UV Flatbed Printer: Understanding Printhead Alignment and Calibration
In the realm of digital printing, UV flatbed printers have revolutionized the way we approach print production, particularly in industries such as advertising, signage, packaging, and decorative arts. These versatile machines utilize ultraviolet (UV) light to instantly cure inks, enabling them to print on a wide array of substrates including rigid materials like wood, glass, metal, and plastics, as well as flexible media. One of the critical factors that determine the quality and precision of prints produced by UV flatbed printers is the alignment and calibration of the printheads. This article delves into the intricacies of printhead alignment and calibration, highlighting their importance, the processes involved, and tips for maintaining optimal performance.
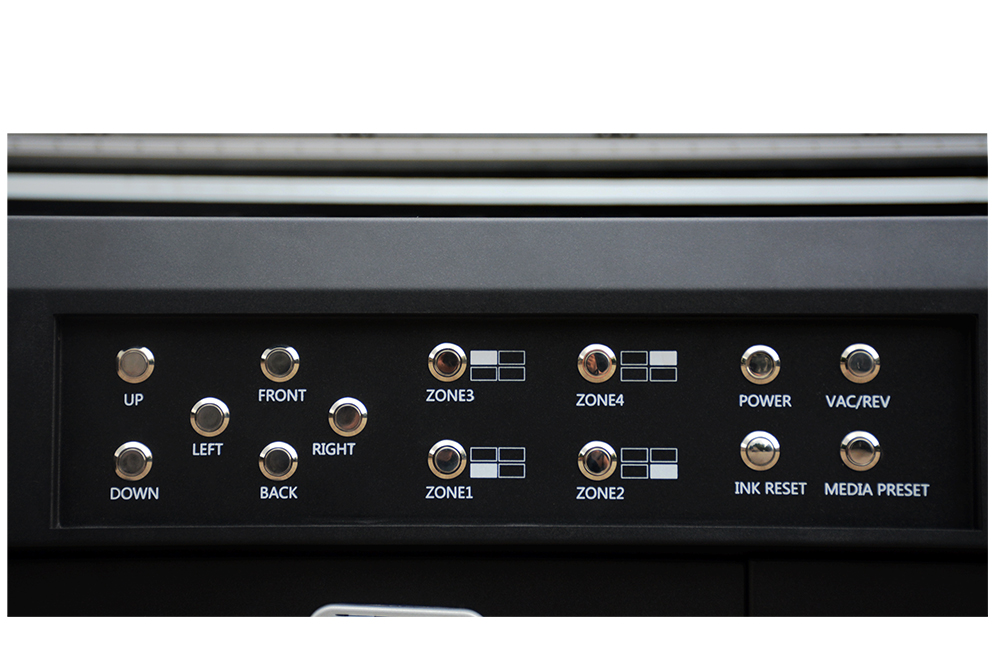
The Significance of Printhead Alignment and Calibration
Printhead alignment and calibration are fundamental procedures that ensure the accurate deposition of ink onto the substrate. Misalignment or miscalibration can lead to a multitude of print defects, including banding, misregistration, color shifts, and uneven ink coverage. These issues not only compromise the aesthetic appeal of the prints but can also result in costly reprints and wasted materials.
Alignment refers to the precise positioning of each printhead in relation to the others and to the substrate. It ensures that ink droplets from different colors or channels converge accurately at the intended location on the media, creating sharp, well-defined images and text. Calibration, on the other hand, involves adjusting the printer’s settings to optimize ink flow, droplet size, and firing frequency, ensuring consistent color output and image quality across different print jobs.
The Printhead Alignment Process
Printhead alignment typically involves both mechanical and software adjustments. The mechanical aspect ensures that the printheads are physically positioned correctly within the printer’s carriage or gantry system. This may require tightening screws, adjusting brackets, or using specialized tools to fine-tune the placement.
Software-based alignment is a more intricate process that involves printing a series of test patterns. These patterns usually consist of lines, crosses, or grids in various colors, designed to reveal any misalignments. The operator then uses the printer’s control panel or software interface to make adjustments. The software may offer automatic alignment features that analyze the test patterns and adjust the printhead positions accordingly. However, manual fine-tuning is often necessary to achieve the best results, especially in high-precision applications.
During the alignment process, it’s crucial to consider factors such as the printer’s resolution, the type of ink being used, and the specific characteristics of the substrate. For instance, some substrates may require slightly different alignment settings due to their surface texture or absorption properties.
Calibration: Ensuring Color Accuracy and Consistency
Calibration is a multi-step process that focuses on optimizing the printer’s color output. It begins with profiling, where a series of color patches are printed and measured using a spectrophotometer or colorimeter. This device captures the color data, which is then used to create an ICC (International Color Consortium) profile. The ICC profile acts as a reference, ensuring that the colors displayed on the computer screen match those printed by the UV flatbed printer.
In addition to color profiling, calibration may involve adjusting ink flow rates, droplet sizes, and the timing of ink firings. These adjustments help to maintain consistent ink coverage and prevent issues such as over-saturation or under-inking. Some printers feature advanced calibration tools that can automatically adjust these parameters based on real-time feedback from sensors monitoring the print process.
Regular calibration is essential, especially when switching between different types of ink or substrates, or when environmental conditions (such as temperature and humidity) change significantly. These factors can affect ink viscosity and drying times, impacting print quality.
Maintaining Optimal Printhead Alignment and Calibration
Maintaining printhead alignment and calibration is an ongoing process that requires diligence and attention to detail. Here are some tips for ensuring optimal performance:
Regular Cleaning and Maintenance: Ink residue and dust can accumulate on printheads and other components, affecting alignment and calibration. Regular cleaning with approved solutions and tools can help prevent these issues.
Environmental Control: Maintaining a stable environment in terms of temperature and humidity can minimize fluctuations that affect ink properties and print quality.
Quality Substrates: Using high-quality substrates that are compatible with UV inks can reduce the risk of ink absorption issues that could affect alignment and calibration.
Regular Testing: Periodically printing test patterns and evaluating them for alignment and color accuracy can help identify and address issues before they become significant problems.
Training and Expertise: Operators should be well-trained in the proper procedures for alignment and calibration. Understanding the printer’s specifications and limitations is crucial for achieving consistent results.
Software Updates: Keeping the printer’s firmware and software up to date can provide access to the latest alignment and calibration features, as well as bug fixes and performance improvements.
Preventive Maintenance: Scheduling preventive maintenance tasks, such as replacing worn parts or adjusting mechanical components, can help avoid unexpected downtime and ensure the printer remains in optimal condition.
UV flatbed printers offer unparalleled versatility and precision in digital printing, but achieving high-quality results depends heavily on proper printhead alignment and calibration. These processes are intricate and require a combination of mechanical precision, software sophistication, and operator expertise. By understanding the importance of alignment and calibration, following best practices for maintenance, and utilizing the latest technology and tools, printer operators can ensure that their UV flatbed printers produce stunning, accurate prints consistently.
In the fast-evolving world of digital printing, staying informed about advancements in alignment and calibration techniques is essential. As technology continues to progress, new methods and tools will emerge, making it easier to maintain optimal print quality and efficiency. By embracing these innovations and adhering to best practices, businesses can maximize the potential of their UV flatbed printers, delivering exceptional print results that meet the demands of a diverse range of applications.