UV Flatbed Printer: Tips for Printing on Wood and Other Porous Materials
UV Flatbed Printer: Tips for Printing on Wood and Other Porous Materials
In the realm of digital printing, UV flatbed printers have revolutionized the way we approach printing on a wide variety of materials. Among the myriad of substrates that these versatile machines can handle, wood and other porous materials present unique challenges and opportunities. The ability to print directly onto wood, for instance, opens up a world of creative possibilities for artisans, decorators, and businesses alike. However, achieving optimal results requires a keen understanding of both the printer’s capabilities and the specific characteristics of the materials being printed on. In this article, we will delve into the intricacies of printing on wood and other porous materials using a UV flatbed printer, offering practical tips and insights to help you master this art.
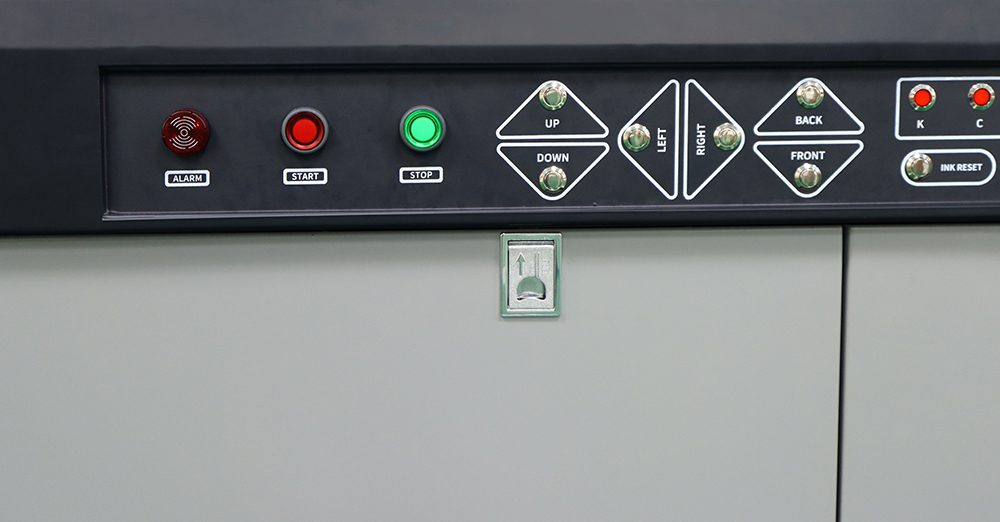
Understanding UV Flatbed Printers
Before we dive into the specifics of printing on wood, it’s essential to have a basic understanding of how UV flatbed printers work. These printers utilize ultraviolet (UV) light to cure the ink as it is applied to the substrate. This process allows for immediate drying, resulting in vibrant, durable prints that are resistant to fading and wear. UV flatbed printers are known for their versatility, capable of printing on materials of varying thicknesses and textures, including rigid substrates like wood, glass, metal, and more.
The Unique Challenges of Printing on Wood
Wood, as a natural material, possesses certain properties that make it both a fascinating and challenging substrate for printing. Its porosity, for example, means that ink absorption can vary greatly depending on the type of wood and its finish. Here are some key challenges you might encounter:
Ink Absorption: Different types of wood absorb ink differently. Softwoods like pine may absorb more ink, leading to darker, more saturated colors, while hardwoods like oak might repel ink, resulting in lighter prints.
Surface Texture: The natural grain and texture of wood can affect how ink adheres to the surface. Rough or uneven surfaces may require preprocessing to ensure even ink distribution.
Moisture Content: Wood’s moisture content can impact print quality. Too much moisture can cause the ink to bleed or spread, while overly dry wood may absorb ink too quickly, leading to patchy results.
Warping and Expansion: Wood is prone to warping and expansion when exposed to changes in temperature and humidity, which can distort prints over time.
Tips for Printing on Wood and Other Porous Materials
To overcome these challenges and achieve stunning prints on wood and similar porous materials, consider the following tips:
1. Choose the Right Wood
Not all woods are created equal when it comes to printing. Opt for woods with a smoother surface and more consistent grain, such as maple or birch plywood. These woods tend to provide better ink adhesion and more predictable results. Avoid highly porous or resinous woods like cedar or pine, which can cause ink to spread unevenly.
2. Prepare the Surface
Proper surface preparation is crucial for achieving high-quality prints. Start by sanding the wood to create a smooth, even surface. This helps to reduce the risk of ink pooling in rough areas and ensures more consistent ink coverage. After sanding, wipe down the surface with a damp cloth to remove any dust or debris. For an even better printing surface, consider applying a thin layer of primer or sealant designed for use with UV inks. This step can help control ink absorption and enhance color saturation.
3. Adjust Printer Settings
UV flatbed printers offer a range of adjustable settings that can be tailored to suit different materials. When printing on wood, you may need to adjust the ink density, print speed, and UV lamp intensity. Experiment with these settings to find the optimal combination for your specific wood type and desired print quality. In general, lower print speeds and higher ink densities can help achieve better ink penetration and color saturation on porous materials.
4. Use the Right Ink
Choosing the correct ink is vital for successful printing on wood. Look for UV-curable inks specifically formulated for use on porous substrates. These inks are designed to penetrate the surface of the wood while maintaining vibrant color and durability. Avoid using inks intended for non-porous materials, as they may not adhere properly and could result in peeling or fading over time.
5. Test Prints
Before committing to a full-scale print job, always perform test prints on scrap pieces of wood. This allows you to assess ink coverage, color accuracy, and overall print quality. Make adjustments to your printer settings and ink choice based on these test results to ensure the final product meets your expectations.
6. Consider Post-Processing
Once the printing is complete, you may want to apply a protective finish to the wood. This can help enhance the durability of the print and protect it from environmental factors like UV rays and moisture. Clear varnishes or polyurethanes are popular choices for this purpose. Be sure to choose a product that is compatible with UV-cured inks and follow the manufacturer’s instructions for application.
7. Maintain Your Printer
Regular maintenance of your UV flatbed printer is essential for achieving consistent, high-quality prints. This includes cleaning the print heads, checking for ink clogs, and ensuring that the UV lamps are functioning correctly. A well-maintained printer will not only produce better results but also extend the life of your equipment.
Expanding to Other Porous Materials
While wood is a popular choice for UV flatbed printing, many other porous materials can also be printed on with similar techniques. These include:
Cardboard and Paperboard: These materials are highly absorbent and require similar surface preparation and ink choices as wood.
Textiles: Natural fabrics like cotton and linen can be printed on using UV flatbed printers, though they may require special pretreatment to ensure ink adhesion.
Leather: Printing on leather presents unique challenges due to its texture and flexibility. However, with the right preparation and ink, stunning results can be achieved.
Stone and Concrete: Although these materials are less porous than wood, they can still be printed on using specialized inks and techniques.
Conclusion
Printing on wood and other porous materials with a UV flatbed printer offers endless creative possibilities. By understanding the unique challenges of these substrates and following the tips outlined above, you can achieve professional-quality prints that showcase the beauty and versatility of UV printing technology. Whether you’re an artist exploring new mediums or a business looking to expand your product offerings, mastering the art of printing on porous materials will open up a world of opportunities for innovation and expression.