What are the Benefits of Using a Rubber Pneumatic Bag in Logistics
In the realm of modern printing, UV flatbed printers have emerged as a revolutionary solution, offering high-quality, durable prints on a variety of substrates, from rigid plastics to wood and metal. Unlike traditional printers, UV flatbed printers use ultraviolet light to cure ink instantly, ensuring vibrant colors and resistance to fading. This technology has transformed industries such as advertising, packaging, and interior design by enabling on-demand, customizable printing solutions. Central to the functionality of these printers is the vacuum system, a critical component that ensures precise and consistent printing outcomes.
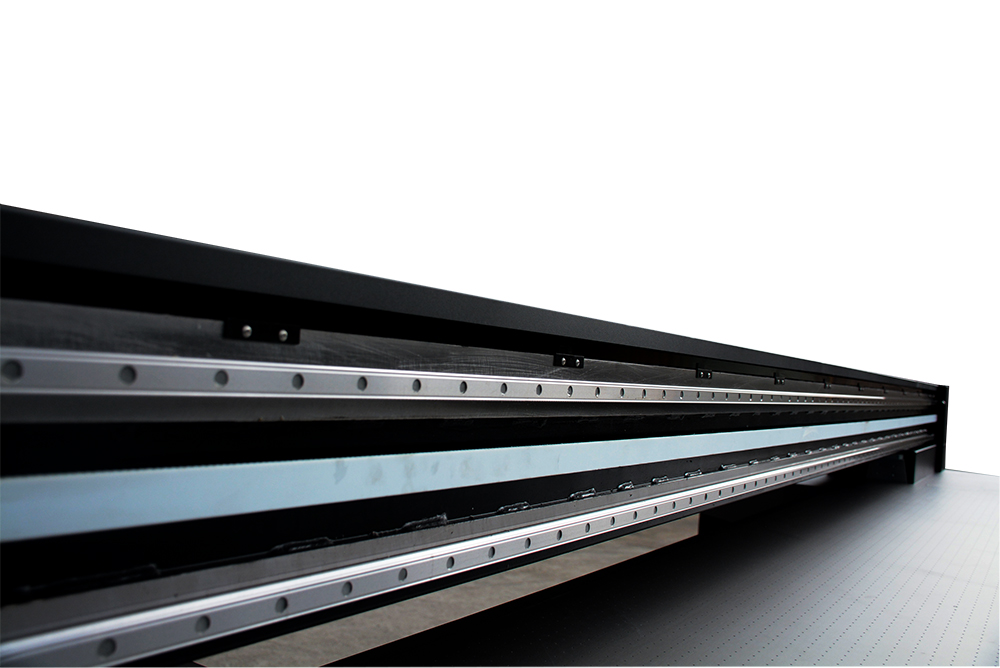
The Role of the Vacuum System in UV Flatbed Printers
At its core, the vacuum system in a UV flatbed printer serves a straightforward yet vital purpose: to securely hold the substrate in place during the printing process. This is crucial because any movement or misalignment can lead to smudged, blurry, or misplaced prints, compromising the quality of the final product. By creating a uniform suction force across the printing bed, the vacuum system ensures that the substrate remains flat and stable, even when the printer head moves rapidly across the surface. This stability is particularly important when printing on non-traditional materials like textured surfaces or thin, flexible substrates, where the risk of warping or shifting is higher.
Components of a Vacuum System in UV Flatbed Printers
A typical vacuum system in a UV flatbed printer consists of several key components:
Vacuum Pump: The heart of the system, responsible for generating the necessary suction. Modern vacuum pumps are designed to be energy-efficient and quiet, minimizing operational noise.
Vacuum Table: This is the flat surface where the substrate is placed. It features a grid of small holes or channels that allow air to be drawn out, creating the vacuum effect.
Valves and Controls: These regulate the flow of air and ensure that suction is applied only where needed, such as in specific zones of the printing bed.
Filters: To prevent dust and debris from entering the vacuum pump, filters are installed to trap particles and maintain system cleanliness.
Benefits of a Robust Vacuum System
A well-designed vacuum system offers numerous advantages for UV flatbed printers:
Enhanced Print Quality: By keeping the substrate stable, the vacuum system ensures that ink is deposited accurately, resulting in sharp, high-resolution prints.
Versatility: With adjustable suction levels, the system can accommodate a wide range of substrates, from lightweight papers to heavy-duty plastics.
Increased Productivity: Faster setup times and reduced waste due to misprints translate to higher throughput and cost savings.
Improved Safety: A securely held substrate reduces the risk of accidents during the printing process, such as materials being ejected from the bed.
Challenges and Solutions in Vacuum System Design
While vacuum systems are essential, they also present challenges. One common issue is uneven suction, which can occur if the vacuum table is damaged or if the pump’s capacity is insufficient. To address this, manufacturers often incorporate zoned vacuum systems that allow for independent control of suction in different areas of the bed. Additionally, regular maintenance, such as cleaning filters and inspecting seals, can prevent performance degradation over time.
Another challenge is noise. Traditional vacuum pumps can be loud, which may be a concern in environments where quiet operation is required. Innovations in pump design, such as the use of brushless motors and acoustic insulation, have significantly reduced noise levels without compromising suction power.
Maintenance and Troubleshooting Tips
To keep a UV flatbed printer’s vacuum system in optimal condition, follow these maintenance tips:
Regular Cleaning: Remove dust and debris from the vacuum table and filters to prevent clogs.
Inspect Seals: Check for wear or damage to the seals around the vacuum table and pump. Replace them if necessary to maintain suction efficiency.
Monitor Performance: Keep an eye on suction levels and listen for unusual noises, which could indicate a problem with the pump or valves.
If issues arise, troubleshooting steps may include:
Adjusting suction zones to ensure even coverage.
Testing the vacuum pump’s output to verify it meets the manufacturer’s specifications.
Replacing worn-out components, such as filters or hoses.
Future Innovations in Vacuum System Technology
As UV flatbed printing technology continues to evolve, so too will the vacuum systems that support it. Emerging trends include:
Smart Vacuum Systems: Integration with sensors and automation software allows for real-time adjustments to suction levels based on substrate type and print job requirements.
Energy-Efficient Designs: Newer vacuum pumps are being developed with advanced materials and motor technologies to reduce power consumption while maintaining performance.
Modular Systems: Future vacuum systems may be designed with interchangeable components, allowing for easy upgrades or repairs without replacing the entire unit.
Conclusion
The vacuum system in a UV flatbed printer is a silent yet indispensable component that ensures the quality, efficiency, and safety of the printing process. By understanding its role, components, and maintenance needs, operators can maximize the potential of their printing equipment. As technology advances, the vacuum system will continue to play a pivotal role in driving innovation in the world of digital printing, offering even greater precision, versatility, and sustainability.
For businesses and professionals relying on UV flatbed printers, investing in a robust vacuum system is not just a matter of convenience—it’s a strategic decision that can lead to better print quality, higher productivity, and a competitive edge in the market.