UV Flatbed Printer: Tips for Printing on Canvas and Fabric
UV Flatbed Printer: Tips for Printing on Canvas and Fabric
In the realm of digital printing, UV flatbed printers have revolutionized the way we approach printing on various media, especially when it comes to canvas and fabric. These versatile printers utilize ultraviolet light to cure the inks instantly, resulting in vibrant, durable, and weather-resistant prints. Whether you’re a professional printer, an artist, or a small business owner looking to expand your product offerings, mastering the art of printing on canvas and fabric with a UV flatbed printer can open up a world of creative possibilities. In this article, we’ll delve into the essential tips and techniques to ensure successful and stunning prints on these materials.
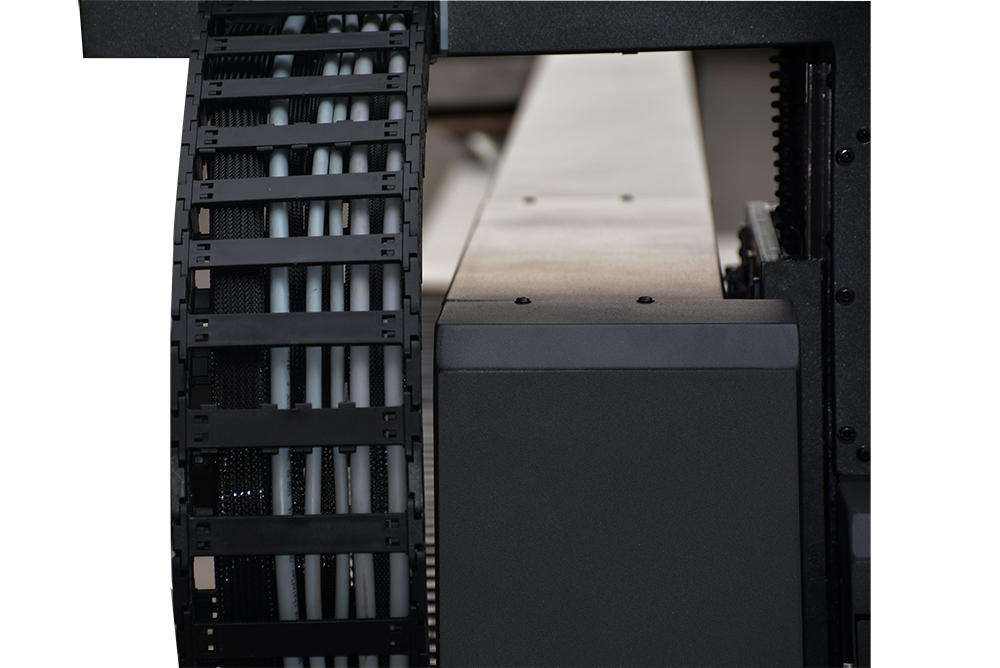
Understanding the Basics
Before diving into the specifics, it’s crucial to understand the fundamentals of UV flatbed printing and the unique characteristics of canvas and fabric as printing substrates.
UV Flatbed Printer Technology:
UV flatbed printers are designed to print directly onto flat or slightly curved surfaces. They use UV-curable inks that solidify immediately upon exposure to UV light, allowing for precise and detailed prints. This technology eliminates the need for drying time and produces prints that are resistant to fading, scratching, and water damage.
Canvas and Fabric as Substrates:
Canvas: Typically made from cotton or a cotton-polyester blend, canvas offers a textured surface that adds depth and artistic appeal to prints. It’s often used for fine art reproductions, murals, and decorative pieces.
Fabric: Fabrics like polyester, silk, and cotton have varying textures, absorbency levels, and stretch factors, which can affect the printing process. Fabrics are commonly used for fashion, home decor, and promotional items.
Preparation is Key
Success in UV printing on canvas and fabric starts with proper preparation.
Material Selection:
Choose high-quality materials that are compatible with UV inks. Ensure the canvas or fabric is clean, dust-free, and free from any oils or contaminants that could interfere with ink adhesion.
For fabrics, consider pre-treating them with a coating or primer designed to enhance ink absorption and reduce bleeding.
