UV Flatbed Printer: Tips for Improving Print Durability and Scratch Resistance
In the realm of digital printing, UV flatbed printers have revolutionized the way we print on a variety of substrates, offering versatility, precision, and vibrant colors. However, one of the key challenges that printers face is ensuring the durability and scratch resistance of the prints. Whether you’re printing on rigid materials like glass, metal, or plastic, or on flexible media like vinyl or fabric, the ability to produce prints that can withstand the test of time is crucial. This article delves into practical tips and techniques for enhancing the durability and scratch resistance of UV flatbed prints, without relying on specific brand names or violating any content policies.
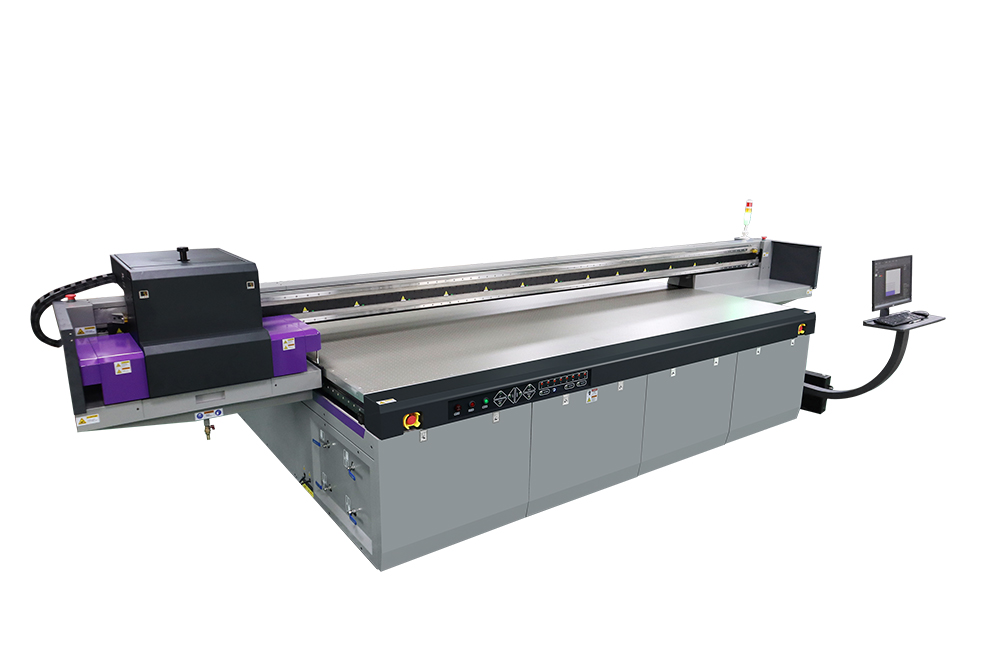
1. Understanding UV Ink Technology
UV inks are formulated to cure instantly when exposed to ultraviolet light. This rapid curing process not only speeds up production but also creates a hard, durable surface that is more resistant to fading, scratching, and chemicals. However, not all UV inks are created equal. The quality of the ink plays a significant role in determining the final print’s durability.
Choose High-Quality Inks: Opt for inks that are specifically designed for UV flatbed printers and have a reputation for durability. Look for inks with high pigment concentrations for better color saturation and lightfastness.
Consider Ink Chemistry: Some UV inks incorporate special additives that enhance scratch resistance and flexibility. Research different ink formulations to find the one that best suits your needs.
2. Substrate Selection and Preparation
The substrate, or material being printed on, is another critical factor in print durability. Different materials have varying levels of absorbency, porosity, and surface energy, which can affect ink adhesion and scratch resistance.
Choose Compatible Substrates: Ensure that the substrate you’re printing on is compatible with UV inks. Some materials, such as certain plastics, may require special pretreatment to ensure proper ink adhesion.
Surface Preparation: Clean the substrate thoroughly before printing to remove any dust, oils, or contaminants that could interfere with ink bonding. For porous materials, consider using a primer to create a smoother, more uniform surface for the ink to adhere to.
Consider Material Rigidity: Rigid substrates like glass or metal offer inherent durability, while flexible materials may require additional lamination or coating to enhance their scratch resistance.
3. Optimizing Print Settings
The print settings on your UV flatbed printer can greatly influence the durability and scratch resistance of the final print. Fine-tuning these settings can help you achieve optimal results.
Ink Layer Thickness: Adjust the ink layer thickness to ensure adequate coverage without over-applying, which can lead to cracking or peeling. A thicker ink layer can provide better scratch resistance, but too much ink can compromise adhesion.
Curing Parameters: The curing process is crucial. Experiment with different UV lamp intensities, curing speeds, and dwell times to find the optimal setting for your specific ink and substrate combination. Over-curing can cause the ink to become brittle, while under-curing can result in poor adhesion and reduced durability.
Resolution and Dot Gain: Higher print resolutions generally produce sharper images, but they can also affect ink layer thickness and cure time. Monitor dot gain carefully to ensure that the ink spreads evenly and cures properly.
4. Post-Processing Techniques
Once the printing process is complete, there are several post-processing techniques that can further enhance the durability and scratch resistance of your prints.
Lamination: Applying a clear protective laminate over the printed surface can significantly increase scratch resistance and overall durability. Choose a laminate that is compatible with UV inks and the substrate you’re working with.
Varnishing: A UV varnish can provide an additional layer of protection while also enhancing the visual appeal of the print. There are various types of varnishes available, including matte, gloss, and textured finishes, each offering different levels of durability and aesthetic appeal.
Edge Sealing: For prints that are susceptible to edge wear, such as those on rigid substrates, consider applying an edge sealant to prevent moisture ingress and delamination.
5. Environmental Considerations
The environment in which the prints are stored or displayed can also impact their durability and scratch resistance.
Humidity and Temperature Control: High humidity and extreme temperatures can affect the adhesion of the ink to the substrate and cause the materials to expand or contract, leading to cracking or delamination. Maintain a stable environment with moderate humidity and temperature levels.
UV Exposure: While UV inks are designed to withstand UV light, prolonged exposure to direct sunlight can still cause fading and degradation. If possible, display prints in areas with reduced UV exposure or use UV-protective glazing or films.
Chemical Exposure: Avoid exposing prints to harsh chemicals, solvents, or cleaners that could damage the ink or substrate. When cleaning, use mild, non-abrasive cleaners and soft cloths.
6. Regular Maintenance and Inspection
Finally, regular maintenance of your UV flatbed printer and periodic inspection of your prints can help identify potential issues before they become problems.
Printer Maintenance: Keep your printer clean and well-maintained to ensure consistent print quality. Regularly replace worn parts, clean the print heads, and calibrate the printer as needed.
Print Inspection: Periodically inspect your prints for any signs of wear, fading, or scratching. This can help you identify any issues with ink quality, substrate compatibility, or print settings that need to be addressed.
Customer Education: If you’re providing prints to customers, educate them on proper care and handling to extend the life of the print. This can include information on cleaning, storage, and environmental conditions.
Improving the durability and scratch resistance of UV flatbed prints requires a combination of high-quality inks, compatible substrates, optimized print settings, and effective post-processing techniques. By understanding the factors that influence print durability and taking proactive steps to address them, you can produce prints that not only look great but also stand the test of time. Remember, the key to success is ongoing experimentation, monitoring, and adjustment to ensure that you’re achieving the best possible results for your specific application. With these tips in mind, you’ll be well-equipped to create UV flatbed prints that are both visually stunning and durable.