What Is the Best Way to Test the Quality of UV-Printed Materials?
What Is the Best Way to Test the Quality of UV-Printed Materials?
UV printing has revolutionized the printing industry with its ability to produce high-quality, durable, and vibrant prints on a wide range of materials. From marketing materials and packaging to artwork and decorative items, UV printing offers numerous advantages, including fast curing times, enhanced color accuracy, and the ability to print on various substrates. However, ensuring the quality of UV-printed materials can be challenging without proper testing methods. In this article, we will explore the best ways to test the quality of UV-printed materials, delving into visual inspection, mechanical testing, durability tests, color accuracy assessments, and the use of specialized equipment.
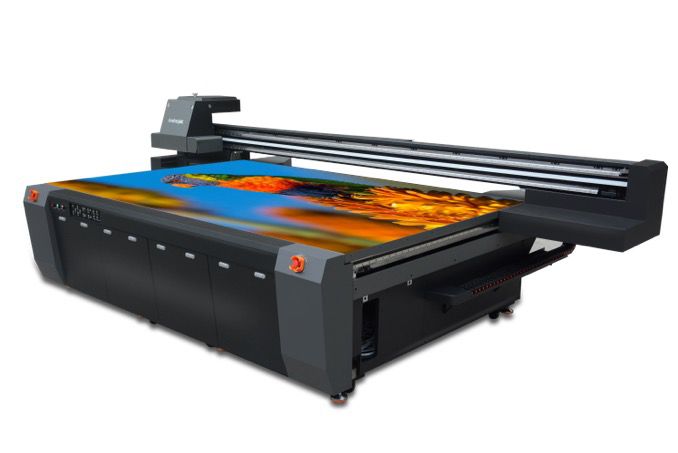
1. Visual Inspection: The First Line of Quality Control
Visual inspection is the most immediate and accessible method for assessing the quality of UV-printed materials. It involves examining the prints for visible defects, such as smudges, streaks, blurring, or uneven ink coverage. While this method is subjective and relies heavily on the inspector’s experience and eyesight, it is an essential first step in the quality control process.
To conduct a thorough visual inspection, follow these steps:
Illumination: Use appropriate lighting conditions, preferably natural light or standardized artificial light sources, to avoid color distortions.
Angle of View: Inspect the prints from different angles to catch defects that might only be visible from certain perspectives.
Magnification: Use magnifying tools or loupes to closely examine intricate details and small text elements.
Comparison: Compare the printed output to a digital proof or a previously approved sample to ensure consistency.
2. Mechanical Testing: Ensuring Durability and Strength
Mechanical testing evaluates the physical properties of UV-printed materials, focusing on their durability, flexibility, and resistance to external factors. This type of testing is crucial for applications where the printed materials will be subjected to stress, such as packaging or outdoor signage.
Key mechanical tests include:
Tensile Strength Test: Measures the force required to break the material, providing insight into its overall strength.
Elongation Test: Determines the material’s ability to stretch before breaking, which is particularly important for flexible substrates.
Tear Strength Test: Evaluates the resistance of the material to tearing, essential for applications requiring high durability.
Abrasion Resistance Test: Measures the material’s resistance to wear and tear from friction, simulating real-world conditions like handling and transport.
Specialized equipment like tensile testers, tear testers, and abrasion testers are used to perform these mechanical tests accurately. The results help ensure that the UV-printed materials meet the required standards for their intended use.
3. Durability Tests: Simulating Real-World Conditions
Durability tests go beyond mechanical properties, focusing on how well the UV-printed materials withstand environmental factors such as heat, humidity, UV exposure, and chemicals. These tests are crucial for ensuring that the prints remain vibrant and intact over time, especially in harsh conditions.
Common durability tests include:
Heat Resistance Test: Exposes the printed materials to elevated temperatures to assess color fading, ink bleeding, or substrate deformation.
Humidity Resistance Test: Subjects the prints to high humidity levels to check for ink bleeding, bubbling, or substrate swelling.
UV Exposure Test: Simulates long-term exposure to sunlight, assessing the resistance of inks to fading and discoloration.
Chemical Resistance Test: Exposes the prints to various chemicals, such as cleaning agents or solvents, to ensure the inks do not degrade or dissolve.
Performing these tests requires specialized chambers or environments that can accurately simulate the desired conditions. The results provide valuable insights into the long-term performance of the UV-printed materials, helping to identify potential issues before they arise in real-world applications.
4. Color Accuracy: Ensuring Consistency and Vibrancy
Color accuracy is a critical aspect of UV printing, particularly for applications where brand consistency and visual appeal are paramount. Testing for color accuracy involves comparing the printed colors to a standardized color reference, such as a digital proof or a PANTONE color swatch.
Techniques for assessing color accuracy include:
Visual Comparison: Using a color-calibrated monitor, compare the printed output directly to the digital proof. This method is subjective but can quickly identify significant color deviations.
Color Measurement Devices: Spectrophotometers and colorimeters are specialized instruments that measure color values (such as Lab* or RGB) and provide quantitative data on color differences (ΔE values).
Color Management Systems (CMS): Software solutions that help manage and calibrate colors across different devices and media, ensuring consistency throughout the printing process.
Regular calibration of printing equipment and color measurement devices is essential to maintain color accuracy. By continuously monitoring and adjusting the printing process, you can ensure that the UV-printed materials meet the desired color standards.
5. Specialized Equipment: Advanced Testing Techniques
In addition to the aforementioned methods, several specialized pieces of equipment can be used to test the quality of UV-printed materials more comprehensively. These include:
Microscopes: High-resolution microscopes can be used to examine the ink’s adhesion to the substrate, the presence of micro-defects, and the overall print quality at a microscopic level.
Thickness Gauges: Measure the ink layer’s thickness, ensuring consistent ink deposition and preventing issues like ink bleeding or cracking.
Adhesion Testers: Evaluate the bond strength between the ink and the substrate, crucial for ensuring that the print remains intact over time.
Gloss Meters: Measure the surface gloss of the printed materials, which can affect the overall visual appeal and perceived quality.
Using these advanced tools requires training and expertise, but they provide invaluable data for optimizing the UV printing process and ensuring the highest quality output.
Conclusion
Testing the quality of UV-printed materials is a multifaceted process that involves visual inspection, mechanical testing, durability tests, color accuracy assessments, and the use of specialized equipment. Each method plays a crucial role in ensuring that the prints meet the desired standards for appearance, durability, and performance.
By incorporating these testing techniques into your quality control process, you can identify potential issues early, make informed decisions to improve the printing process, and ultimately deliver high-quality UV-printed materials that meet or exceed customer expectations. Whether you are a printer, a designer, or a quality control manager, understanding and implementing these testing methods will help you achieve excellence in UV printing.