UV Flatbed Printer: Tips for Reducing Ink Costs
UV Flatbed Printer: Tips for Reducing Ink Costs
In the realm of digital printing, UV flatbed printers have revolutionized the way we produce high-quality, vibrant prints on various materials. From rigid substrates like glass, metal, and plastic to flexible ones such as fabric and leather, these printers offer unparalleled versatility. However, one of the primary concerns for businesses investing in UV flatbed technology is the cost of ink. Given the specialized nature of UV-curable inks and their role in achieving exceptional print quality, managing ink consumption efficiently becomes crucial. This article delves into practical tips for reducing ink costs while maintaining optimal print quality with a UV flatbed printer.
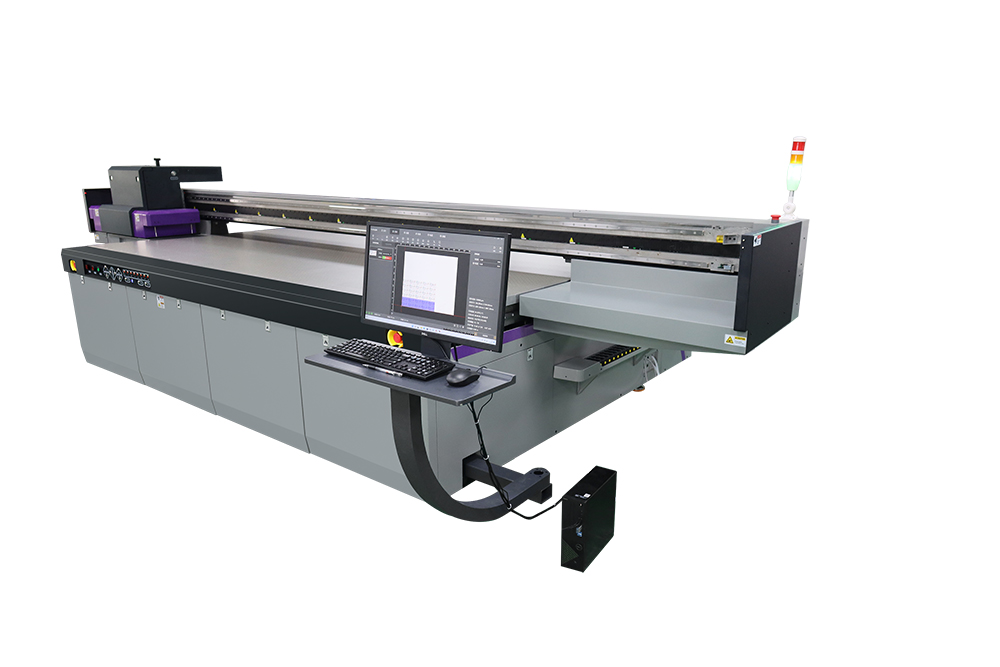
1. Understand Your Ink Consumption
The first step in managing ink costs is to gain a comprehensive understanding of your printer’s ink consumption patterns. Most UV flatbed printers come equipped with software that tracks ink usage per print job. Utilize this feature to monitor ink consumption over time. Analyze which colors are used most frequently and identify any unusual spikes in ink usage that may indicate inefficiencies or misconfigurations.
2. Optimize Print Settings
Fine-tuning your print settings can significantly impact ink consumption. Start by adjusting the ink density or opacity settings. While higher ink densities can enhance color saturation, they also consume more ink. Find the optimal balance between print quality and ink usage by experimenting with different settings. Additionally, consider using variable dot technologies if available, as they can help reduce ink usage while maintaining print quality.
3. Choose the Right Ink Type
Not all UV inks are created equal, and some formulations are more cost-effective than others. Consult with your ink supplier to explore options that offer good print quality at a lower cost per liter. Keep in mind that cheaper inks might compromise print durability or require more frequent printer maintenance, so consider the long-term implications.
4. Implement Ink Saving Modes
Many UV flatbed printers offer ink-saving modes that adjust the ink laydown based on the specific job requirements. For instance, using an ‘economy mode’ can reduce ink consumption for less critical applications without significantly impacting visual quality. Be mindful of when to use these modes to strike a balance between cost savings and print quality.
5. Proper Printer Maintenance
A well-maintained printer operates more efficiently, reducing ink waste. Regularly clean print heads to prevent clogged nozzles that can cause ink to be deposited unevenly or not at all. Also, ensure the printer’s calibration is up to date to avoid misalignments that can lead to ink overuse. Schedule routine maintenance checks with a professional to keep your printer in optimal condition.
6. Careful Material Selection
The type of material you print on can influence ink consumption. Some materials require more ink to achieve the desired color intensity or adhesion. Test different substrates to see how they interact with ink and choose materials that offer good print results with minimal ink usage. Additionally, consider pre-treating materials to enhance ink adhesion, potentially reducing the amount of ink needed for a satisfactory print.
7. Efficient Job Planning
Efficient job planning can minimize ink waste. Arrange print jobs in a way that minimizes printer startups and shutdowns, as each restart can consume additional ink for print head cleaning and priming. Also, group similar jobs together to optimize ink usage, especially if they require similar color profiles.
8. Use Print Profiling Software
Invest in print profiling software that allows you to create custom ICC profiles for specific substrates and ink combinations. This ensures that your printer uses the right amount of ink for each job, reducing over-saturation and ink waste. Custom profiles also help maintain color consistency across different print runs.
9. Train Your Operators
Operator error can contribute to unnecessary ink waste. Train your staff on best practices for ink management, including proper printer operation, job setup, and material handling. Encourage them to report any unusual ink consumption patterns or print quality issues immediately.
10. Explore Ink Recycling Options
Some ink manufacturers offer ink recycling programs where you can return used ink containers for a discount on new ink purchases. This not only reduces waste but also offers a cost-saving opportunity. Inquire about such programs with your ink supplier.
Conclusion
Managing ink costs is a vital aspect of operating a UV flatbed printer profitably. By understanding your printer’s ink consumption patterns, optimizing print settings, choosing the right ink type, implementing ink-saving modes, maintaining your printer properly, selecting materials wisely, planning jobs efficiently, using print profiling software, training your operators, and exploring ink recycling options, you can significantly reduce ink expenses without compromising print quality. Remember, a holistic approach that combines technological advancements with operational best practices is key to achieving long-term cost savings in UV flatbed printing.