UV Flatbed Printer: Tips for Reducing Print Defects and Artifacts
UV Flatbed Printer: Tips for Reducing Print Defects and Artifacts
In the realm of digital printing, UV flatbed printers have emerged as versatile and powerful tools, capable of producing high-quality prints on a wide range of substrates. These printers utilize ultraviolet (UV) light to cure ink instantly, enabling rapid and precise printing on materials such as glass, metal, plastic, wood, and even textiles. However, like any sophisticated machinery, UV flatbed printers are not immune to print defects and artifacts. These imperfections can range from minor ink bleeding and banding to more severe issues like color inconsistency and image distortion. To ensure optimal print quality and minimize these issues, it is crucial to adopt a comprehensive set of practices. This article presents a detailed guide on tips for reducing print defects and artifacts in UV flatbed printing.
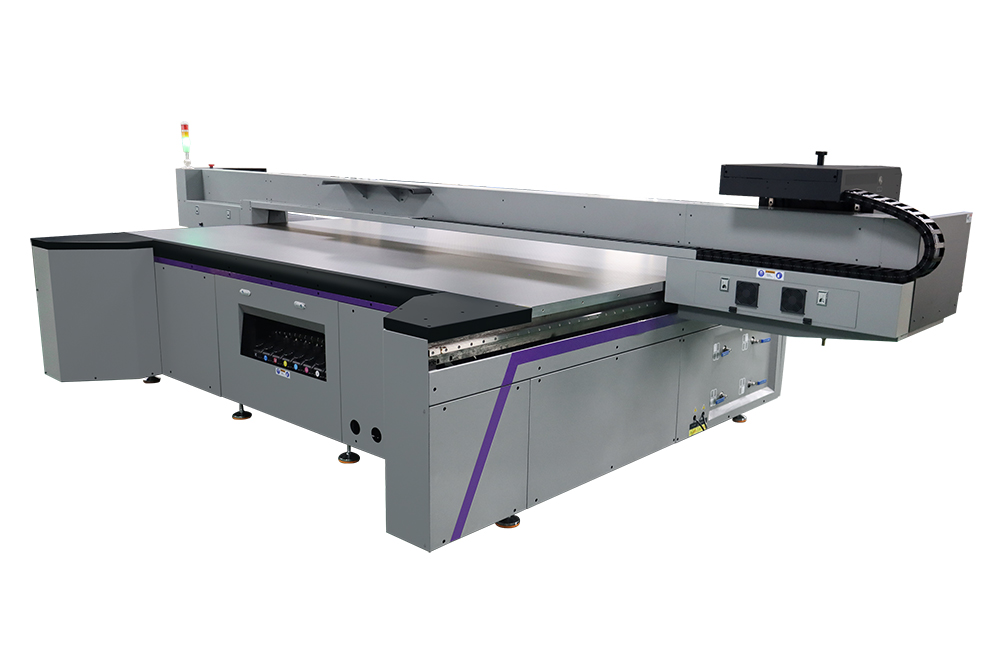
1. Pre-Printing Preparation: The Foundation of Quality
1.1. Substrate Selection and Preparation
The choice of substrate plays a critical role in determining print quality. Different materials have varying levels of absorbency, texture, and reactivity to UV inks. Always conduct test prints on the actual substrate to be used, as even slight variations in material composition can affect ink adhesion and curing.
Cleaning and Pretreatment: Ensure the substrate is clean, dust-free, and, if necessary, pretreated. Contaminants like oils, dust, and moisture can interfere with ink adhesion, leading to defects such as poor ink coverage or bubbling.
Temperature and Humidity Control: Maintain a stable environment with controlled temperature and humidity levels. Variations in these conditions can cause ink to spread unevenly or cure improperly.
1.2. File Preparation and Ripping
Accurate file preparation is essential for achieving the desired print outcome. High-resolution images and proper color management are key.
Resolution: Use images with a resolution of at least 300 dpi to ensure sharpness and clarity. Lower resolutions can result in pixelation and blurred prints.
Color Profile: Utilize the correct color profile for your printer and substrate. Mismatched profiles can lead to color shifts and inaccuracies.
Ripping Software: Employ reliable RIP (Raster Image Processor) software to manage color, resolution, and other print settings effectively. Ensure the RIP software is updated and compatible with your printer’s specifications.
