What Is the Difference Between UV Flatbed and Traditional Printing?
What Is the Difference Between UV Flatbed and Traditional Printing?
The printing industry has evolved significantly over the years, with technological advancements driving innovation and efficiency. Among the various printing techniques available today, UV flatbed printing and traditional printing stand out as two distinct methods offering unique advantages and applications. Understanding the differences between these two printing processes is crucial for graphic designers, print shops, and anyone seeking high-quality printed materials. This article delves into the key distinctions between UV flatbed printing and traditional printing, examining aspects such as technology, materials, cost, speed, quality, environmental impact, and versatility.
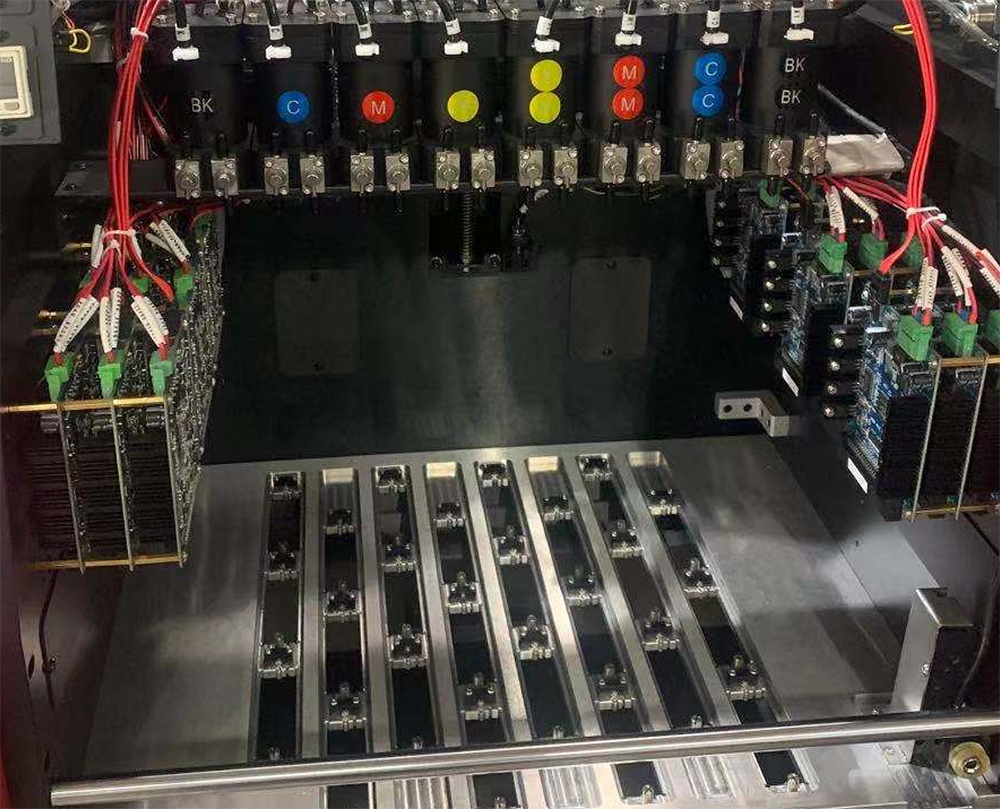
Technology and Equipment
UV Flatbed Printing:
UV flatbed printing employs modern digital technology that utilizes ultraviolet (UV) light to instantly dry inks as they are applied to the substrate. This technology allows for direct printing onto a wide range of flat and rigid materials, including metals, plastics, glass, woods, and textiles, without the need for curved or flexible media paths. UV flatbed printers use high-intensity UV-LED or UV-arc lamps to cure the inks, ensuring rapid drying and immediate handling of the printed materials.
The printing heads in UV flatbed printers can often be configured with varying resolutions, typically ranging from 600 to 2400 dots per inch (DPI), enabling intricate detail and vibrant color reproduction. Moreover, UV inks are formulated to be highly durable, resistant to fading, scratching, and chemicals, making them suitable for outdoor applications and high-traffic environments.
Traditional Printing:
Traditional printing methods, such as offset lithography, screen printing, and flexography, have been around for centuries and have evolved gradually over time. Offset printing, in particular, is widely used for commercial printing jobs due to its cost-effectiveness and high-volume capabilities. It involves transferring ink from a plate to a blanket and then to the printing surface, typically paper.
Offset printing uses water-based inks that require drying time, either through air drying or the use of heated dryers. The process can be highly automated, making it efficient for large-scale production runs. However, it is generally limited to flexible, flat media, such as paper, cardboard, and some types of plastics, and requires plates to be created for each color in the design, which can be time-consuming and costly for short runs.
Materials Compatibility
UV Flatbed Printing:
UV flatbed printing’s most significant advantage lies in its versatility when it comes to materials. The technology can print directly onto an extensive range of substrates, from rigid materials like metals and acrylics to flexible ones like fabrics and vinyl. This capability allows for the creation of unique and custom items that would be difficult or impossible to produce using traditional methods.
The ability to print on non-traditional materials opens up new design possibilities and market opportunities. For instance, UV flatbed printing can be used to create personalized phone cases, decorative wall panels, signage, and even prototypes for industrial design. The direct-to-substrate printing process eliminates the need for lamination or other finishing steps, simplifying the production workflow.
