UV Flatbed Printer Troubleshooting Guide: Common Problems and Solutions
UV Flatbed Printer Troubleshooting Guide: Common Problems and Solutions
Introduction
UV flatbed printers have revolutionized the printing industry by offering versatile, high-quality prints on a wide range of materials. These printers utilize ultraviolet (UV) light to cure inks instantly, resulting in durable and vibrant images. However, like any sophisticated machinery, UV flatbed printers can encounter various issues that may disrupt the printing process. This troubleshooting guide aims to address common problems encountered with UV flatbed printers and provide practical solutions to help operators resolve them efficiently.
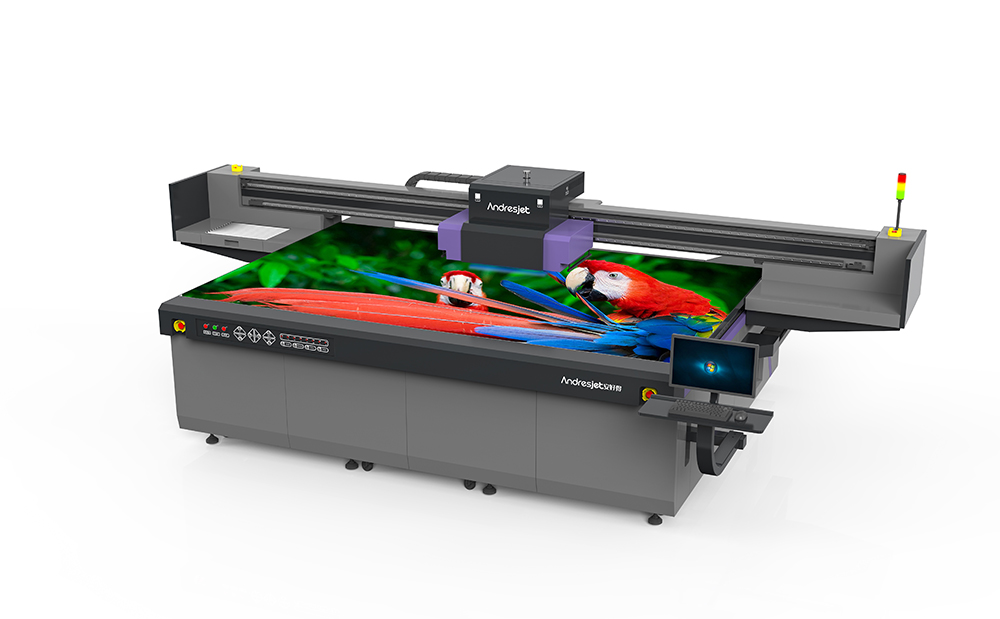
Print Quality Issues
1.1 Poor Image Clarity
Problem: The printed image appears blurry or lacks sharpness.
Possible Causes:
Low resolution of the image file.
Incorrect print settings, such as low dpi (dots per inch).
Misalignment or dirt on the printhead.
Worn-out or damaged printhead.
Solutions:
Ensure the image file has a high resolution, ideally 300 dpi or higher.
Check and adjust the print settings to match the desired output quality.
Clean the printhead regularly using the manufacturer’s recommended cleaning solution and procedures.
If cleaning does not improve the print quality, consider replacing the printhead.
1.2 Color Inconsistency
Problem: The colors in the print do not match the colors on the screen or previous prints.
Possible Causes:
Incorrect color profile settings.
Ink level imbalances.
Aging or faulty ink cartridges.
Variations in ambient temperature or humidity.
Solutions:
Calibrate the printer and monitor to ensure they are using the same color profile, such as Adobe RGB or sRGB.
Check ink levels and replace any low or empty cartridges promptly.
Use high-quality, genuine ink cartridges from the manufacturer to avoid color variation issues.
Maintain a consistent and controlled environment with stable temperature and humidity levels.
1.3 Banding or Striping
Problem: Horizontal or vertical lines appear in the print.
Possible Causes:
Printhead misalignment.
Inconsistent ink flow.
Mechanical issues with the printer’s movement system.
Solutions:
Perform a printhead alignment using the printer’s built-in tools or software.
Check for and clear any ink flow obstructions, such as clogged nozzles.
Inspect the printer’s movement system for any signs of wear or damage and replace worn parts as needed.
Hardware and Mechanical Problems
2.1 Printhead Clogging
Problem: The printhead becomes clogged, resulting in missing or faded prints.
