UV Flatbed Printer: Tips for Printing on Uneven Surfaces
UV Flatbed Printer: Tips for Printing on Uneven Surfaces
In the realm of digital printing, UV flatbed printers have revolutionized the way we approach surface decoration and customization. These versatile machines can print on a wide array of materials, including rigid substrates like wood, metal, glass, and even uneven surfaces. While UV flatbed printers excel at producing high-quality prints on flat, smooth surfaces, tackling uneven or irregular surfaces presents a unique set of challenges. This article aims to provide comprehensive tips and strategies for achieving optimal print results when using a UV flatbed printer on uneven surfaces.
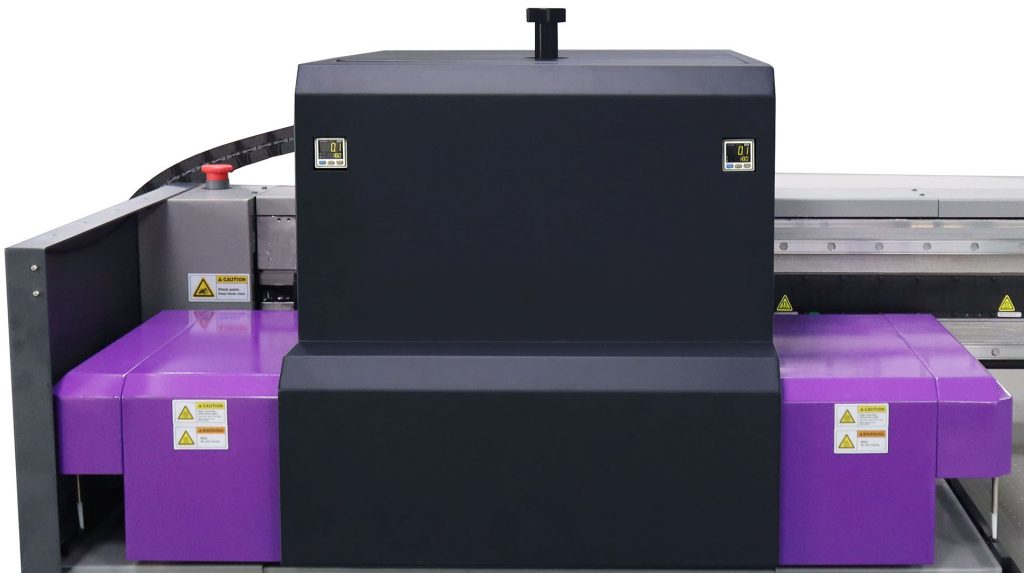
Understanding the Challenges
Before delving into the solutions, it’s crucial to grasp the inherent difficulties associated with printing on uneven surfaces. Uneven surfaces can introduce several issues:
Ink Adhesion: Variations in surface height can affect ink adhesion, leading to uneven coverage or ink pooling in low areas.
Registration Accuracy: Maintaining precise alignment of the print image across an uneven surface can be challenging.
Print Head Clearance: The print heads need to maintain a consistent distance from the surface to ensure proper ink deposition. Uneven surfaces may require adjustments to avoid contact or excessive distance.
Curing Uniformity: UV light needs to evenly cure the ink across the entire surface. Shadows or variations in distance from the UV lamps can result in incomplete curing.
Preparing the Surface
Cleaning and Preparation:
Thorough Cleaning: Ensure the surface is clean and free of dust, dirt, oils, and other contaminants. Use appropriate cleaners and allow the surface to dry completely.
Sanding and Leveling: For minor imperfections, light sanding or using a leveling compound can help create a more uniform surface. This step is particularly important for wood or textured materials.
Priming:
Primer Application: Apply a suitable primer to enhance ink adhesion. Choose a primer compatible with both the surface material and the UV inks.
Uniform Coating: Ensure the primer is applied evenly, paying extra attention to any recessed areas where ink might pool.
Printer Settings and Adjustments
Height Adjustment:
Manual Calibration: If your printer allows, manually adjust the height of the print heads to maintain an optimal distance from the surface. This may involve using spacers or adjusting the Z-axis.
