UV Flatbed Printer: Tips for Achieving Smooth and Even Ink Coverage
UV Flatbed Printer: Tips for Achieving Smooth and Even Ink Coverage
In the realm of digital printing, UV flatbed printers have revolutionized the way businesses produce high-quality graphics and images on a wide variety of substrates. These versatile machines utilize ultraviolet (UV) light to cure ink instantly, enabling printing on rigid materials such as glass, metal, wood, plastic, and more. However, achieving smooth and even ink coverage with a UV flatbed printer requires careful attention to detail and a thorough understanding of the printing process. In this article, we will explore several key tips and strategies to help you optimize your UV flatbed printer for the best possible results.
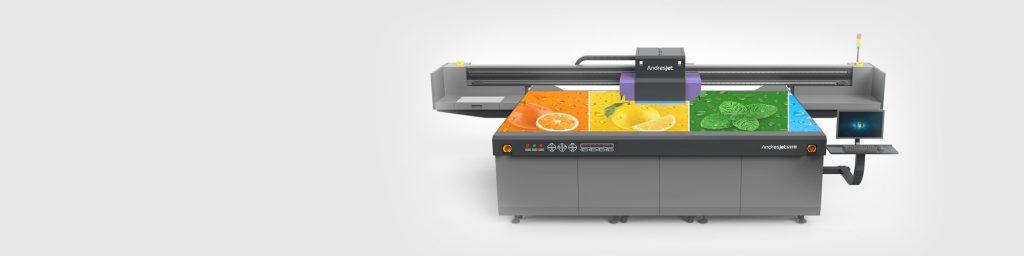
1. Understand Your Printer’s Capabilities
Before diving into the intricacies of ink coverage, it is crucial to familiarize yourself with your UV flatbed printer’s specifications and capabilities. Each printer model has its unique features, limitations, and recommended settings. Refer to the manufacturer’s manual and technical documents to gain a comprehensive understanding of your printer’s ink types, curing systems, printable materials, and supported resolutions.
Understanding the printer’s ink delivery system (such as piezo or thermal inkjet technology) and its color management options will also play a significant role in achieving consistent ink coverage. Additionally, be aware of the printer’s maximum print size and the thickness of materials it can handle, as these factors can impact your design and preparation processes.
2. Prepare Your Substrate Properly
The choice and preparation of your substrate are fundamental to achieving smooth and even ink coverage. Different materials absorb ink differently, and some may require specific pretreatments to ensure proper adhesion and curing.
Cleaning: Ensure that the substrate is clean and dust-free. Any dirt, oil, or grease on the surface can affect ink adhesion, leading to uneven coverage.
Pretreatment: Depending on the material, you may need to apply a primer or coating to enhance ink adhesion. For example, porous materials like wood or stone may require a sealing coat to prevent ink from being absorbed too quickly, while non-porous materials like glass or metal might need an adhesion promoter.
Flatness: Ensure the substrate is flat and level. Any warping or unevenness can cause the print head to make inconsistent contact, resulting in uneven ink deposition.
3. Optimize Ink and Color Management
Achieving accurate and consistent color reproduction is vital for smooth and even ink coverage. This involves careful calibration of your printer and the use of appropriate color management tools.
Profiling: Use ICC (International Color Consortium) profiles specific to your printer, ink, and substrate combination. These profiles help translate colors accurately from your design software to the printed output.
Ink Viscosity: Monitor and adjust the ink viscosity as needed. Ink that is too thick can result in heavy, uneven deposits, while ink that is too thin may not provide adequate coverage.
Color Calibration: Regularly calibrate your printer to maintain color accuracy. This involves printing test charts and adjusting the printer’s settings based on the results.
4. Adjust Print Settings for Optimal Coverage
The print settings you choose will significantly impact ink coverage. Experimenting with various settings is often necessary to find the optimal balance for your specific application.
Resolution: Higher resolutions generally produce smoother and more detailed prints, but they also require more ink and longer print times. Find the resolution that best suits your needs without unnecessarily increasing costs and production time.
Dot Gain: Dot gain refers to the expansion of ink dots on the substrate during printing. Adjusting dot gain settings can help control ink spread and ensure even coverage.
Pass Count: The number of passes the print head makes over the substrate affects ink deposition. More passes can lead to smoother coverage but also increase production time.
Ink Layering: Some UV flatbed printers allow for multi-layer printing, where different colors or effects are printed in separate passes. Properly layering ink can enhance color saturation and smoothness.
5. Control Ink Curing
The curing process is critical in UV printing, as it determines how well the ink adheres to the substrate and its overall durability.
UV Intensity: Ensure that the UV lamps are at the correct intensity for the ink and substrate being used. Insufficient curing can lead to poor adhesion and ink smearing, while excessive curing can cause overheating and damage to the material.
Curing Time: The amount of time the ink is exposed to UV light also plays a role. Follow the manufacturer’s recommendations for curing times and adjust as necessary based on your specific application.
Temperature and Humidity: Maintain a stable environment with appropriate temperature and humidity levels. Variations in these conditions can affect ink curing and overall print quality.
6. Maintain Your Printer Regularly
Regular maintenance is essential for keeping your UV flatbed printer in optimal condition and ensuring consistent ink coverage.
Cleaning: Regularly clean the print head, platen, and other critical components to prevent ink buildup and ensure smooth operation.
Calibration: Perform routine calibrations to maintain color accuracy and print quality.
Replacement Parts: Keep track of the usage of consumables such as ink cartridges, UV lamps, and maintenance kits. Replace them as recommended by the manufacturer to avoid degradation in print quality.
Software Updates: Keep your printer’s software and drivers up to date to ensure compatibility with the latest design software and to benefit from any performance improvements or bug fixes.
7. Experiment and Iterate
Achieving the perfect ink coverage often requires a process of experimentation and iteration. Don’t be afraid to test different settings, substrates, and pretreatments to find the combination that works best for your specific needs.
Test Prints: Start with small test prints to evaluate ink coverage, color accuracy, and overall print quality before committing to a full-scale production run.
Keep Records: Maintain a detailed record of your tests, including the settings used, any pretreatments applied, and the results observed. This will help you track your progress and identify the most effective strategies.
Seek Expert Advice: If you’re struggling to achieve the desired results, don’t hesitate to consult with the printer’s manufacturer or a printing expert. They can provide valuable insights and guidance based on their experience and expertise.
Conclusion
Achieving smooth and even ink coverage with a UV flatbed printer requires a combination of careful preparation, attention to detail, and a thorough understanding of the printing process. By following the tips outlined in this article, you can optimize your printer for the best possible results, ensuring that your prints are of the highest quality and meet your customers’ expectations. Remember to experiment, iterate, and seek expert advice when needed, and you’ll be well on your way to mastering the art of UV flatbed printing.