Possible Causes:
Ink drying on the printhead.
Dust or debris accumulation.
Infrequent use or improper storage.
Solutions:
Run a printhead cleaning cycle regularly, as recommended by the manufacturer.
Use a printhead cleaning solution and lint-free cloth to manually clean the printhead if necessary.
Store the printer in a clean, dust-free environment and run maintenance cycles periodically when not in use.
2.2 Paper Feed Issues
Problem: The printer fails to feed paper or media correctly.
Possible Causes:
Misaligned or damaged media guides.
Slippery or incompatible media.
Dirty or worn-out rollers.
Solutions:
Adjust the media guides to ensure proper alignment with the media edges.
Use media that is compatible with the printer and has the appropriate surface texture.
Clean the rollers with a damp cloth and mild cleaner, and replace worn-out rollers.
2.3 UV Lamp Failure
Problem: The UV lamp does not turn on or fails to cure the ink properly.
Possible Causes:
Lamp burnout due to extensive use or aging.
Power supply issues.
Faulty lamp connections or wiring.
Solutions:
Replace the UV lamp according to the manufacturer’s recommended maintenance schedule.
Check the power supply and connections to ensure they are functioning correctly.
Contact a technician to inspect and repair any faulty wiring or connections.
Software and Connectivity Issues
3.1 Print Job Failures
Problem: Print jobs fail to start or stop unexpectedly.
Possible Causes:
Corrupted print files.
Incompatible or outdated printer drivers.
Insufficient computer resources (e.g., memory, processing power).
Solutions:
Ensure the print files are not corrupted and are in a compatible format.
Update the printer drivers to the latest version available from the manufacturer.
Close unnecessary applications and free up system resources to improve performance.
3.2 Connectivity Problems
Problem: The printer fails to connect to the computer or network.
Possible Causes:
Faulty USB, Ethernet, or Wi-Fi connections.
Incorrect network settings or configurations.
Firewall or security software blocking the connection.
Solutions:
Check the physical connections (cables, ports) for any signs of damage or wear and replace as needed.
Verify network settings and configurations, ensuring they match the printer’s requirements.
Configure firewall and security settings to allow communication between the computer and the printer.
3.3 RIP Software Issues
Problem: The Raster Image Processor (RIP) software malfunctions or crashes.
Possible Causes:
Incompatible or corrupted software.
Insufficient system resources.
Conflicts with other software or drivers.
Solutions:
Ensure the RIP software is compatible with the printer and operating system.
Update the RIP software to the latest version and apply any necessary patches.
Close unnecessary applications and free up system resources to improve performance.
Uninstall and reinstall the RIP software if necessary, following the manufacturer’s instructions.
Maintenance and Preventive Measures
4.1 Regular Cleaning and Maintenance
Importance: Regular cleaning and maintenance are crucial for maintaining optimal printer performance and preventing issues.
Recommendations:
Clean the printhead, rollers, and other critical components regularly.
Replace worn-out parts, such as ink cartridges, UV lamps, and rollers, according to the manufacturer’s schedule.
Run printer maintenance cycles, such as printhead alignment and nozzle checks, as recommended.
4.2 Environmental Control
Importance: Maintaining a controlled environment can help prevent issues related to temperature, humidity, and dust.
Recommendations:
Keep the printer in a clean, dust-free environment with stable temperature and humidity levels.
Use an air purification system or air filters to minimize dust accumulation.
Avoid placing the printer in direct sunlight or areas with extreme temperature fluctuations.
4.3 Operator Training
Importance: Proper operator training can help prevent user-induced issues and ensure efficient problem-solving when issues arise.
Recommendations:
Provide comprehensive training on printer operation, maintenance, and troubleshooting.
Encourage operators to follow manufacturer guidelines and best practices.
Offer ongoing support and resources, such as user manuals and online tutorials.
Conclusion
UV flatbed printers offer numerous advantages for a wide range of printing applications. However, like any complex machinery, they can encounter various issues that may affect print quality, hardware performance, and software functionality. By understanding the common problems and their solutions, operators can efficiently troubleshoot and resolve issues, ensuring optimal printer performance and high-quality prints. Regular maintenance, environmental control, and operator training are essential for preventing issues and maximizing the printer’s lifespan. With this troubleshooting guide, operators can confidently address and resolve common UV flatbed printer problems, enabling them to produce exceptional prints consistently.