UV Flatbed Printer: Troubleshooting Guide for Common Problems
UV Flatbed Printer: Troubleshooting Guide for Common Problems
UV flatbed printers have revolutionized the printing industry by offering versatile and high-quality printing on a wide range of materials. These printers use ultraviolet light to cure the ink instantly, resulting in durable and vibrant prints. However, like any other piece of technology, UV flatbed printers can encounter various issues that may disrupt the printing process. This troubleshooting guide aims to address some of the most common problems you might face with your UV flatbed printer and provide practical solutions to resolve them.
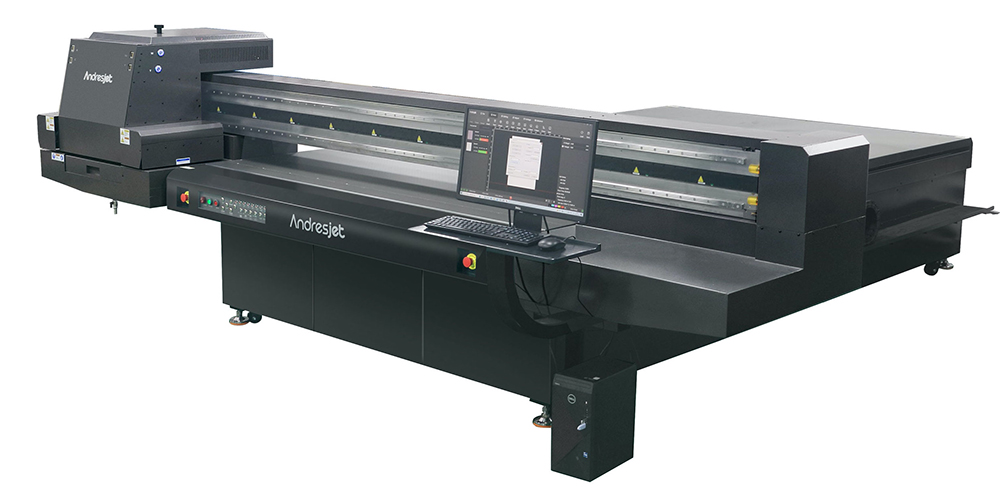
1. Print Quality Issues
Problem: Fuzzy or Blurred Prints
Possible Cause: Low resolution settings in the printer driver or design software.
Solution: Ensure that the resolution is set to the highest possible setting, typically 300 dpi or higher, depending on your printer’s capabilities.
Possible Cause: Nozzle clogging or misalignment.
Solution: Perform a nozzle clean and alignment through the printer’s maintenance menu. Regular cleaning and maintenance can prevent this issue.
Possible Cause: Incorrect media settings.
Solution: Verify that the printer settings match the type and thickness of the media being used. Adjust the media settings accordingly in the printer driver.
Problem: Banding or Stripes in the Print
Possible Cause: Inkjet nozzles are not firing consistently.
Solution: Run a nozzle check and clean the print heads if necessary. If the issue persists, consider replacing the ink cartridges or print heads.
Possible Cause: Inconsistent ink flow.
Solution: Check the ink supply system for any blockages or air bubbles. Ensure that the ink tanks are properly seated and filled.
Possible Cause: Mechanical issues with the printer’s movement.
Solution: Inspect the printer’s belts, pulleys, and motors for any signs of wear or damage. Lubricate moving parts as recommended by the manufacturer.
2. Ink-Related Problems
Problem: Ink Not Adhering to the Media
Possible Cause: Incorrect ink type for the media.
Solution: Use the appropriate type of ink recommended for the specific media you are printing on. Consult your printer’s manual or the ink manufacturer for guidance.
Possible Cause: UV lamp not functioning properly.
Solution: Check the UV lamp for any signs of damage or wear. Replace the lamp if necessary. Ensure that the lamp is turned on and functioning during the printing process.
Possible Cause: Incorrect curing settings.
Solution: Adjust the curing settings, such as the intensity and duration of the UV light, according to the ink and media type.
Problem: Ink Smearing or Bleeding
Possible Cause: Excessive ink application.
Solution: Reduce the ink density settings in the printer driver or design software. Also, ensure that the media is properly absorbed and compatible with the ink.
Possible Cause: Print heads too close to the media.
Solution: Adjust the print head height to ensure proper clearance between the heads and the media. This setting can usually be adjusted in the printer’s maintenance menu.
3. Printer Hardware Issues
Problem: Printer Not Responding
Possible Cause: Power issues.
Solution: Check the power supply and ensure that the printer is properly plugged in. Try turning the printer off and on again.
Possible Cause: Connectivity issues.
Solution: Verify that the printer is properly connected to the computer or network. Check cables, USB connections, and network settings. Restart the printer and the computer if necessary.
Possible Cause: Firmware or software issues.
Solution: Check for firmware updates from the printer manufacturer’s website. Ensure that the printer driver and any associated software are up to date.
Problem: Mechanical Noise or Vibrations
Possible Cause: Loose or worn parts.
Solution: Inspect the printer for any loose screws, belts, or other components. Tighten or replace any worn parts as needed.
Possible Cause: Misalignment of the print carriage or media feed system.
Solution: Calibrate the printer’s print carriage and media feed system through the printer’s maintenance menu. This process ensures that all components are properly aligned.
4. Software and Configuration Issues
Problem: Incorrect Colors in the Print
Possible Cause: Color profile mismatch.
Solution: Ensure that the color profile in your design software matches the printer’s color capabilities. Use ICC profiles provided by the printer manufacturer for accurate color matching.
Possible Cause: Monitor calibration.
Solution: Calibrate your computer monitor to ensure that the colors displayed on the screen match the printed output. This can be done using monitor calibration tools.
Problem: Print Jobs Stalling or Freezing
Possible Cause: Printer driver issues.
Solution: Update the printer driver to the latest version. If the issue persists, try reinstalling the driver.
Possible Cause: Computer performance issues.
Solution: Ensure that your computer meets the minimum system requirements for running the printer software. Close any unnecessary applications to free up system resources.
Possible Cause: Corrupt print file.
Solution: Try printing a different file to determine if the issue is with the specific file or the printer. If the problem persists, the file may be corrupt. Re-create or re-save the file in a different format.
5. Media Handling Problems
Problem: Media Not Feeding Properly
Possible Cause: Incorrect media settings.
Solution: Adjust the media settings in the printer driver to match the type, thickness, and size of the media being used.
Possible Cause: Dirty or damaged feed rollers.
Solution: Clean the feed rollers with a lint-free cloth and a mild cleaning solution. Replace any damaged rollers.
Possible Cause: Media not loaded properly.
Solution: Ensure that the media is loaded correctly in the printer tray or feeder. Align the edges and make sure the media is not curled or wrinkled.
Problem: Media Jamming
Possible Cause: Overloading the printer tray.
Solution: Do not overload the printer tray. Follow the manufacturer’s guidelines for the maximum number of sheets or thickness of media.
Possible Cause: Incorrect media path.
Solution: Check the media path for any obstructions or misalignments. Ensure that the media guides are properly adjusted to support the media.
Conclusion
Troubleshooting UV flatbed printer issues can be a complex process, but by following the steps outlined in this guide, you can diagnose and resolve many common problems. Regular maintenance, such as cleaning the print heads, inspecting mechanical parts, and updating software, can help prevent issues from arising. If you encounter a problem that you are unable to solve, consult the printer’s manual or contact the manufacturer’s technical support for further assistance. With proper care and maintenance, your UV flatbed printer can continue to produce high-quality prints for years to come.