What Are the Challenges of UV Flatbed Printing?
UV flatbed printing has revolutionized the printing industry, offering unparalleled versatility and precision in producing high-quality images on a wide range of substrates. This technology utilizes ultraviolet (UV) light to instantly cure inks, enabling rapid and efficient printing on materials such as glass, metal, wood, plastics, and even textiles. Despite its numerous advantages, UV flatbed printing is not without its challenges. This article delves into the primary hurdles faced by this innovative printing method and explores potential solutions to overcome them.
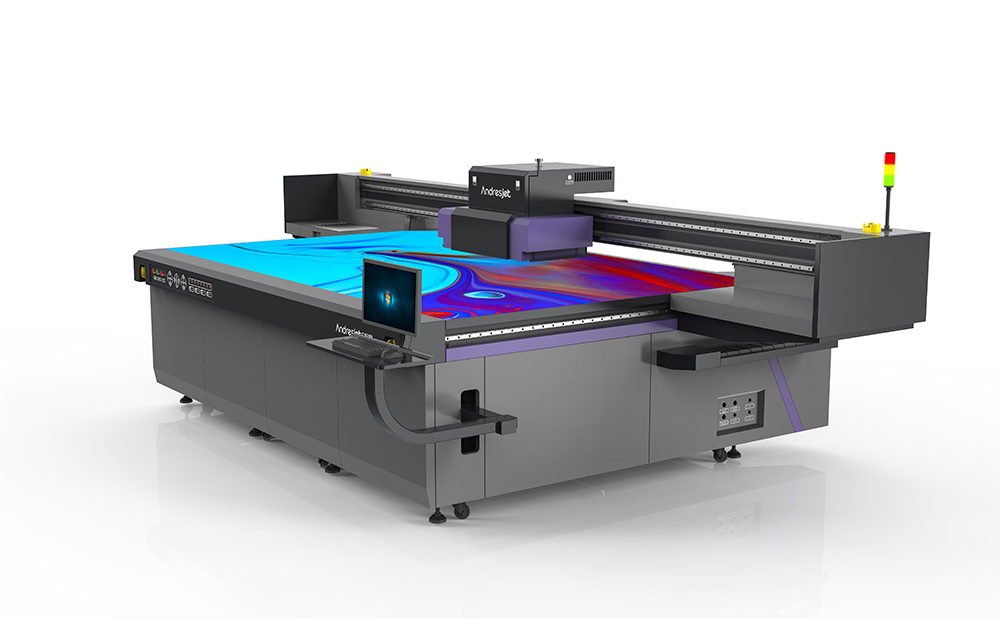
One of the foremost challenges in UV flatbed printing is achieving consistent print quality across different substrates. Each material has unique properties that can affect ink adhesion, absorption, and cure rates. For instance, porous surfaces like wood may absorb ink differently compared to non-porous surfaces like glass or metal. This variability can lead to inconsistencies in color, gloss, and durability. To address this challenge, printers must carefully select and test inks and substrates to ensure compatibility. Additionally, adjusting print settings such as ink layer thickness, cure times, and print speeds can help optimize print quality for specific materials.
Another significant challenge is the cost associated with UV flatbed printing. The initial investment in equipment can be substantial, with high-end machines often priced in the hundreds of thousands of dollars. Furthermore, the ongoing costs of UV-curable inks and maintenance can add up quickly. These expenses can be prohibitive for small businesses or startups. To mitigate these costs, some printers opt for leasing or financing options to spread out payments over time. Additionally, investing in energy-efficient equipment and optimizing ink usage through precise print settings can help reduce operational expenses.
The cure process itself presents another set of challenges. UV inks require exposure to ultraviolet light to cure properly. However, the intensity and wavelength of UV light can vary, impacting cure times and the final properties of the printed material. Insufficient curing can result in poor ink adhesion and smudging, while overcuring can cause brittleness or cracking. Ensuring consistent and adequate curing requires precise control over UV light sources and may necessitate the use of specialized equipment such as UV meters to monitor light output.
Moreover, the environmental impact of UV flatbed printing cannot be overlooked. UV-curable inks often contain volatile organic compounds (VOCs) and other chemicals that can be harmful to the environment if not handled properly. Disposing of waste ink and cleaning solutions also poses environmental challenges. To address these concerns, printers can adopt eco-friendly practices such as using low-VOC inks, recycling waste materials, and implementing proper waste disposal procedures. Additionally, investing in equipment that minimizes ink waste and reduces energy consumption can further reduce the environmental footprint of UV flatbed printing.
Registration accuracy is another critical challenge in UV flatbed printing. Ensuring that images are printed in the correct position and align perfectly with the substrate is essential for achieving a professional finish. Misregistration can occur due to factors such as substrate warping, ink shrinkage during curing, or mechanical inaccuracies in the printing equipment. To improve registration accuracy, printers can use advanced registration systems that employ cameras and sensors to detect and correct misalignments in real-time. Furthermore, regularly maintaining and calibrating printing equipment can help ensure consistent and accurate printing.
The speed of UV flatbed printing can also be a limiting factor, especially for high-volume production runs. While UV flatbed printers have made significant advancements in print speed, they may still not be able to match the throughput of traditional printing methods such as offset or screen printing. To increase productivity, printers can optimize print settings for faster cure times and reduce the number of print passes required for each job. Additionally, investing in multiple printing units or utilizing automated workflows can help increase overall production capacity.
Color management is another area where UV flatbed printing faces challenges. Achieving accurate and consistent color reproduction across different substrates and print runs can be difficult due to variations in ink absorption, surface texture, and lighting conditions. To ensure color accuracy, printers can use color management systems (CMS) that calibrate and profile printing equipment and substrates. These systems help to ensure that colors are consistently reproduced across different devices and media types.
In addition to technical challenges, UV flatbed printing also faces competition from other printing technologies. As the printing industry evolves, new and innovative printing methods are constantly emerging, each with its own set of advantages and disadvantages. To stay competitive, UV flatbed printers must continuously invest in research and development to improve their technology and offer unique value propositions to customers.
Lastly, the skill level required to operate UV flatbed printing equipment can be a challenge. These machines are highly sophisticated and require operators to have a good understanding of color management, ink chemistry, and print settings. Training and developing a skilled workforce is essential for ensuring the successful operation of UV flatbed printers. Printers can invest in training programs and certification courses to upskill their employees and maintain a competitive edge in the market.
In conclusion, UV flatbed printing offers numerous benefits in terms of versatility, precision, and quality. However, it is not without its challenges. Achieving consistent print quality across different substrates, managing costs, ensuring proper curing, addressing environmental concerns, improving registration accuracy, increasing print speed, managing color accuracy, competing with other printing technologies, and developing a skilled workforce are all critical challenges that UV flatbed printers must face. By adopting innovative solutions and best practices, printers can overcome these hurdles and harness the full potential of UV flatbed printing technology.