Printer Settings:
Adjust the printer’s DPI (dots per inch) setting to match the material’s texture and desired print quality. Higher DPI settings will produce finer details but may require longer print times.
Calibrate the printer regularly to maintain color accuracy and consistency.
Handling and Stretching:
For canvas, ensure it is properly stretched and mounted on a frame to prevent wrinkles and ensure even ink distribution.
Fabrics should be taut but not overly stretched, as excessive tension can cause distortion in the print.
Ink and Color Management
Achieving the desired colors and print quality involves careful management of inks and color profiles.
Ink Selection:
Use UV-curable inks specifically formulated for the type of material you’re printing on. These inks are designed to adhere well and cure properly on different surfaces.
Consider using specialized inks for vibrant colors, such as neon or metallic, to add unique effects to your prints.
Color Calibration:
Create and save custom ICC profiles (International Color Consortium) for your specific printer-material combination. This ensures that the colors on your screen match the colors in your print.
Regularly print test swatches and adjust the color settings as needed to maintain consistency.
Printing Techniques
The actual printing process requires attention to detail and a few specialized techniques for optimal results.
Test Prints:
Always perform test prints on scrap material before starting a full print job. This allows you to fine-tune the printer settings, check for color accuracy, and ensure proper ink coverage.
Layering and Passes:
For fabrics with high absorbency, consider using multiple thin layers of ink rather than a single thick layer. This helps prevent ink bleeding and ensures better color saturation.
Adjust the number of print passes to control the amount of ink deposited. More passes can result in richer colors but may also increase print time.
Curing:
Proper curing is crucial. Ensure the UV lights are set to the correct intensity and exposure time for the type of ink and material being used.
Overcuring can cause the material to become brittle, while undercuring may result in ink that is easily scratched or smudged.
Post-Processing
The final step in the printing process is post-processing, which can enhance the durability and appearance of your prints.
Cleaning:
Gently clean the printed surface to remove any excess ink or debris. Use a soft, lint-free cloth and a mild cleaning solution specifically designed for UV-printed materials.
Finishing:
For canvas, consider applying a protective varnish or coating to enhance the colors and provide additional durability.
Fabrics may require heat setting to fix the inks permanently. Follow the manufacturer’s guidelines for the specific fabric type.
Quality Control:
Inspect each print carefully for any defects or inconsistencies. Address any issues immediately to avoid wasting materials and time.
Creative Applications
The versatility of UV flatbed printing on canvas and fabric opens up endless creative applications.
Art Reproductions:
High-resolution UV printing allows for detailed reproductions of artwork, preserving the original’s colors and texture.
Custom Fashion:
Print unique designs on fabrics for custom clothing, accessories, and even shoes. UV printing offers the ability to create intricate patterns and vibrant colors that stand out.
Home Decor:
Personalize home decor items such as throw pillows, curtains, and wall art with custom prints. UV printing ensures the designs are long-lasting and resistant to everyday wear and tear.
Promotional Items:
Utilize UV printing to create eye-catching promotional materials such as banners, flags, and tablecloths. The durability of UV-printed fabrics makes them ideal for outdoor events and long-term display.
Environmental Considerations
As with any printing process, it’s important to consider the environmental impact of UV flatbed printing.
Ink Disposal:
Properly dispose of used inks and cleaning solutions according to local regulations. Many UV-curable inks are more environmentally friendly than traditional solvent-based inks, but it’s still crucial to handle them responsibly.
Energy Efficiency:
Opt for printers with energy-saving features and efficient UV curing systems. Reducing energy consumption not only lowers costs but also reduces your carbon footprint.
Material Choice:
Choose sustainable materials whenever possible. For example, opt for organic cotton canvas or recycled polyester fabrics.
Conclusion
UV flatbed printing on canvas and fabric offers a world of creative possibilities, combining advanced technology with the beauty of traditional materials. By following the tips outlined in this article, you can ensure that your prints are not only visually stunning but also durable and long-lasting. Whether you’re a seasoned professional or just starting out in the world of digital printing, mastering the art of UV flatbed printing will open up new avenues for creativity and business growth. So, experiment with different techniques, explore new materials, and let your imagination run wild as you create unique and captivating prints that stand the test of time.