What is the Difference Between Solvent and UV Printing?
What is the Difference Between Solvent and UV Printing?
In the realm of digital printing, two prominent technologies stand out: solvent printing and UV printing. Both methods have gained significant popularity in various industries, including advertising, signage, and even fine art reproduction, due to their ability to produce high-quality prints on a wide range of materials. However, despite their shared goal of achieving vibrant and durable prints, solvent and UV printing differ significantly in terms of ink composition, printing process, application versatility, environmental impact, and cost-effectiveness. This article delves into the intricacies of both technologies to provide a comprehensive understanding of their distinct features and advantages.
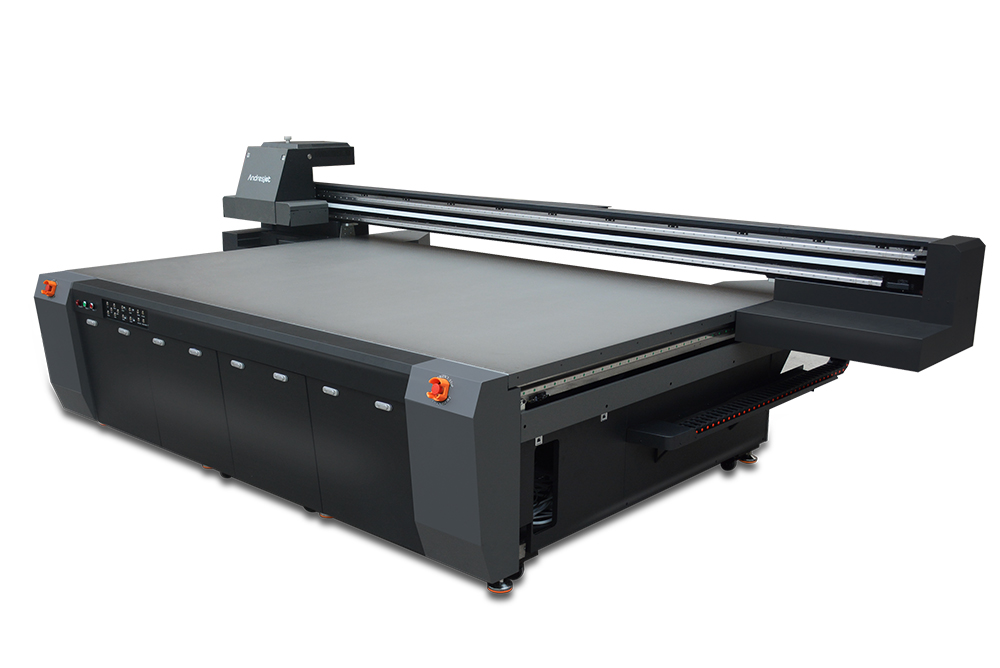
Ink Composition: The Core Difference
The fundamental difference between solvent and UV printing lies in the composition of the inks used. Solvent inks are formulated with solvents, typically a mixture of volatile organic compounds (VOCs), which act as carriers for the pigment or dye. These inks are liquid at room temperature and require evaporation of the solvent during or after the printing process to fix the ink onto the substrate.
On the other hand, UV inks are specially designed to cure (or dry) instantly when exposed to ultraviolet (UV) light. UV inks contain photoinitiators that react with UV radiation, triggering a chemical reaction that transforms the ink from a liquid to a solid state in a matter of seconds. This rapid curing process is a defining characteristic of UV printing.
Printing Process: Workflow and Equipment
The printing process for solvent and UV printing also differs significantly. Solvent printers typically employ piezoelectric or thermal printheads to deposit ink onto the media. After printing, the solvent must evaporate, which can be aided by heaters or simply by allowing time for natural evaporation. This evaporation step is crucial for achieving the final print quality and durability.
UV printers, however, integrate UV lamps into the printing system. As the ink is deposited onto the substrate, it is immediately exposed to intense UV light, which initiates the curing process. This inline curing allows for immediate handling and finishing of the printed material, as the ink is already dried and fixed. UV printers often have a more complex setup due to the need for precise UV light exposure control.
Application Versatility
Both solvent and UV printing offer versatility in terms of the materials they can print on, but each has its own strengths. Solvent inks are known for their ability to adhere to a wide variety of substrates, including vinyl, mesh, polycarbonate, and certain textiles, making them ideal for outdoor signage and banners that require flexibility and weather resistance.
UV inks, while also capable of printing on these materials, excel in applications where immediate curing is essential, such as floor graphics, rigid signboards, and packaging materials. UV printing’s ability to cure instantly on various substrates, including plastics and metals, makes it highly versatile for industrial and specialized applications.
Environmental Impact
Environmental considerations are a crucial aspect when comparing solvent and UV printing. Solvent inks, due to their VOC content, can emit strong odors during printing and drying, which may require special ventilation systems to maintain a safe working environment. Moreover, the VOCs released into the atmosphere contribute to air pollution and can have adverse health effects.
UV inks, in contrast, are generally considered more environmentally friendly. They contain no or low levels of VOCs, reducing odor and air pollution concerns. Additionally, the curing process is more efficient, consuming less energy overall compared to solvent ink evaporation methods. UV printing also generates minimal waste, as unused ink can often be recycled or reused.
Cost-Effectiveness and Durability
Cost-effectiveness is another factor that differentiates solvent and UV printing. Solvent printers are typically more affordable to purchase and operate, making them an attractive choice for startups or businesses with budget constraints. However, the long-term costs, including ink consumption, maintenance, and potential ventilation system expenses, should be considered.
UV printers, while initially more expensive, offer several advantages that can offset these costs over time. The instant curing process reduces ink waste and allows for faster production cycles, increasing efficiency. UV prints are also known for their exceptional durability, resistance to fading, and scratch resistance, which can justify the higher investment for applications requiring long-lasting quality.
Color Gamut and Print Quality
Both solvent and UV printing can achieve vibrant and high-resolution prints, but there are differences in color gamut and print quality. Solvent inks are known for their ability to produce deep, rich colors, particularly in outdoor applications where they can withstand environmental factors without significant degradation.
UV inks, on the other hand, often provide a broader color gamut due to advancements in ink chemistry. UV printing can achieve a wider range of vibrant and accurate colors, making it suitable for applications requiring precise color matching or reproduction, such as fine art prints or high-end packaging.
Conclusion
In conclusion, the choice between solvent and UV printing ultimately depends on specific application requirements, budget considerations, and environmental priorities. Solvent printing offers affordability and versatility across various substrates, while UV printing provides instant curing, environmental advantages, and superior durability and color reproduction. Understanding the distinct features and advantages of each technology enables businesses and individuals to make informed decisions that align with their unique needs and goals in the digital printing landscape.