UV Flatbed Printer: Tips for Improving Color Saturation
UV Flatbed Printer: Tips for Improving Color Saturation
In the realm of digital printing, UV flatbed printers have revolutionized the way images are reproduced on various surfaces. These printers utilize ultraviolet (UV) light to instantly cure or dry ink as it is applied, resulting in vibrant, durable prints. One of the key factors that determine the quality of prints produced by UV flatbed printers is color saturation. Color saturation refers to the intensity or purity of a color, and achieving high color saturation is crucial for producing eye-catching and visually appealing prints. In this article, we will explore several tips for improving color saturation when using a UV flatbed printer.
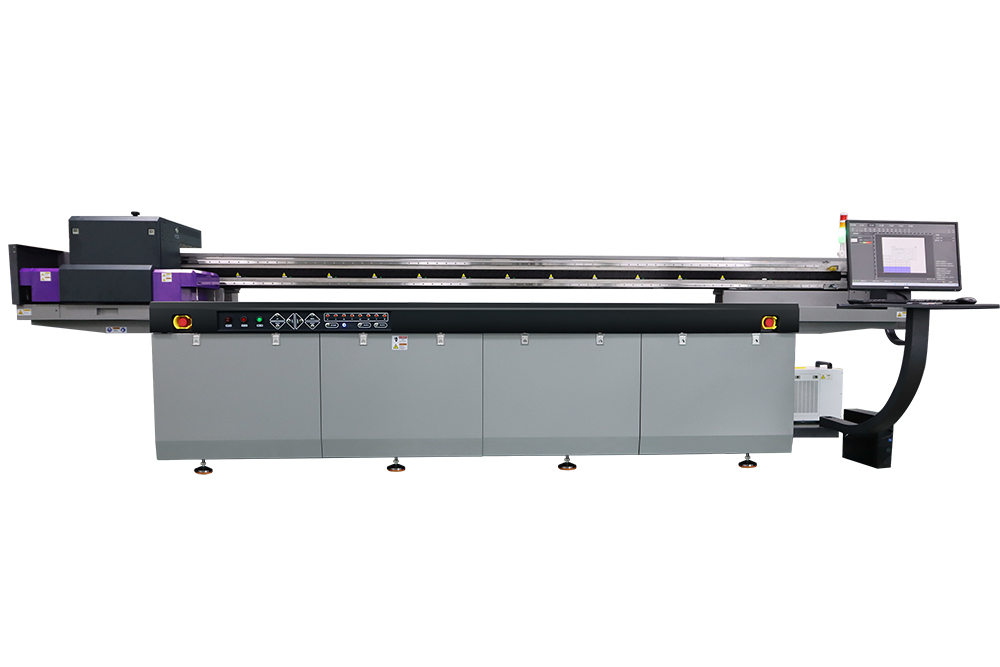
1. Understand Color Management
The foundation of achieving optimal color saturation lies in understanding and implementing proper color management. Color management involves the controlled conversion of color data from one device to another, ensuring consistency and accuracy across different mediums. When working with a UV flatbed printer, it is essential to calibrate the printer regularly to maintain accurate color reproduction. This includes profiling the printer to create an ICC (International Color Consortium) profile, which describes the printer’s color capabilities and ensures that colors are reproduced consistently.
Moreover, using color management software can help refine and enhance color saturation. These software tools allow users to adjust color settings, such as hue, saturation, and brightness, to achieve the desired visual impact. By fine-tuning these parameters, users can maximize color saturation while maintaining color accuracy.
2. Optimize Ink and Print Settings
The type and quality of ink used in a UV flatbed printer significantly impact color saturation. UV-curable inks are specifically designed to cure under UV light, resulting in vibrant and durable prints. To improve color saturation, it is crucial to use high-quality UV inks that are formulated to produce rich, intense colors. Additionally, some ink manufacturers offer inks with enhanced color saturation properties, which can further elevate the visual quality of prints.
Print settings also play a vital role in achieving optimal color saturation. Adjusting the ink density or ink limit settings can help increase color saturation. However, it is important to strike a balance, as excessive ink deposition can lead to ink pooling or bleeding, which can negatively affect print quality. Experimenting with different ink density settings and conducting test prints can help determine the optimal ink deposition for achieving the desired color saturation.
3. Utilize High-Resolution Printing
The resolution of a print directly impacts its overall quality, including color saturation. Higher resolution prints contain more dots per inch (DPI), resulting in smoother gradients and sharper details. When printing with a UV flatbed printer, opting for higher resolution settings can help improve color saturation by allowing for a more precise deposition of ink droplets. This results in smoother color transitions and more vibrant hues.
However, it is important to note that higher resolution printing may also increase print time and ink consumption. Therefore, it is advisable to balance resolution settings based on the specific requirements of the print job and the capabilities of the printer.
4. Pre-Treatment and Surface Preparation
The surface on which the ink is applied can greatly influence color saturation. In some cases, the porosity or texture of the material can cause ink to spread unevenly, resulting in reduced color saturation. To mitigate this issue, pre-treatment and surface preparation are crucial steps in the printing process.
Applying a pre-treatment coating to the substrate can help improve ink adhesion and enhance color saturation. These coatings create a more uniform surface for the ink to adhere to, ensuring that the ink is evenly distributed and cured. Additionally, pre-treatment coatings can help reduce the risk of ink bleeding or spreading, further improving print quality.
Proper surface preparation, such as cleaning and degreasing the substrate, is also essential for achieving optimal color saturation. Dust, dirt, or oils on the surface can interfere with ink adhesion, leading to reduced color intensity. By ensuring that the surface is clean and properly prepared, the ink can adhere more effectively, resulting in improved color saturation.
5. Post-Curing Techniques
Post-curing is an additional step in the UV printing process that can help enhance color saturation. After the initial UV curing process, post-curing involves exposing the printed material to additional UV light to further cure the ink. This additional curing step can help improve ink adhesion and enhance the durability of the print.
Moreover, post-curing can also help intensify color saturation. The additional exposure to UV light can further cure the ink, resulting in richer and more vibrant colors. However, it is important to note that excessive post-curing can lead to ink yellowing or degradation, so it is crucial to find the right balance based on the specific ink and substrate being used.
6. Experiment with Print Modes and Techniques
UV flatbed printers often offer various print modes and techniques that can be utilized to improve color saturation. For example, some printers offer a “high saturation” or “vivid color” mode, which optimizes print settings to produce more vibrant and intense colors. Experimenting with different print modes can help users achieve the desired color saturation without compromising print quality.
Additionally, techniques such as layering or double-hitting can also be employed to enhance color saturation. Layering involves applying multiple passes of ink to the same area, building up color intensity. Double-hitting involves printing the same area twice with slightly offset passes, creating a denser ink deposition and resulting in more vibrant colors.
Conclusion
Achieving high color saturation is a key factor in producing visually stunning prints with a UV flatbed printer. By understanding and implementing proper color management, optimizing ink and print settings, utilizing high-resolution printing, preparing the surface adequately, employing post-curing techniques, and experimenting with different print modes and techniques, users can significantly improve color saturation in their prints. With these tips, UV flatbed printer users can unlock the full potential of their printers and produce prints that are not only visually appealing but also durable and long-lasting.