What Is the Impact of Humidity on UV Flatbed Printer Performance?
What Is the Impact of Humidity on UV Flatbed Printer Performance?
In the realm of digital printing, UV flatbed printers have emerged as a versatile and efficient technology, capable of producing high-quality prints on a wide range of materials. These printers utilize ultraviolet (UV) light to cure inks instantly, enabling fast and durable printing results. However, like any precision machinery, their performance can be influenced by various environmental factors, with humidity being a significant one. This article delves into the impact of humidity on UV flatbed printer performance, exploring the underlying mechanisms, potential issues, and strategies for mitigation.
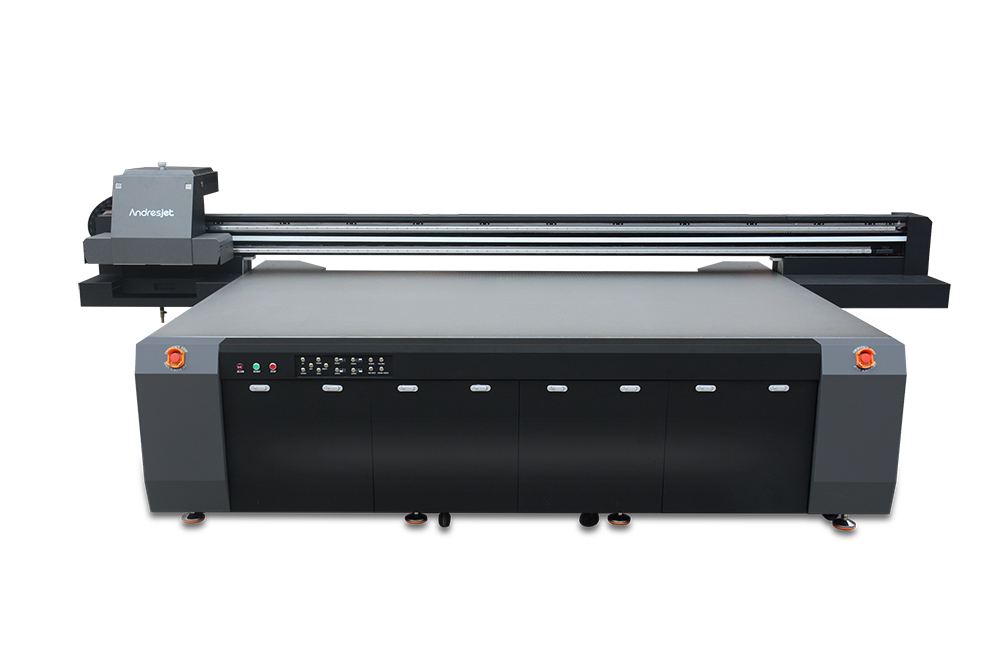
Understanding Humidity and Its Effects
Humidity, the amount of water vapor present in the air, is a crucial environmental parameter that can significantly affect the operation and output quality of UV flatbed printers. High humidity levels can lead to condensation, while low humidity can result in static electricity and material deformation. Both extremes can disrupt the delicate balance required for optimal print quality.
1. Ink Curing and Adhesion
UV inks cure through a photochemical reaction when exposed to UV light. Humidity can influence this process by altering the surface tension of the ink and the substrate. In high humidity conditions, the excess moisture in the air can interfere with the ink’s ability to properly adhere to the material, leading to issues such as ink bleeding, poor curing, and reduced print durability. Conversely, low humidity can cause the ink to dry too quickly on the printhead, potentially leading to clogged nozzles and reduced print quality.
2. Material Expansion and Contraction
Many printing substrates, especially wooden or paper-based materials, are sensitive to humidity changes. High humidity can cause these materials to expand, while low humidity can lead to contraction. These dimensional changes can affect the flatness of the substrate, leading to registration errors, ink cracking, or even substrate warping during the printing process.
3. Electrical Components and Static Electricity
UV flatbed printers are equipped with sensitive electrical components that control precise movements and ink dispensing. High humidity can lead to condensation within the printer, potentially damaging electronic parts or causing short circuits. On the other hand, low humidity environments can increase the risk of static electricity, which can disrupt the printer’s operation by attracting dust particles to the printhead or causing misfires in the inkjet system.
4. Printhead Performance
The printhead is a critical component of any UV flatbed printer, responsible for depositing ink accurately onto the substrate. Humidity can affect its performance by altering the viscosity of the ink and causing clogs or irregular ink flow. In high humidity, ink can become too thin, leading to poor print definition, while in low humidity, it can thicken, causing the printhead to struggle to maintain consistent ink delivery.
Strategies for Mitigating Humidity Impact
Given the detrimental effects of humidity on UV flatbed printer performance, it is essential to implement strategies to mitigate these impacts. Here are some effective approaches:
1. Environmental Control
Maintaining a controlled environment is crucial. Installing a dehumidifier or humidifier can help regulate humidity levels within the optimal range for printing, typically between 40% and 60% relative humidity. Regularly monitoring and adjusting these levels can significantly reduce the risk of humidity-related issues.
2. Material Preparation
Properly storing and preparing substrates can help mitigate the effects of humidity. Materials should be stored in a controlled environment before printing to ensure they are at a stable moisture content. Additionally, pre-treating substrates with appropriate coatings can enhance ink adhesion and reduce the risk of dimensional changes.
3. Printer Maintenance
Regular maintenance is vital to keep UV flatbed printers operating efficiently. This includes cleaning the printhead regularly to prevent ink buildup and ensuring that all electrical connections are secure and protected from moisture. Using manufacturer-recommended cleaning solutions and following maintenance schedules can help prolong the printer’s lifespan and maintain print quality.
4. Ink Management
Managing ink viscosity is crucial, especially in environments with varying humidity levels. Some printer manufacturers offer inks specifically designed to perform better in humid conditions. Using these inks can help reduce the risk of ink-related issues. Additionally, storing inks in a temperature-controlled environment can help maintain their consistency.
5. Static Control
In low humidity environments, implementing static control measures can be beneficial. This may include using antistatic cleaning wipes on the printer, installing an antistatic ionizer near the printing area, or using static-dissipative materials for substrate handling.
Conclusion
Humidity is a significant environmental factor that can profoundly impact the performance of UV flatbed printers. By understanding the mechanisms through which humidity affects ink curing, material stability, electrical components, and printhead performance, printer operators can take proactive measures to mitigate these effects. Implementing environmental controls, proper material preparation, regular printer maintenance, careful ink management, and static control strategies can help ensure consistent, high-quality prints, regardless of the humidity levels. As technology continues to advance, so too will the ability to manage and adapt to environmental challenges, further enhancing the versatility and reliability of UV flatbed printing technology.