such as ink coverage, print speed, layer thickness, and curing parameters. By tailoring these settings to each specific job, you can optimize print quality and reduce the risk of inconsistencies.
Resolution and Pass Count
The resolution and pass count settings directly impact the detail and quality of the print. Higher resolutions and more passes generally result in better print quality but can also increase production time. Finding the right balance between quality and efficiency is key. For most applications, a resolution of 1200 dpi with an appropriate pass count provides excellent results without excessive production time.
4. Curing Process
UV Lamp Performance
The UV lamps are responsible for curing the ink almost instantly after it’s deposited on the material. Over time, UV lamps can degrade, leading to inconsistent curing and potential print quality issues. Regularly check and replace UV lamps as needed, following the manufacturer’s recommendations.
Curing Distance and Time
The distance between the UV lamp and the printed surface, as well as the exposure time, are critical factors in the curing process. Incorrect settings can result in undercured ink (which may smudge or remain tacky) or overcured ink (which can cause brittleness or cracking). Conduct tests to determine the optimal curing distance and time for each material and ink combination.
5. Environmental Controls
Temperature and Humidity
Environmental conditions can have a substantial impact on print quality and consistency. High humidity can affect ink drying and adhesion, while extreme temperatures can alter ink viscosity and printer performance. Aim to maintain a controlled environment with stable temperature and humidity levels to minimize these effects.
Dust and Contaminants
Dust and other contaminants can settle on the printer heads, media, and UV lamps, leading to print defects. Regular cleaning of the printer and its surroundings is essential. Implement a cleaning schedule and use appropriate tools and materials to avoid damaging delicate printer components.
6. Pre- and Post-Processing
Media Preparation
Proper media preparation is often overlooked but is vital for consistent print results. Ensure that the material is clean, dry, and free of any defects before printing. For some materials, applying a primer or coating can improve ink adhesion and overall print quality.
Finishing Touches
Post-processing steps, such as cutting, laminating, or applying a protective coating, can also affect the final appearance and durability of the print. Choose finishing materials and methods that are compatible with the printed surface and the intended application.
7. Quality Control and Maintenance
Regular Maintenance
Implementing a regular maintenance schedule can prevent many common issues that lead to inconsistent print results. This includes cleaning printer heads, checking ink levels, inspecting UV lamps, and lubricating moving parts. Keep a detailed maintenance log to track tasks and ensure nothing is overlooked.
Quality Control Checks
Performing quality control checks at various stages of the printing process can help identify and address issues early on. Use color calibration tools, resolution test charts, and visual inspections to monitor print quality consistently.
Achieving consistent print results with a UV flatbed printer requires attention to detail, careful planning, and ongoing maintenance. By understanding your printer and materials, managing ink effectively, fine-tuning printer settings, controlling the curing process, maintaining optimal environmental conditions, and implementing thorough pre- and post-processing procedures, you can significantly improve the consistency of your print jobs. Regular quality control checks and maintenance are the backbone of a reliable and efficient printing operation. With these practices in place, you’ll be well-equipped to deliver high-quality prints that meet or exceed your customers’ expectations.