Traditional Printing:
Traditional printing methods, particularly offset printing, are primarily suited for printing on paper and paper-based materials. While advancements have expanded the range of materials that can be used, such as specialty papers and coated stocks, they are generally limited to flexible, flat surfaces.
Offset printing’s material limitations can be a drawback for projects requiring unique or non-traditional substrates. Additionally, the need for plates and the associated setup costs make it less economically viable for short runs or jobs with frequent design changes.
Cost and Efficiency
UV Flatbed Printing:
UV flatbed printing is generally more expensive than traditional printing methods in terms of initial equipment costs. High-quality UV flatbed printers are sophisticated machines that require significant investment. However, the technology’s ability to print directly onto a variety of materials without the need for plates, intermediate steps, or additional finishing processes can offset these costs in the long run, particularly for short-run and custom jobs.
UV flatbed printing also offers faster turnaround times, as there is no need for plate preparation or extensive setup. This can be a significant advantage for businesses requiring quick prototyping, personalized items, or small-batch production.
Traditional Printing:
Traditional printing methods, especially offset printing, are more cost-effective for large-volume production runs. The high initial setup costs, including plate creation and makeready procedures, are amortized over a larger number of prints, making each unit cheaper.
Offset printing’s efficiency in handling large volumes makes it the preferred choice for mass-produced materials like newspapers, magazines, and packaging. However, for smaller jobs, the setup costs can make the overall price prohibitive, leading to higher per-unit expenses.
Speed and Turnaround Time
UV Flatbed Printing:
UV flatbed printers are known for their rapid printing speeds and short turnaround times. The direct-to-substrate process eliminates the need for plates and other preparatory steps, allowing for quicker job setups. Additionally, the instant drying of UV inks means that printed materials can be handled and finished immediately after printing.
This speed and efficiency make UV flatbed printing ideal for short-run jobs, personalized items, and prototypes that require quick turnaround times. It also enables print shops to offer more flexible scheduling and quicker response times to customer requests.
Traditional Printing:
Traditional printing methods, particularly offset printing, are generally slower due to the need for plate preparation, makeready, and ink drying processes. The setup time can be significant, especially for jobs with multiple colors or intricate designs.
However, once the setup is complete, offset printing can achieve high printing speeds, making it well-suited for large-volume production runs. The balance between setup time and production speed often makes offset printing the most economically viable option for high-volume jobs.
Print Quality
UV Flatbed Printing:
UV flatbed printing offers exceptional print quality, with high-resolution capabilities that can produce intricate details and vibrant colors. The use of UV inks ensures high durability and resistance to fading, scratching, and environmental factors, making printed materials suitable for both indoor and outdoor applications.
The direct-to-substrate printing process also eliminates the potential for ghosting or registration errors that can occur in traditional printing methods where multiple printing passes are required. This results in cleaner, more accurate prints with consistent color and detail.
Traditional Printing:
Traditional printing methods, particularly offset printing, are also capable of producing high-quality prints. Offset printing is known for its sharp, clean lines and vibrant color reproduction, making it ideal for high-resolution graphics and photographic images.
However, the quality can be affected by factors such as plate wear, ink consistency, and paper absorption. Additionally, registration errors can occur when printing multiple colors, requiring careful alignment and calibration to ensure accuracy.
Environmental Impact
UV Flatbed Printing:
UV flatbed printing is generally considered more environmentally friendly than traditional printing methods. The use of UV inks, which do not contain volatile organic compounds (VOCs), reduces emissions and minimizes the impact on indoor air quality.
Additionally, the direct-to-substrate printing process eliminates the need for plates, chemicals, and waste associated with traditional printing setups. UV flatbed printers also use less ink and water compared to offset printing, further reducing waste and environmental footprint.
Traditional Printing:
Traditional printing methods, particularly offset printing, can have a significant environmental impact. The use of water-based inks and solvents can result in emissions of VOCs, which can contribute to air pollution.
The plate-making process generates waste, and the use of chemicals for cleaning and maintenance can also have adverse effects on the environment. Additionally, offset printing often results in significant paper waste, especially during the makeready and proofing stages.
Versatility and Applications
UV Flatbed Printing:
UV flatbed printing’s versatility in terms of materials and applications is one of its most compelling advantages. The ability to print directly onto a wide range of substrates enables the creation of unique and custom items that would be difficult or impossible to produce using traditional methods.
This versatility makes UV flatbed printing ideal for a wide range of applications, including signage, display graphics, decorative panels, prototypes, personalized items, and even functional parts for industrial design. The technology’s ability to handle both rigid and flexible materials further expands its potential applications.
Traditional Printing:
Traditional printing methods, particularly offset printing, are highly effective for producing large volumes of printed materials, such as newspapers, magazines, books, and packaging. The cost-effectiveness and high-quality output make it the preferred choice for these applications.
However, its limitations in terms of materials and customization can restrict its versatility. Traditional printing methods are generally less suitable for short-run jobs, personalized items, or projects requiring unique or non-traditional materials.
Conclusion
UV flatbed printing and traditional printing each offer unique advantages and are suited for different types of projects and applications. UV flatbed printing stands out for its versatility in terms of materials, high print quality, and fast turnaround times, making it ideal for short-run jobs, personalized items, and unique applications.
Traditional printing methods, particularly offset printing, excel in cost-effectiveness and high-volume production, making them the preferred choice for large-scale projects like newspapers, magazines, and packaging. Understanding the differences between these two printing processes can help businesses and designers make informed decisions about the best printing method for their needs.