Automatic Leveling Systems: Some advanced UV flatbed printers come equipped with automatic leveling systems that can adjust the print head height in real-time. Ensure this feature is calibrated correctly.
Print Resolution and Speed:
Lower Resolution: For highly uneven surfaces, consider reducing the print resolution. This can help prevent the print heads from colliding with the surface and ensure smoother ink deposition.
Slower Speed: Printing at a slower speed can improve ink adhesion and allow for better control over the print process.
Ink Coverage and Layering:
Increased Ink Flow: Adjust the ink flow settings to ensure adequate coverage, especially in recessed areas.
Multiple Layers: Consider printing in multiple layers, allowing each layer to cure before applying the next. This can help build up a more uniform print on uneven surfaces.
Software Optimization
Image Preprocessing:
Distortion Correction: Use software tools to pre-distort the image to counteract any surface irregularities. This ensures that the final print appears correct on the uneven surface.
Color Management: Adjust color settings to account for any substrate absorption or reflection characteristics that might affect the final appearance.
Rip Software:
Custom Profiles: Create custom RIP (Raster Image Processor) profiles for different surface types and conditions. This allows for precise control over ink deposition and curing.
Test Prints: Always perform test prints on similar surfaces to fine-tune your RIP settings before full-scale production.
Curing and Post-Processing
UV Curing:
Uniform Exposure: Ensure the UV lamps are properly maintained and aligned to provide consistent curing across the entire print area.
Extended Curing Time: For uneven surfaces, consider increasing the curing time to ensure complete polymerization of the ink.
Post-Processing:
Inspection: Thoroughly inspect the print for any defects or areas of incomplete curing.
Touch-Up: If necessary, use a UV touch-up lamp to cure any missed spots or areas where the ink didn’t fully adhere.
Protection and Finishing:
Clear Coat: Apply a clear protective coat to enhance durability and protect the print from UV degradation, scratches, and chemicals.
Lamination: For added protection and a glossy finish, consider laminating the printed surface.
Special Considerations for Specific Materials
Wood:
Grain and Texture: Wood’s natural grain and texture can affect ink absorption. Test different primer and ink combinations to find the best adhesion.
Moisture Content: Ensure the wood is properly dried to prevent warping and ink bleeding.
Metal:
Surface Treatment: Metals may require pretreatment to improve ink adhesion. This can include sanding, priming, or applying a special coating.
Thermal Expansion: Consider the metal’s thermal properties, as it may expand or contract during the printing and curing process.
Glass:
Cleanliness: Glass surfaces must be meticulously clean to ensure proper ink adhesion.
Curing Temperature: Adjust the curing temperature to prevent thermal stress on the glass, which could lead to cracking.
Textiles and Fabrics:
Stretch and Movement: Textiles can shift or stretch during printing. Use adhesives or tensioning systems to keep the fabric stable.
Ink Penetration: Choose inks specifically designed for textile printing to ensure proper penetration and color fastness.
Best Practices for Maintenance and Troubleshooting
Regular Maintenance:
Clean Print Heads: Regularly clean the print heads to prevent ink buildup and ensure consistent ink flow.
Check UV Lamps: Inspect and replace UV lamps as needed to maintain proper curing intensity.
Troubleshooting:
Ink Pooling: If ink is pooling in low areas, try increasing the print head height, reducing ink flow, or adjusting the print speed.
Image Distortion: If the printed image appears distorted, review and adjust your image preprocessing settings.
Curing Issues: If the ink isn’t curing properly, check the UV lamp alignment, increase curing time, or adjust the curing temperature.
Conclusion
Printing on uneven surfaces with a UV flatbed printer requires careful preparation, precise adjustments, and a thorough understanding of both the printer’s capabilities and the surface’s characteristics. By following the tips outlined in this article, you can overcome the challenges associated with uneven surfaces and achieve high-quality, durable prints. Remember to always perform test prints, regularly maintain your equipment, and be prepared to adjust your settings as needed. With the right approach, UV flatbed printers can unlock a world of creative possibilities for decorating and customizing a wide range of surfaces.