UV Flatbed Printer: Understanding Ink Coverage and Adhesion
In the realm of digital printing, UV flatbed printers have emerged as a versatile and powerful tool, revolutionizing the way images and designs are applied to a wide array of substrates. These printers utilize ultraviolet (UV) light to cure inks almost instantly, providing numerous benefits including durability, high resolution, and the ability to print on diverse materials. Two crucial aspects that significantly influence the quality and effectiveness of UV flatbed printing are ink coverage and adhesion. This article delves into these factors, exploring their importance, how they are managed, and the impact they have on the final printed product.
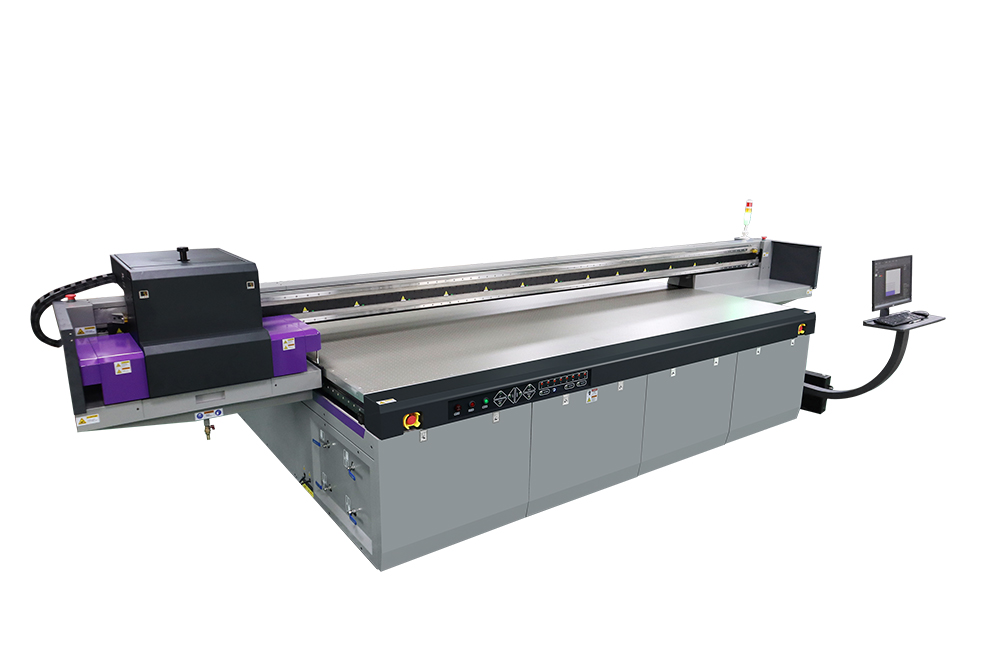
The Essence of Ink Coverage
Ink coverage refers to the amount of ink deposited on a substrate during the printing process. It is a critical parameter that directly affects the appearance, feel, and overall quality of the printed output. Proper ink coverage ensures that colors are vibrant, details are sharp, and the print has a professional finish. Conversely, inadequate or excessive ink coverage can lead to a host of issues, ranging from faded colors to smudging and even damage to the printer or the printed material.
Factors Influencing Ink Coverage
Several factors play a pivotal role in determining ink coverage:
Printer Settings: Modern UV flatbed printers come equipped with advanced software that allows operators to adjust ink coverage settings. These settings can be fine-tuned to suit different types of substrates and desired print effects.
Ink Type: The type of UV ink used can significantly impact coverage. Some inks are formulated to provide higher coverage while maintaining good adhesion and cure properties. Choosing the right ink for the job is crucial.
Substrate Absorbency: The absorbency of the substrate affects how much ink it can hold. Porous materials like paper and some fabrics may require less ink than non-porous surfaces such as glass or metal.
Print Resolution: Higher resolution prints often require more precise control over ink coverage to ensure that fine details are accurately reproduced.
Print Speed: Faster print speeds may result in less ink being deposited, as the printer has less time to apply each layer. Balancing speed and coverage is essential for optimal results.
