UV Flatbed Printer: Understanding Dot Gain and Its Effects on Print Quality
In the realm of digital printing, particularly with UV flatbed printers, achieving precise and consistent print quality is paramount. One critical factor that significantly influences the outcome of prints is dot gain. This phenomenon, often overlooked yet fundamentally important, can make or break the visual appeal and accuracy of the printed materials. To truly grasp the nuances of UV flatbed printing and optimize print quality, it’s essential to delve into the concept of dot gain, its causes, measurement techniques, and its overall impact on the final print.
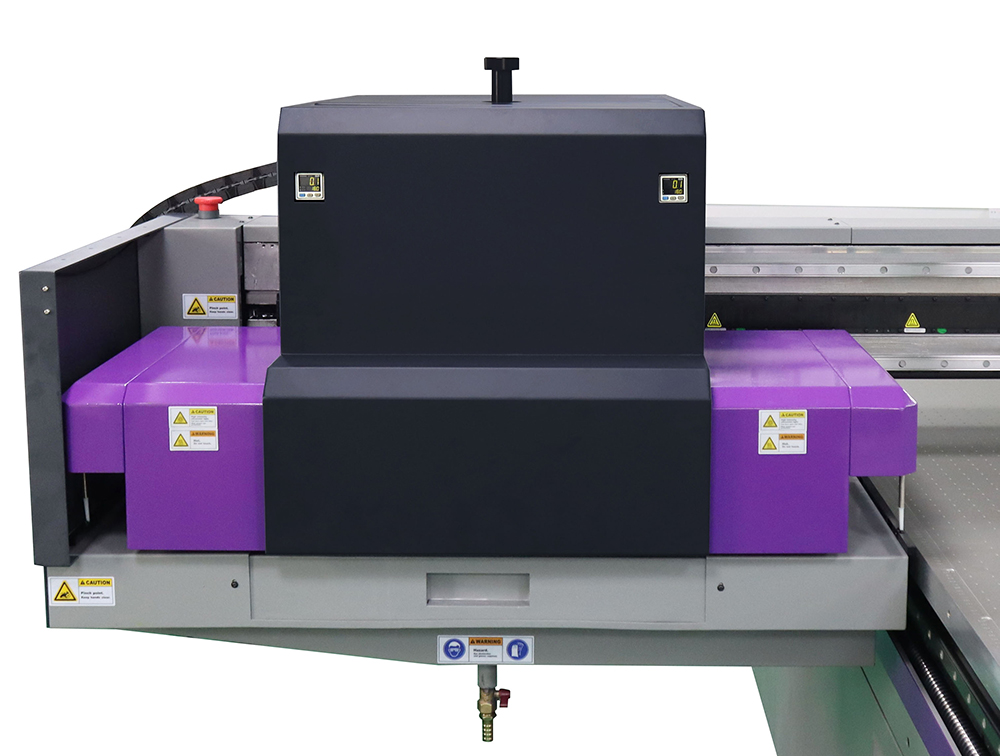
What is Dot Gain?
Dot gain refers to the enlargement of dots during the printing process. In ideal conditions, a digital image is composed of tiny dots of varying sizes and colors that combine to create the desired visual effect. However, when this image is transferred onto a substrate using a UV flatbed printer, these dots can spread or expand beyond their original dimensions. This expansion can occur due to several factors, including ink absorption characteristics of the substrate, ink viscosity, printing pressure, and the interaction between the ink and the substrate’s surface.
Causes of Dot Gain
Dot gain is a multifaceted issue influenced by several variables:
Ink Absorption: Different substrates absorb ink differently. Porous materials like uncoated paper tend to absorb ink more readily, causing dots to spread. Conversely, non-porous surfaces like glossy or coated materials may exhibit less dot gain but can still be affected by ink surface tension and wetting properties.
Ink Viscosity: The thickness or fluidity of the ink plays a crucial role. Inks with lower viscosity tend to spread more easily, contributing to increased dot gain. Conversely, higher viscosity inks are less prone to spreading but may require more pressure to be applied, potentially leading to other print quality issues.
