UV Flatbed Printer: Understanding the Role of Ink Viscosity in Print Quality
UV Flatbed Printer: Understanding the Role of Ink Viscosity in Print Quality
In the realm of digital printing, UV flatbed printers have emerged as a versatile and efficient solution for producing high-quality prints on a wide array of materials. These printers utilize ultraviolet (UV) light to cure ink instantly, enabling rapid printing and minimizing the risk of ink smudging or bleeding. A crucial aspect of achieving optimal print quality with UV flatbed printers lies in understanding and managing ink viscosity, a factor that significantly influences the final output. This article delves into the intricacies of ink viscosity and its pivotal role in determining print quality.
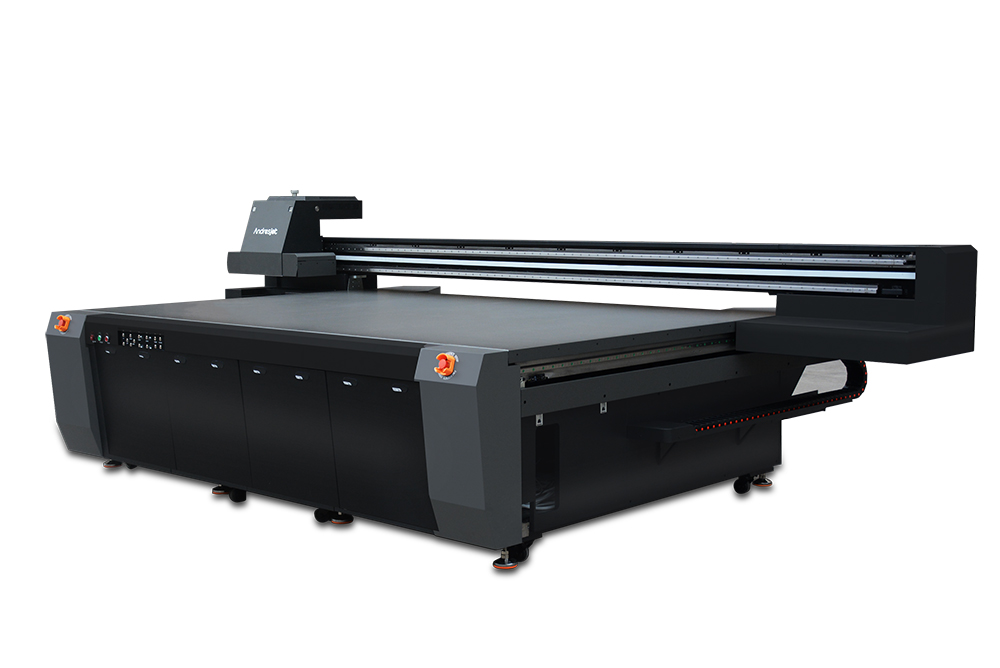
The Basics of Ink Viscosity
Ink viscosity refers to the resistance of ink to flow, essentially measuring its thickness or thinness. It is a critical parameter in printing as it directly affects how ink interacts with the substrate and the printer’s components. Viscosity is typically expressed in centipoise (cP) or Pascal-seconds (Pa·s), with lower values indicating thinner inks and higher values indicating thicker inks.
In UV flatbed printing, ink viscosity plays a multifaceted role. It influences ink spreadability, adhesion to the substrate, dot gain (the increase in ink diameter after deposition), and ultimately, the overall print resolution and appearance. Therefore, maintaining ink viscosity within an optimal range is paramount to achieving consistent, high-quality prints.
Ink Viscosity and Print Quality
Ink Spreadability and Dot Gain
Ink viscosity directly impacts how ink spreads on the substrate. If the ink is too viscous, it may not spread evenly, leading to poor ink laydown and visible banding or streaking in the printed image. Conversely, if the ink is too thin, it may spread excessively, causing dot gain and reducing print resolution. The ideal viscosity balance ensures that ink spreads uniformly without excessive spreading, preserving fine details and achieving crisp, clear prints.
Adhesion and Durability
The adhesion of ink to the substrate is crucial for long-lasting prints. Ink with appropriate viscosity ensures strong adhesion, preventing ink from peeling off or fading over time. This is particularly important for UV flatbed printing, where inks are cured instantly upon exposure to UV light. Incorrect viscosity can lead to weak adhesion, compromising the print’s durability and resistance to abrasion or chemicals.
Ink Drying and Curing
UV flatbed printers rely on UV light to cure ink instantly. Ink viscosity affects the curing process, as thicker inks may require more UV energy to cure completely. Insufficient curing can result in tacky surfaces, reduced ink hardness, and poor resistance to environmental factors. Conversely, overly thin inks may cure too quickly, leading to brittleness and cracking. Therefore, optimizing ink viscosity is essential for achieving proper curing and ensuring print durability.
Print Speed and Efficiency
Ink viscosity also impacts print speed and overall printer efficiency. Thicker inks may flow less smoothly through the printhead, leading to slower print speeds and increased wear on printer components. On the other hand, thinner inks may require frequent replenishment due to higher consumption rates. Finding the optimal viscosity balance enhances print speed and reduces maintenance needs, ultimately improving overall productivity.
Managing Ink Viscosity for Optimal Print Quality
Managing ink viscosity effectively requires a comprehensive understanding of the printing process, substrate characteristics, and ink properties. Here are some key strategies for optimizing ink viscosity in UV flatbed printing:
Temperature Control
Temperature plays a significant role in ink viscosity, with inks becoming thinner as temperature increases and thicker as it decreases. Maintaining a stable printing environment and controlling ink temperature can help stabilize viscosity levels and ensure consistent print quality.
Ink Formulation
Choosing the right ink formulation is crucial for achieving the desired viscosity. Manufacturers offer inks with varying viscosities to suit different printing applications and substrates. Selecting an ink specifically designed for UV flatbed printing ensures compatibility with the printer and optimal print quality.
Viscosity Adjustment
In some cases, adjusting ink viscosity may be necessary to achieve optimal print results. This can be accomplished by adding viscosity modifiers or diluents to the ink. However, it is essential to follow manufacturer recommendations and thoroughly test any adjustments to avoid compromising print quality or printer performance.
Regular Maintenance
Regular printer maintenance, including cleaning printheads and ink lines, helps maintain consistent ink flow and prevents viscosity-related issues. Keeping the printer in optimal condition ensures that ink viscosity remains stable and print quality remains high.
Substrate Compatibility
Different substrates require inks with specific viscosities to achieve optimal adhesion and print quality. Understanding the substrate’s porosity, texture, and ink receptivity is crucial for selecting the appropriate ink viscosity. Testing inks on the target substrate before commencing large-scale production ensures compatibility and minimizes the risk of print defects.
Conclusion
Ink viscosity is a critical factor in determining print quality in UV flatbed printing. It influences ink spreadability, adhesion, curing, and overall print efficiency. Understanding the intricacies of ink viscosity and implementing effective management strategies is essential for achieving consistent, high-quality prints. By controlling temperature, selecting appropriate ink formulations, adjusting viscosity when necessary, maintaining the printer, and considering substrate compatibility, UV flatbed printer users can optimize ink viscosity and unlock the full potential of their printing capabilities. As technology continues to advance, so too will our understanding and control of ink viscosity, further pushing the boundaries of print quality and versatility in UV flatbed printing.