2. Printer Calibration and Maintenance
2.1. Regular Calibration
Regular calibration of the printer ensures that colors are accurate and consistent across prints.
Color Calibration: Perform color calibration using a calibrated color chart and software. This process helps to align the printer’s output with the desired color standards.
Print Head Alignment: Check and adjust the alignment of print heads regularly. Misalignment can cause banding, streaking, and other artifacts.
2.2. Routine Maintenance
Proper maintenance is crucial for preventing print defects and extending the printer’s lifespan.
Cleaning: Regularly clean the print heads, platen, and other critical components to remove ink residue and dust.
Ink Management: Use genuine inks recommended by the printer manufacturer and replace ink cartridges when they reach their expiration date or show signs of degradation.
Nozzle Checks: Perform regular nozzle checks and cleanings to prevent clogged nozzles, which can cause missing dots and lines in the print.
3. Optimizing Print Settings
3.1. Ink Coverage and Layering
Controlling ink coverage and layering is vital for achieving a smooth and uniform print.
Ink Density: Adjust ink density settings based on the substrate and desired effect. Excessive ink can lead to bleeding and smearing, while too little can result in patchy coverage.
Layering Technique: Use multi-pass printing to build up ink layers gradually. This approach minimizes the risk of ink pooling and ensures better adhesion.
3.2. Curing Settings
Proper curing is critical for ink durability and adhesion.
UV Intensity: Adjust the UV lamp intensity according to the ink type and substrate. Insufficient curing can cause ink to remain tacky, while excessive curing can lead to over-hardening and cracking.
Curing Time: Ensure adequate curing time for each layer of ink. Rushing the process can result in under-cured ink, which is prone to smearing and peeling.
4. Environmental Control
4.1. Temperature and Humidity
Maintaining a stable and controlled environment is crucial for consistent print quality.
Temperature Regulation: Keep the printing area within the recommended temperature range. High temperatures can cause ink to spread excessively, while low temperatures can affect ink viscosity and curing.
Humidity Control: Humidity levels should be kept low to prevent moisture from interfering with ink adhesion and curing. Use dehumidifiers and air conditioning systems as needed.
4.2. Dust and Contaminant Management
Dust and other contaminants can significantly impact print quality.
Clean Workspace: Regularly clean the printing area and surrounding environment to minimize dust accumulation.
Air Filtration: Use air filtration systems to remove airborne particles that can settle on the substrate or printer components.
5. Post-Printing Inspection and Quality Control
5.1. Immediate Inspection
Inspect prints immediately after they come out of the printer for any visible defects.
Visual Check: Conduct a thorough visual inspection under controlled lighting conditions to identify issues such as banding, streaking, and color inconsistencies.
Dimensional Accuracy: Use measuring tools to ensure that prints meet the required dimensions and specifications.
5.2. Cure Verification
Verify the cure quality to ensure ink durability and adhesion.
Cure Test: Perform cure tests using a cure verifier or by applying adhesive tape to the print and checking for ink lifting.
Durability Testing: Conduct durability tests, such as scratch and abrasion tests, to ensure the print can withstand expected use and handling.
6. Continuous Improvement and Training
6.1. Operator Training
Well-trained operators are essential for maintaining print quality and reducing defects.
Regular Training: Provide ongoing training for operators on printer operation, maintenance, and troubleshooting.
Best Practices: Encourage the adoption of best practices and standard operating procedures (SOPs) to minimize human error.
6.2. Feedback Loop
Establish a feedback loop to continuously improve print quality.
Customer Feedback: Collect and analyze customer feedback to identify areas for improvement.
Internal Audits: Conduct regular internal audits and quality checks to ensure consistent adherence to quality standards.
Continuous Learning: Stay updated with the latest advancements in UV flatbed printing technology and ink formulations. Attend industry conferences, workshops, and online training sessions to enhance your knowledge and skills.
Conclusion
Achieving high-quality prints with UV flatbed printers requires a meticulous approach that encompasses every aspect of the printing process. From substrate selection and file preparation to printer calibration, maintenance, and environmental control, each step plays a critical role in minimizing print defects and artifacts. By adopting the tips outlined in this article, printer operators can significantly improve print quality, enhance customer satisfaction, and maximize the efficiency and lifespan of their UV flatbed printers. Remember, continuous learning and improvement are key to staying ahead in the ever-evolving world of digital printing.