Printing Pressure: The force exerted by the print heads onto the substrate can affect dot size. Excessive pressure can cause dots to spread, while insufficient pressure may result in incomplete ink transfer.
Ink-Substrate Interaction: The chemical and physical properties of both the ink and the substrate influence how the ink behaves upon contact. For instance, inks with strong surface tension may not wet the substrate evenly, leading to uneven dot distribution and gain.
Drying Process: UV flatbed printers cure ink instantly using ultraviolet light. However, the initial moments before curing can still allow for some dot spread, especially if the ink is not immediately exposed to sufficient UV intensity.
Measuring Dot Gain
Accurate measurement of dot gain is crucial for maintaining print quality consistency. Several methods can be employed:
Microscopic Examination: Using a high-resolution microscope, printers can examine dots before and after printing to measure the extent of spread. This method provides direct visual evidence of dot gain.
Spectrophotometric Analysis: By measuring the color density and comparing it to a standard, spectrophotometers can indirectly indicate dot gain. Changes in color density often correlate with dot size alterations.
Dot Gain Charts: Specialized test charts with known dot patterns can be printed and analyzed. By comparing the printed dots to the original digital pattern, the degree of gain can be quantified.
Software Tools: Some advanced printing software includes algorithms that can predict and compensate for dot gain based on substrate type, ink properties, and printing conditions.
Effects of Dot Gain on Print Quality
Dot gain directly impacts several aspects of print quality:
Color Accuracy: Expanded dots can alter the color mix, leading to shifts in hue, saturation, and brightness. This can result in a print that appears duller or more saturated than intended.
Detail and Sharpness: Fine details and sharp edges in images can become blurred as dots merge. This loss of detail is particularly noticeable in high-resolution graphics and text.
Tone Reproduction: In halftone images, dot gain can disrupt the delicate balance of dot sizes that create smooth gradients. This can lead to banding or posterization effects.
Consistency: Variations in dot gain across a print job can cause inconsistency, with some areas appearing darker or lighter than others. This lack of uniformity is unacceptable in professional printing.
Mitigating Dot Gain
To minimize dot gain and maintain optimal print quality, several strategies can be implemented:
Substrate Selection: Choose substrates that are compatible with the ink being used. Substrates with controlled porosity and good ink absorption properties can help reduce dot spread.
Ink Adjustment: Adjusting ink viscosity and surface tension can mitigate dot gain. Working with ink suppliers to find the right formulation for specific substrates is crucial.
Printing Parameters: Fine-tuning printing pressure, speed, and ink laydown can significantly reduce dot gain. Experienced printer operators understand the subtleties of these adjustments.
UV Curing Optimization: Ensuring that the UV curing system is properly calibrated and provides adequate exposure can minimize dot spread during the critical initial moments after ink deposition.
Software Compensation: Utilizing advanced printing software that includes dot gain compensation algorithms can help predict and counteract dot gain, ensuring more accurate prints.
Regular Calibration: Regularly calibrating both the printer and the measurement tools ensures that any deviations are quickly identified and corrected.
Dot gain is an intrinsic aspect of the UV flatbed printing process that, while often challenging, can be managed effectively with a comprehensive understanding and strategic approach. By delving into the causes, measurement techniques, and impacts of dot gain, printers can take proactive steps to minimize its effects, thereby enhancing print quality. Whether through careful substrate and ink selection, precise printing parameter adjustments, or leveraging advanced software tools, the goal remains the same: to produce prints that are as close to the original digital image as possible, preserving detail, color accuracy, and overall visual appeal.
In the world of UV flatbed printing, mastering dot gain is not just a technical achievement; it’s a testament to the printer’s commitment to excellence and customer satisfaction. As technology continues to evolve, so too will our understanding and ability to control dot gain, pushing the boundaries of what’s possible in digital printing.