UV Flatbed Printer: Understanding the Printing Process
UV Flatbed Printer: Understanding the Printing Process
In the realm of digital printing, UV flatbed printers have emerged as a versatile and efficient technology, revolutionizing the way images and designs are transferred onto various surfaces. This article aims to provide a comprehensive understanding of the UV flatbed printing process, exploring its mechanics, applications, advantages, and considerations for optimal use.
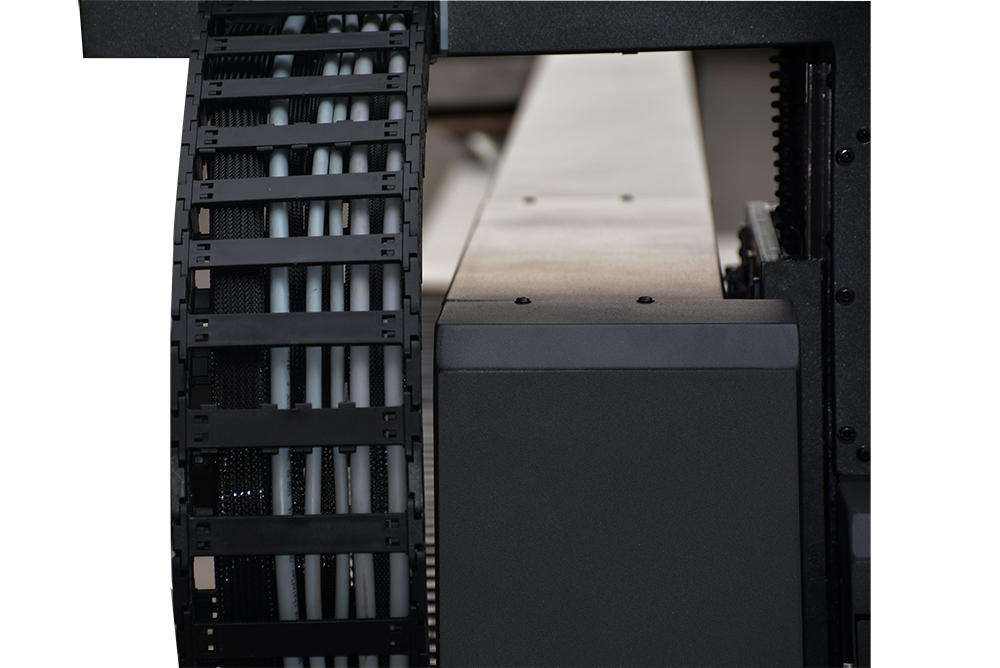
Introduction to UV Flatbed Printing
UV flatbed printing is a digital printing technique that utilizes ultraviolet (UV) light to cure or dry ink instantly after it is applied to a substrate. This method allows for precise and high-quality printing on flat or slightly curved surfaces, making it suitable for a wide range of materials including glass, plastic, wood, metal, and even certain textiles. The process involves the use of a specialized printer equipped with UV-curable inks and a UV light source, typically LEDs or mercury lamps, to instantly cure the ink as it exits the print head.
The Printing Process
Preparation of the Substrate: Before printing, the substrate must be properly prepared. This includes cleaning the surface to remove any dust, dirt, or oils that could affect print quality. Depending on the material, pretreatment such as sanding, priming, or coating might be necessary to enhance ink adhesion.
Design and File Preparation: The digital design is created or selected and prepared for printing. This involves converting the design into a printable format, adjusting colors and resolutions to match the printer’s specifications, and ensuring the file is properly sized for the substrate.
Printer Setup: The UV flatbed printer is calibrated to ensure accurate color reproduction and print quality. This includes adjusting the print head gap (the distance between the print head and the substrate), selecting the appropriate ink set, and configuring the UV light intensity and curing speed.
Ink Application: The design is printed onto the substrate using UV-curable inks. These inks remain in a liquid state until exposed to UV light, allowing for precise dot placement and control. The printer moves the print head across the substrate, depositing ink according to the digital design.
UV Curing: Immediately after ink application, the UV light source is activated, curing the ink instantly. This curing process solidifies the ink, creating a durable and vibrant print. The speed and intensity of the UV light can be adjusted to control the cure level and achieve desired print characteristics.
Post-Processing: Depending on the application, additional post-processing steps may be required. This can include cutting or trimming the substrate to size, applying protective coatings, or performing quality checks to ensure print integrity.
Applications of UV Flatbed Printing
UV flatbed printing’s versatility extends to a broad array of applications, including:
Signage and Display Graphics: UV flatbed printers are commonly used to produce high-quality signs, posters, and display graphics for retail stores, trade shows, and exhibitions.
Product Customization: From personalized phone cases to custom-printed promotional items, UV flatbed printing enables on-demand customization of various products.
Interior Decor: The ability to print on diverse materials makes UV flatbed printing ideal for interior design elements such as decorative panels, wall art, and furniture finishes.
Packaging and Labeling: UV flatbed printers can produce durable and eye-catching packaging and labels for products in industries ranging from food and beverage to cosmetics.
Industrial Applications: The technology is also utilized in industrial settings for printing on components, prototypes, and even directly on certain types of machinery parts.
Advantages of UV Flatbed Printing
High Quality: UV-curable inks produce sharp, vibrant prints with excellent color accuracy and detail.
Instant Curing: The UV curing process allows for immediate drying, reducing the risk of ink smudging or running and enabling faster turnaround times.
Versatility: The ability to print on a wide range of materials and surfaces makes UV flatbed printing highly adaptable to various applications.
Durability: UV-cured inks are resistant to fading, scratching, and chemicals, ensuring long-lasting prints.
Environmentally Friendly: Compared to traditional solvent-based inks, UV-curable inks emit lower levels of volatile organic compounds (VOCs), making them a more environmentally friendly option.
Considerations and Limitations
While UV flatbed printing offers numerous advantages, there are also considerations and limitations to be aware of:
Initial Investment: UV flatbed printers and their associated inks can be more expensive than traditional printing methods, making them a significant investment for some businesses.
Learning Curve: Achieving optimal print quality requires understanding the printer’s settings, ink characteristics, and substrate preparation, which may involve a learning curve for new users.
Material Compatibility: While UV flatbed printers can print on a variety of materials, some substrates may require special pretreatment or coatings to achieve desired results.
Print Speed: Compared to some other digital printing methods, UV flatbed printing can be slower, especially for large or complex prints.
Conclusion
UV flatbed printing has revolutionized the digital printing industry by offering high-quality, versatile, and durable printing solutions for a wide range of applications. Its ability to print on diverse materials and instantly cure inks using UV light provides numerous advantages, including fast turnaround times, environmental friendliness, and exceptional print quality. However, it’s important to consider the initial investment, learning curve, material compatibility, and print speed when evaluating UV flatbed printing for specific projects or business needs. With proper understanding and application, UV flatbed printing can unlock new creative possibilities and enhance efficiency in various industries.