UV Flatbed Printer: Tips for Printing on Transparent Materials
UV Flatbed Printer: Tips for Printing on Transparent Materials
The UV flatbed printer has revolutionized the printing industry, offering unparalleled versatility and precision in reproducing intricate designs on a wide range of surfaces. Among its many capabilities, printing on transparent materials presents a unique set of challenges and opportunities. Transparent substrates, such as glass, acrylic, and certain types of plastics, can yield stunning visual effects when printed with UV ink, but achieving optimal results requires careful consideration of several factors. In this article, we will explore essential tips and techniques for successfully printing on transparent materials using a UV flatbed printer.
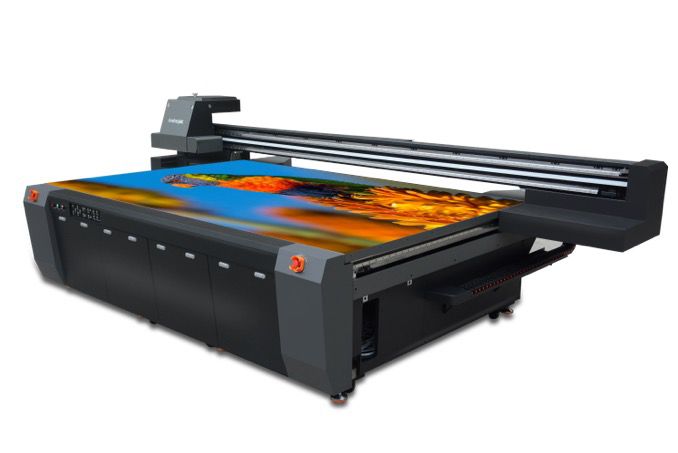
1. Understand the Material Properties
Transparent materials vary greatly in their chemical composition, surface texture, and reactivity to UV inks. Before embarking on a print job, it is crucial to thoroughly understand the properties of the material you are working with. For instance, some transparent plastics may warp or discolor under the heat generated by UV curing, while others might have a natural tendency to repel ink, leading to poor adhesion.
Research the Material: Consult the material manufacturer’s guidelines for compatibility with UV printing and any specific pretreatment requirements.
Test Prints: Conduct small-scale test prints to assess ink adhesion, color accuracy, and overall print quality. This step also helps in identifying potential issues such as ink bleeding or smearing.
2. Surface Preparation
Proper surface preparation is vital for ensuring that UV inks adhere correctly to transparent materials. Transparent surfaces can be particularly challenging due to their lack of absorbency.
Cleaning: Thoroughly clean the surface to remove any dust, dirt, or oils that could interfere with ink adhesion. Use a lint-free cloth and a suitable cleaning agent recommended for the material.
Priming: Apply a primer or adhesion promoter specifically designed for UV printing on transparent surfaces. This step enhances ink adhesion and can prevent issues like ink cracking or peeling over time.
Handling Static: Transparent materials, especially plastics, can generate static electricity, which can attract dust and cause ink misplacement. Use anti-static sprays or devices to mitigate this issue.
3. Ink Selection and Color Management
Choosing the right ink and managing colors effectively are crucial for achieving vibrant, long-lasting prints on transparent materials.
UV Ink Quality: Opt for high-quality UV inks formulated for transparency printing. These inks should offer excellent durability, resistance to fading, and good adhesion properties.
Color Calibration: Calibrate your printer and monitor to ensure accurate color reproduction. Transparent materials can sometimes alter the appearance of colors, so it’s essential to achieve color consistency from design to print.
White Base Layer: Consider printing a white base layer before applying colored inks. This step enhances color saturation and vibrancy, especially on clear substrates, and can help prevent colors from appearing washed out.
4. Print Settings and Curing
Adjusting your printer’s settings and curing process is critical for achieving optimal results on transparent materials.
Ink Drop Size: Use smaller ink drop sizes for finer detail and better ink control. This setting helps prevent ink from spreading or bleeding, which can be a problem on smooth, non-absorbent surfaces.
Curing Temperature and Time: The UV curing process solidifies the ink, and the temperature and duration of curing can significantly affect the print quality. Follow the ink manufacturer’s recommendations for curing parameters, as over-curing can cause material warping or ink discoloration, while under-curing may result in poor adhesion.
Multi-Pass Printing: For better ink coverage and adhesion, consider using multi-pass printing techniques. This involves printing the same layer multiple times to build up ink density gradually.
5. Design Considerations
Designing for transparent materials requires a different approach compared to traditional substrates. The transparency of the material can be leveraged to create unique visual effects.
Reverse Printing: When printing on the back of transparent materials, remember that the image will be reversed. This technique is often used for backlit applications, where the light source illuminates the print from behind, creating a striking effect.
Layering and Depth: Use layering techniques in your design to create a sense of depth and dimension. Transparent materials can enhance this effect, making the print appear more three-dimensional.
Transparency as an Asset: Embrace the transparency of the material as a design element. Incorporate areas of the design that intentionally leave the material clear to play with light and shadow.
6. Post-Processing and Finishing
After printing, the post-processing and finishing stages can further enhance the appearance and durability of your prints on transparent materials.
Cutting and Trimming: Use precision cutting tools to achieve clean edges, especially if the printed material will be used in applications where neatness is crucial, such as signage or display cases.
Lamination: Consider applying a protective laminate to the printed surface to increase durability and scratch resistance. This is particularly useful for outdoor applications or high-traffic areas.
Mounting and Display: Depending on the application, you may need to mount the transparent material onto a backing or frame. Ensure that the mounting method does not compromise the integrity of the print or the material.
7. Quality Control and Maintenance
Maintaining consistent print quality on transparent materials requires regular quality control checks and printer maintenance.
Regular Cleaning: Keep your printer clean, especially the print head and ink system, to prevent clogs and ensure smooth ink flow.
Calibration Checks: Perform regular calibration checks to maintain color accuracy and print precision.
Material Handling: Develop standardized procedures for handling transparent materials to minimize the risk of damage during loading, printing, and unloading.
Conclusion
Printing on transparent materials with a UV flatbed printer offers exciting creative possibilities but also presents unique challenges. By understanding the properties of the material, preparing the surface correctly, selecting the right ink, adjusting print settings, considering design elements, and implementing proper post-processing and maintenance, you can achieve outstanding results. With careful planning and attention to detail, UV printing on transparent materials can yield stunning, durable prints that stand out in any application. Whether you’re creating eye-catching signage, intricate product displays, or artistic installations, mastering these techniques will elevate your UV printing capabilities to new heights.