UV Flatbed Printer: Understanding the Different Types of Printing Plates
UV Flatbed Printer: Understanding the Different Types of Printing Plates
In the realm of digital printing, UV flatbed printers have revolutionized the way images and designs are transferred onto various surfaces. These versatile machines are capable of printing on a wide array of materials, including glass, metal, plastic, wood, and more. One of the key components that contribute to the efficiency and quality of UV flatbed printing is the printing plate. This article delves into the different types of printing plates used in UV flatbed printers, exploring their characteristics, advantages, and applications.
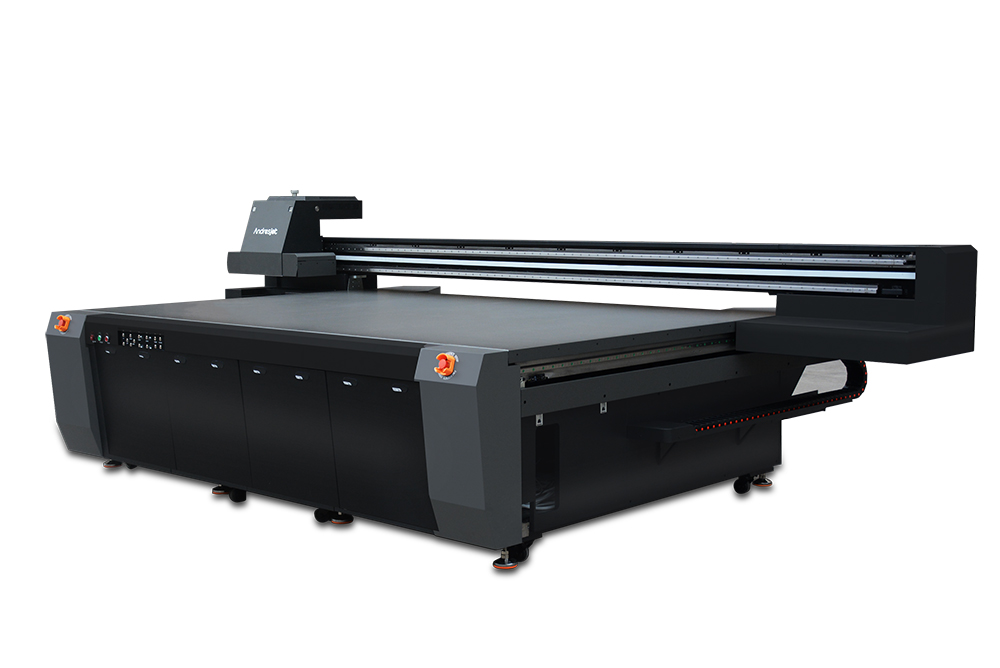
1. Introduction to UV Flatbed Printers
UV flatbed printers utilize ultraviolet (UV) light to cure or dry ink instantly after it is applied to the material. This technology allows for precise and high-resolution printing, making it ideal for applications that require intricate details and vibrant colors. The printer’s flatbed design enables it to accommodate materials of various sizes and thicknesses, further enhancing its versatility.
At the heart of every UV flatbed printer lies the printing plate, which plays a crucial role in transferring the ink onto the substrate. Understanding the different types of printing plates is essential for achieving optimal print results and ensuring the longevity of the printed designs.
2. Types of Printing Plates
UV flatbed printers employ several types of printing plates, each with its unique properties and applications. The most common types include:
2.1. Flexographic Plates
Flexographic plates, also known as flexo plates, are made of flexible materials such as rubber or photopolymer. They are ideal for printing on soft or uneven surfaces due to their ability to conform to the substrate’s contour. Flexo plates are relatively inexpensive and easy to produce, making them a popular choice for large-scale printing projects.
Advantages:
Cost-effective for large print runs.
Suitable for printing on a variety of surfaces, including corrugated cardboard and flexible packaging materials.
Ability to print with a wide range of inks, including water-based, solvent-based, and UV-curable inks.
Applications:
Packaging industry (bags, boxes, labels).
Textile printing.
Promotional materials.
2.2. Offset Plates
Offset plates are used in offset printing, a technique where the ink is transferred from the plate to a rubber blanket, then to the substrate. UV flatbed printers that utilize offset plates offer high-quality prints with sharp details and accurate color reproduction. These plates are typically made of aluminum and coated with a photosensitive material.
Advantages:
High print quality and resolution.
Suitable for printing on a wide range of materials, including paper, cardboard, and some plastics.
Efficient ink transfer, resulting in minimal ink waste.
Applications:
High-end packaging.
Fine art reproduction.
Marketing materials.
2.3. Screen Printing Plates
Screen printing plates, or stencil plates, are created by cutting a design into a fine mesh screen. Ink is then forced through the open areas of the screen onto the substrate. UV flatbed printers that use screen printing plates are ideal for printing thick layers of ink and achieving unique textures.
Advantages:
Ability to print with high ink opacity and thickness.
Suitable for printing on a variety of materials, including textiles, ceramics, and glass.
Versatile for creating textured effects and specialty finishes.
Applications:
Textile and apparel printing.
Decorative and promotional items.
Industrial and specialty printing.
2.4. Digital Printing Plates
Digital printing plates are a more recent innovation, utilizing digital technology to create the plate image directly. These plates offer high-resolution printing capabilities and quick turnaround times, making them ideal for short-run and customized printing jobs.
Advantages:
High-resolution printing with precise color control.
Rapid plate production, allowing for quick job changes and reduced downtime.
Suitable for printing on a wide range of materials.
Applications:
Short-run and customized packaging.
Point-of-purchase displays.
Prototyping and design validation.
3. Choosing the Right Printing Plate
Selecting the appropriate printing plate for a UV flatbed printer depends on several factors, including the substrate material, desired print quality, ink type, and production requirements. Consider the following when making your choice:
Material Compatibility: Ensure the plate is compatible with the substrate you intend to print on.
Print Quality: Choose a plate that can deliver the desired resolution and color accuracy.
Ink Compatibility: Verify that the plate is suitable for use with the ink type you plan to use.
Production Needs: Consider the volume of prints and the turnaround time required for your project.
4. Conclusion
UV flatbed printers have transformed the printing industry, offering versatility and high-quality output for a wide range of applications. Understanding the different types of printing plates and their respective advantages is crucial for achieving optimal print results. By selecting the appropriate plate for your specific needs, you can ensure that your UV flatbed printer delivers exceptional prints with lasting durability. As technology continues to advance, the future of UV flatbed printing and its printing plates looks promising, with even greater capabilities and applications on the horizon.