What is the Difference Between UV and Solvent Printing?
What is the Difference Between UV and Solvent Printing?
In the realm of digital printing, two prominent technologies that often spark curiosity are UV printing and solvent printing. Both methods have gained significant popularity across various industries, including advertising, packaging, and decorative arts, due to their ability to produce high-quality prints on a wide range of materials. However, they differ fundamentally in their ink composition, curing process, environmental impact, and application versatility. This article delves into the intricacies of UV and solvent printing, highlighting their key differences and respective advantages.
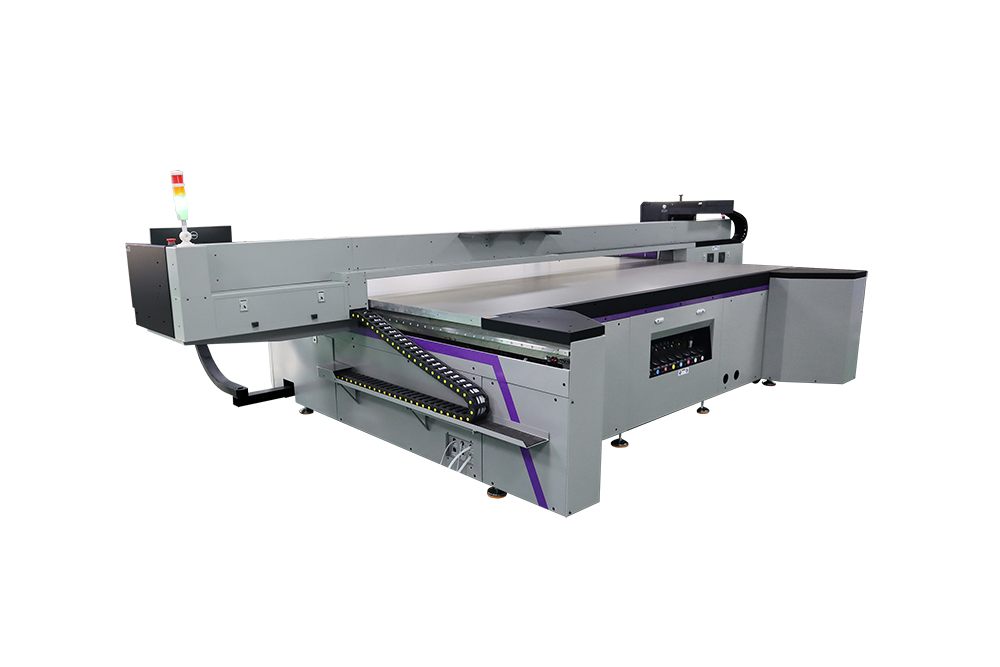
Understanding UV Printing
UV printing, short for ultraviolet printing, is a digital printing technique that utilizes UV-curable inks. These inks are formulated to cure or dry instantly when exposed to ultraviolet light. The process involves applying ink onto a substrate and then immediately exposing it to high-intensity UV lamps, which trigger a chemical reaction that solidifies the ink, creating a durable and vibrant print.
One of the defining features of UV printing is its ability to print on almost any material, including plastics, glass, metal, wood, and even flexible substrates like vinyl without the need for pre-treatment or priming. This versatility makes UV printing an attractive choice for applications requiring direct-to-object printing or those seeking to achieve unique textures and finishes.
Moreover, UV prints are known for their exceptional durability. The cured ink becomes resistant to fading, scratching, and chemical exposure, making it suitable for outdoor applications where longevity is crucial. Additionally, UV printing offers precise color control and high resolution, ensuring sharp images and vivid colors that can rival traditional printing methods.
Exploring Solvent Printing
Solvent printing, on the other hand, employs solvent-based inks that contain organic compounds as the primary carrier for the pigment or dye. These inks are designed to evaporate slowly, allowing the ink to penetrate the surface of the material being printed upon. Once the solvent evaporates, the pigment remains, forming the printed image.
Solvent printing is particularly suited for large-format applications, such as billboards, banners, and vehicle wraps, due to its ability to adhere well to various plastics and vinyl materials. The inks used in solvent printing are known for their flexibility and elasticity, which allows prints to conform to curved surfaces without cracking or peeling.
While solvent printing offers excellent print quality and versatility, it does have some drawbacks. The evaporation of solvents during the printing and drying process can release volatile organic compounds (VOCs) into the air, posing potential health risks to operators and contributing to environmental pollution. As a result, proper ventilation and safety measures are essential when working with solvent-based inks.
Key Differences Between UV and Solvent Printing
Ink Composition and Curing Process:
UV printing uses UV-curable inks that solidify upon exposure to ultraviolet light.
Solvent printing employs solvent-based inks that dry through the evaporation of the solvent carrier.
Environmental Impact:
UV printing is generally considered more environmentally friendly since it produces minimal VOC emissions and requires less energy for curing.
Solvent printing releases VOCs during the printing and drying process, necessitating proper ventilation and safety precautions.
Material Compatibility:
UV printing is highly versatile, capable of printing on almost any material without pretreatment.
Solvent printing is well-suited for plastics, vinyl, and other flexible materials but may require specific substrates for optimal results.
Durability and Finish:
UV prints are extremely durable, resistant to fading, scratching, and chemicals, making them ideal for outdoor applications.
Solvent prints offer good durability but may not match the longevity of UV prints, especially in harsh environments.
Color and Resolution:
Both UV and solvent printing can achieve high-resolution prints with vibrant colors, but UV printing often offers more precise color control due to the instant curing process.
Cost and Efficiency:
UV printing can be more cost-effective for short-run jobs due to its quick curing time and minimal setup requirements.
Solvent printing might be more economical for large-scale productions, especially when printing on traditional materials like vinyl.
Choosing Between UV and Solvent Printing
The decision between UV and solvent printing ultimately depends on specific project requirements, budget considerations, and environmental concerns. UV printing is often the preferred choice for applications demanding high durability, precise color accuracy, and the ability to print on a wide array of materials. Its environmental advantages and efficient curing process also make it an attractive option for many businesses.
Solvent printing, however, remains a viable choice for large-format printing, particularly when working with flexible materials and seeking cost-effectiveness for bulk productions. Its ability to adhere well to curved surfaces and its proven track record in outdoor advertising applications make it a reliable option despite its environmental drawbacks.
In conclusion, both UV and solvent printing offer unique advantages and cater to different needs within the digital printing industry. As technology continues to advance, these methods are likely to evolve, further enhancing their capabilities and expanding their application possibilities. Understanding the distinct characteristics of each technique enables businesses and individuals to make informed decisions, ensuring the best possible outcome for their specific printing needs.