Managing Ink Coverage
Effective management of ink coverage involves a combination of technical know-how and artistic sensibility. Operators must understand how to adjust printer settings to achieve the desired effect without compromising print quality. This may involve conducting test prints on different substrates to determine the optimal ink coverage for each material.
Additionally, regular maintenance of the printer, including cleaning the print heads and ensuring proper ink flow, is vital for maintaining consistent ink coverage. Using high-quality inks and substrates also plays a significant role in achieving predictable and satisfactory results.
The Importance of Adhesion
Adhesion refers to the ability of the ink to bond securely to the substrate. Good adhesion is essential for the longevity and durability of the printed product. If the ink does not adhere properly, it can lead to issues such as peeling, cracking, and fading over time. In extreme cases, poor adhesion can cause the ink to rub off completely, rendering the print useless.
Factors Affecting Adhesion
Several factors influence the adhesion of UV ink to a substrate:
Substrate Surface Energy: The surface energy of the substrate determines its ability to wet out and bond with the ink. High surface energy materials, such as metals and glasses, generally provide better adhesion than low surface energy materials like plastics and some coated papers.
Ink Chemistry: The chemical composition of the UV ink is crucial for achieving good adhesion. Inks are formulated with specific resins and additives that enhance their bonding capabilities.
Curing Process: The UV curing process itself plays a significant role in adhesion. Proper curing ensures that the ink polymerizes correctly, forming a strong bond with the substrate. Inadequate curing can result in weak adhesion and poor print durability.
Surface Preparation: Preparing the substrate surface before printing can improve adhesion. This may involve cleaning the surface to remove contaminants, applying a primer, or treating the surface to increase its surface energy.
Environmental Conditions: Temperature and humidity can affect ink adhesion. Extreme conditions may cause the ink to cure too quickly or too slowly, impacting its ability to bond properly with the substrate.
Enhancing Adhesion
To enhance adhesion, printer operators can take several steps:
Choose the Right Ink: Selecting an ink that is specifically formulated for the type of substrate being printed on can make a significant difference.
Prepare the Substrate: Properly cleaning and preparing the surface can improve ink adhesion. This may involve using solvents, primers, or surface treatments.
Optimize Curing Parameters: Ensuring that the UV curing process is optimized for the specific ink and substrate being used is crucial. This may involve adjusting the intensity and duration of the UV light.
Control Environmental Conditions: Maintaining a controlled environment, with stable temperature and humidity levels, can help ensure consistent ink adhesion.
Conduct Adhesion Tests: Performing adhesion tests on sample prints can provide valuable information about the effectiveness of the printing process and help identify potential issues before they become problematic.
The Synergy Between Ink Coverage and Adhesion
Ink coverage and adhesion are intertwined; they must be balanced to achieve optimal print quality. Excessive ink coverage can lead to poor adhesion if the ink does not cure properly, while inadequate coverage may result in a weak and unappealing print. Finding the right balance requires a thorough understanding of both the printer’s capabilities and the characteristics of the inks and substrates being used.
Moreover, the interaction between ink coverage and adhesion can vary depending on the specific application. For example, in graphic arts, where high-quality images and vibrant colors are essential, a slightly higher ink coverage may be desirable. In contrast, for industrial applications where durability and resistance to wear and tear are critical, ensuring strong adhesion may take precedence over achieving maximum ink coverage.
UV flatbed printers have transformed the printing industry, offering unparalleled versatility and quality. However, to fully harness their potential, it is essential to understand and manage ink coverage and adhesion effectively. By carefully considering the factors that influence these parameters and taking the necessary steps to optimize them, printer operators can produce prints that are not only visually appealing but also durable and long-lasting.
Whether you are a professional printer, a graphic designer, or an industrial manufacturer, mastering the art and science of ink coverage and adhesion is key to achieving successful UV flatbed printing outcomes. With the right knowledge, tools, and techniques, you can unlock the full potential of UV flatbed printing, creating stunning and resilient prints that meet and exceed your expectations.