What Are the Best Practices for Using a UV Flatbed Printer?
What Are the Best Practices for Using a UV Flatbed Printer?
UV flatbed printers have revolutionized the printing industry, offering unparalleled versatility and precision in reproducing images and designs on various substrates. These printers utilize UV-curable inks that cure instantly when exposed to ultraviolet light, enabling them to print on a wide range of materials, including glass, metal, plastic, wood, and even fabric. However, to harness the full potential of a UV flatbed printer and ensure optimal print quality, it is essential to adhere to best practices. This article outlines the key considerations and best practices for using a UV flatbed printer effectively.
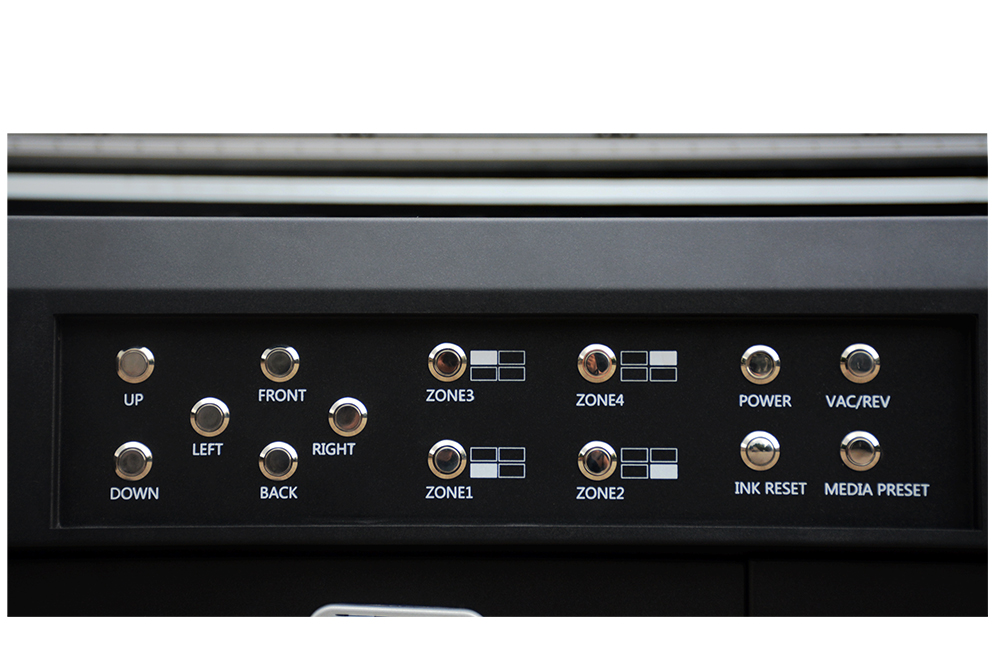
1. Understanding the Basics of UV Flatbed Printing
Before diving into the best practices, it is crucial to understand the fundamental principles of UV flatbed printing. UV flatbed printers work by depositing UV-curable ink onto the substrate in a controlled manner. The ink is then instantly cured by exposure to UV light, resulting in a durable and high-quality print. This technology allows for precise control over ink deposition, making it ideal for printing detailed graphics and achieving vibrant colors.
2. Preparing the Workspace
Ensure Proper Ventilation: UV inks emit volatile organic compounds (VOCs) during the curing process. Adequate ventilation is necessary to maintain a safe working environment and prevent the accumulation of harmful fumes.
Maintain Cleanliness: Dust, dirt, and debris can significantly affect print quality. Regularly clean the printer’s bed, inkjet heads, and surrounding area to prevent contamination.
Temperature and Humidity Control: Maintain a stable temperature and humidity level in the printing environment. Extreme temperatures or high humidity can affect ink curing and substrate stability.
3. Preparing the Substrate
Substrate Selection: Choose substrates that are compatible with UV inks. Conduct tests to ensure ink adhesion and curing on the chosen material.
Surface Preparation: Clean the substrate thoroughly to remove any dust, oil, or contaminants that could interfere with ink adhesion. For porous materials, consider applying a pre-treatment to enhance ink adhesion.
Flatness and Stability: Ensure the substrate is flat and stable on the printer bed. Use clamps or vacuum systems if necessary to prevent movement during printing.
4. Printer Settings and Calibration
Color Management: Calibrate the printer regularly to ensure accurate color reproduction. Use color profiling tools to create ICC profiles for different substrates.
Resolution and DPI: Adjust the printer settings according to the desired print resolution. Higher DPI (dots per inch) settings result in finer detail but may increase print time.
Ink Flow and Curing Settings: Fine-tune ink flow rates and UV curing intensity based on the substrate and ink type. Over-curing can lead to ink cracking, while under-curing may result in poor adhesion.
5. Printing Techniques
Test Prints: Always perform test prints before starting a large production run. This helps identify any potential issues with ink adhesion, curing, or color accuracy.
Print Modes: Utilize the printer’s different print modes (e.g., high-speed, high-quality) based on the specific requirements of the job.
Layering and Passes: For complex designs or deep colors, consider using multiple passes or layering techniques to achieve the desired effect.
6. Post-Printing Considerations
Curing Completion: Allow sufficient time for the ink to fully cure after printing, especially for thicker ink layers. Some printers offer post-cure units to ensure complete curing.
Handling and Packaging: Handle printed materials carefully to avoid damaging the freshly printed surface. Use appropriate packaging materials to protect the prints during transportation.
Cleaning and Maintenance: Regularly clean the printer’s inkjet heads and perform routine maintenance to prevent ink build-up and ensure optimal performance.
7. Safety Precautions
Personal Protective Equipment (PPE): Wear appropriate PPE, including gloves, safety glasses, and respirators, when working with UV inks.
Emergency Procedures: Familiarize yourself with the printer’s emergency stop procedures and have a fire extinguisher nearby, as UV inks can be flammable.
8. Training and Expertise
Operator Training: Ensure all operators are adequately trained on the specific UV flatbed printer model and its features.
Continuous Learning: Stay updated on new printing techniques, ink technologies, and software updates to enhance printing capabilities.
9. Environmental Considerations
Ink and Substrate Disposal: Dispose of used inks and substrates in an environmentally responsible manner, following local regulations.
Energy Efficiency: Look for UV flatbed printers with energy-saving features to reduce power consumption and environmental impact.
Conclusion
UV flatbed printers offer immense potential for creating high-quality prints on a wide array of substrates. However, achieving optimal results requires adherence to best practices throughout the printing process. From preparing the workspace and substrate to fine-tuning printer settings and post-printing considerations, every step plays a crucial role in ensuring print quality and longevity. By following these best practices, operators can harness the full capabilities of UV flatbed printers, producing vibrant, durable prints that meet or exceed client expectations. As technology continues to advance, staying updated on new techniques and innovations will further enhance the versatility and efficiency of UV flatbed printing.