UV Flatbed Printer: Tips for Printing on Different Materials
In the ever-evolving world of digital printing, UV flatbed printers have emerged as versatile and powerful tools, capable of printing high-quality images directly onto a wide array of materials. From rigid substrates like wood, metal, and glass to flexible media such as textiles and plastics, UV flatbed printers offer unparalleled precision, speed, and versatility. However, achieving optimal print results on these diverse materials requires a nuanced understanding of the specific characteristics and challenges associated with each. This article aims to provide practical tips for printing on different materials using UV flatbed printers, ensuring that your prints are not only visually stunning but also durable and functional.
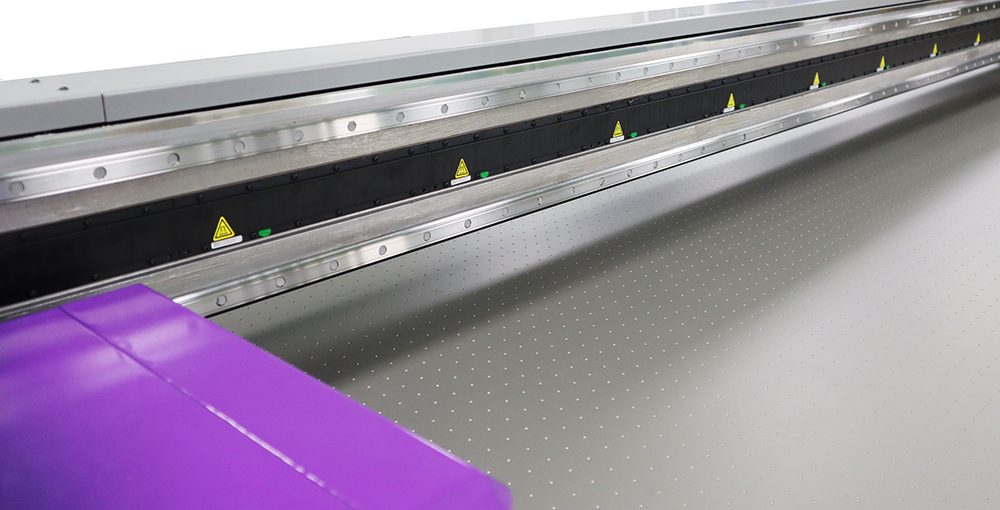
Understanding UV Flatbed Printer Technology
Before diving into the tips, it’s essential to grasp the basics of UV flatbed printer technology. UV flatbed printers use ultraviolet (UV) curable inks that instantly cure (or dry) when exposed to UV light. This curing process allows for instant printing without the need for heat drying, making it suitable for heat-sensitive materials. The flatbed design enables these printers to accommodate a variety of substrates, from thin films to thick, rigid panels, without the need for special feeding mechanisms.
Material Preparation: The Foundation for Success
Surface Cleanliness:
Ensuring that the printing surface is clean and free of contaminants is crucial. Dirt, grease, or dust can interfere with ink adhesion, leading to poor print quality. Use appropriate cleaners and cloths designed for the specific material to avoid damaging the surface.
Surface Treatment:
Some materials may require a pretreatment to enhance ink adhesion. This could involve priming, sanding, or applying an adhesive promoter. For example, plastics often benefit from a primer to ensure the inks bond properly.
Flatness and Stability:
UV flatbed printers require a flat and stable surface for optimal printing. Warped or uneven materials can lead to print distortion. When working with flexible materials, consider using a rigid backing to maintain flatness during printing.
Tips for Printing on Different Materials
Wood
Material Selection: Choose woods with a smooth, even surface such as MDF (medium-density fiberboard) or plywood. Rough or porous woods can absorb too much ink, causing uneven prints.
Sealants and Primers: Applying a clear sealant or primer can help create an even surface and improve ink adhesion.
Post-Processing: Consider adding a protective coat after printing to enhance durability and resistance to scratching or fading.
Metal
Surface Preparation: Metals can be highly reflective and require thorough cleaning to remove oils and oxides. Sandblasting or chemical etching can enhance ink adhesion.
Thermal Management: Metal conducts heat efficiently, which can impact ink curing. Monitor and adjust the UV light intensity and curing time to ensure proper ink cure without overheating the material.
Coatings: Use UV-resistant coatings to protect prints from fading due to exposure to sunlight.
Glass
Cleanliness: Glass must be impeccably clean. Use glass cleaner designed for optical surfaces and lint-free cloths.
Positioning: Small imperfections in glass can be exaggerated by printing. Inspect the glass carefully before printing and position prints to minimize the visibility of any imperfections.
Curing: Glass reflects UV light, which can affect curing uniformity. Use a curing system designed for transparent materials or adjust the angle of UV exposure to ensure even curing.
Plastics
Material Compatibility: Not all plastics are compatible with UV inks. Test your material for compatibility, paying attention to any potential for distortion or surface degradation.
Temperature Control: Plastics can warp or melt if exposed to excessive heat. Maintain a controlled environment and monitor the printing temperature closely.
Flexibility: When printing on flexible plastics, use a tensioning system to keep the material taut during printing to avoid distortion.
Textiles
Pretreatment: Textiles often require a pretreatment to enhance ink absorption and adhesion. This could involve steaming, coating, or using a specialized inkjet textile pretreatment.
Media Support: Use a mesh or mesh-like support under the textile to prevent sagging and ensure even ink distribution.
Curing and Washing: Ensure complete ink curing to prevent ink transfer during washing. Follow the printer manufacturer’s guidelines for post-curing and washing instructions.
Ceramics and Tiles
Glaze Compatibility: UV inks may not adhere well to glazed surfaces. Test on unglazed or specially prepared glazed tiles.
Firing: While UV printing eliminates the need for high-temperature firing, some ceramic applications may still require post-firing for additional durability.
Grout Lines: When printing on tiles intended for installation, consider the impact of grout lines on the overall design. Use grout-resistant inks or design around potential grout placement.
Paper and Cardboard
Weight and Thickness: Thicker papers and cardboards can handle higher ink loads and provide better definition. Choose materials appropriate for the desired print quality.
Absorbency: Paper’s absorbency affects ink penetration and drying. Test different papers to find the one that best balances ink absorption and surface finish.
Curl and Cockle: UV curing can cause paper to curl or cockle. Use anti-curl sprays or adjust the printing and curing parameters to minimize this effect.
Advanced Techniques for Enhanced Print Quality
Profiling and Calibration:
Regular profiling and calibration of your UV flatbed printer ensure consistent color accuracy and print quality across different materials. Utilize color management software to create profiles tailored to each material type.
Layering and Ink Opacity:
Adjust the ink layering and opacity settings based on the material’s porosity and desired print effect. Porous materials may require more ink layers to achieve opacity, while non-porous surfaces may benefit from lighter ink applications to prevent ink pooling.
White Ink Usage:
When printing on dark or transparent materials, white ink can be used as a base layer to improve color vibrancy and opacity. Ensure precise control over white ink application to avoid over-saturation or ink build-up.
Software Optimization:
Utilize advanced printing software features such as rip (raster image processor) settings, halftone patterns, and color separation techniques to optimize print quality for specific materials.
UV flatbed printers offer a wealth of opportunities for creative expression and industrial applications, but achieving optimal print results on diverse materials requires careful preparation, understanding of material characteristics, and strategic use of printer capabilities. By following the tips outlined in this article—from meticulous material preparation to advanced printing techniques—you can unlock the full potential of UV flatbed printing, delivering high-quality, durable prints across a wide range of substrates. Remember, continuous experimentation and refinement are key to mastering the art and science of UV flatbed printing. Happy printing!