UV Flatbed Printer: Troubleshooting Guide for Beginners
UV Flatbed Printer: Troubleshooting Guide for Beginners
UV flatbed printers have revolutionized the printing industry by offering versatile, high-quality prints on a wide range of materials. Whether you’re a seasoned professional or a beginner in the field, encountering issues with your UV flatbed printer can be frustrating. This comprehensive troubleshooting guide aims to equip beginners with the knowledge to diagnose and resolve common problems effectively, ensuring smooth and efficient printing operations.
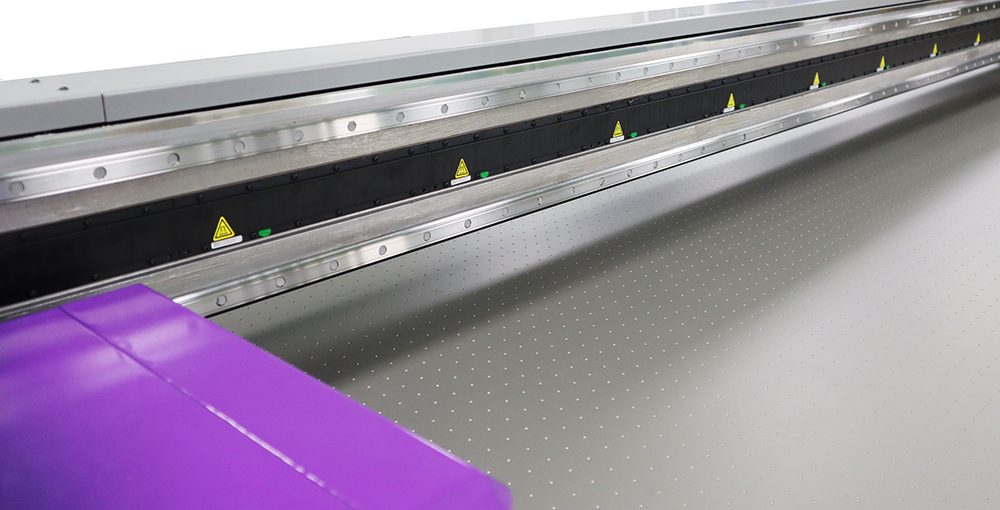
Understanding the Basics of UV Flatbed Printers
Before diving into troubleshooting, it’s essential to have a basic understanding of how UV flatbed printers work. These printers utilize ultraviolet (UV) light to cure or dry the ink immediately after it’s applied to the substrate. This process allows for printing on various materials such as plastic, glass, metal, wood, and more. The key components of a UV flatbed printer include the print head, UV lamps, ink supply system, and control software.
Common Issues and Troubleshooting Steps
1. Print Quality Problems
Issue: Blurry or Fuzzy Prints
Possible Cause: Low resolution settings in the printer software.
Solution: Check the print settings and ensure the resolution is set to the highest possible value for your printer model.
Issue: Banding or Lines in the Print
Possible Cause: The print head may be clogged or misaligned.
Solution: Perform a print head cleaning cycle and check for any obstructions. If the issue persists, consider recalibrating the print head.
Issue: Ink Smearing
Possible Cause: The substrate might be moving during the printing process.
Solution: Ensure the substrate is securely fastened to the print bed. Adjust the printer’s settings to reduce the print speed slightly, allowing the ink to set properly before the next pass.
2. Ink-Related Issues
Issue: Ink Not Adhering to the Substrate
Possible Cause: The substrate may not be compatible with the type of ink being used.
Solution: Check the printer’s manual for recommended substrates and inks. You may need to use a primer or change the ink type.
Issue: Ink Leakage
Possible Cause: A damaged ink cartridge or tubing.
Solution: Inspect the ink supply system for any visible leaks. Replace any damaged components and ensure all connections are secure.
Issue: Ink Clogging in the Print Head
Possible Cause: The printer has been idle for a long period.
Solution: Run a print head cleaning cycle regularly, especially if the printer is not used frequently. Consider using a maintenance kit to keep the print head in optimal condition.
3. UV Lamp Issues
Issue: Prints Not Fully Curing
Possible Cause: The UV lamps might be weak or malfunctioning.
Solution: Check the UV lamp intensity and replace any bulbs that are not functioning correctly. Ensure the lamps are clean and free of debris.
Issue: Uneven Curing
Possible Cause: The UV lamps may be positioned incorrectly or the substrate is not flat.
Solution: Adjust the lamp positioning to ensure even coverage. Ensure the substrate is level and properly supported on the print bed.
4. Software and Connectivity Problems
Issue: Printer Not Responding to Commands
Possible Cause: Connectivity issues between the printer and the computer.
Solution: Check the USB or network connection. Restart both the printer and the computer, and ensure the correct drivers are installed.
Issue: Print Jobs Stuck in Queue
Possible Cause: Software conflict or corrupted print job.
Solution: Clear the print queue and resend the job. Update the printer’s firmware and software to the latest version.
Issue: Incorrect Colors in the Print
Possible Cause: Color profile mismatch or incorrect printer settings.
Solution: Calibrate the printer and ensure the correct color profile is selected in the print settings. Use a color calibration tool if available.
5. Mechanical Issues
Issue: Printer Making Unusual Noises
Possible Cause: Mechanical parts may be worn or misaligned.
Solution: Inspect the printer for any loose or worn parts.Lubricate moving components as recommended by the manufacturer.
Issue: Print Head Hitting the Substrate
Possible Cause: Incorrect Z-axis adjustment.
Solution: Adjust the Z-axis to ensure the print head has the correct clearance above the substrate. Refer to the printer’s manual for specific instructions.
Issue: Substrate Not Feeding Properly
Possible Cause: Issues with the substrate loading mechanism.
Solution: Check for any obstructions in the feed path. Ensure the substrate is the correct size and thickness for the printer.
Preventive Maintenance Tips
To minimize issues and ensure the longevity of your UV flatbed printer, follow these preventive maintenance tips:
Regular Cleaning: Keep the print head, UV lamps, and other components clean to prevent dust and debris accumulation.
Ink Management: Use high-quality ink and replace cartridges before they run out completely to avoid clogging.
Calibration: Regularly calibrate the printer to maintain print quality and accuracy.
Software Updates: Keep the printer’s firmware and software up to date to benefit from the latest features and bug fixes.
Humidity and Temperature Control: Maintain optimal humidity and temperature levels in the printing environment to avoid ink-related issues.
Training: Ensure operators are trained properly on the use and maintenance of the printer to prevent user errors.
Conclusion
Troubleshooting a UV flatbed printer can seem daunting at first, but with a systematic approach and a basic understanding of the printer’s components, most issues can be resolved efficiently. Remember to start with the simplest solutions and gradually move to more complex troubleshooting steps. Regular maintenance and proper handling can significantly reduce the occurrence of problems, ensuring your UV flatbed printer operates smoothly and produces high-quality prints consistently. By following the guidelines outlined in this troubleshooting guide, beginners can gain confidence in managing their printers and tackle issues with ease.