What Is the Impact of Ink Drying Time on Print Quality in UV Flatbed Printers?
What Is the Impact of Ink Drying Time on Print Quality in UV Flatbed Printers?
In the realm of digital printing, UV flatbed printers have gained significant popularity due to their ability to produce high-quality prints on a wide range of materials. These printers utilize ultraviolet (UV) curing technology, which involves the instant drying of inks when exposed to UV light. This process not only accelerates the printing process but also enhances the durability and quality of the prints. However, the ink drying time, a crucial aspect of UV curing, plays a pivotal role in determining the overall print quality. This article delves into the impact of ink drying time on print quality in UV flatbed printers, exploring the underlying mechanisms, factors influencing drying time, and strategies to optimize print quality.
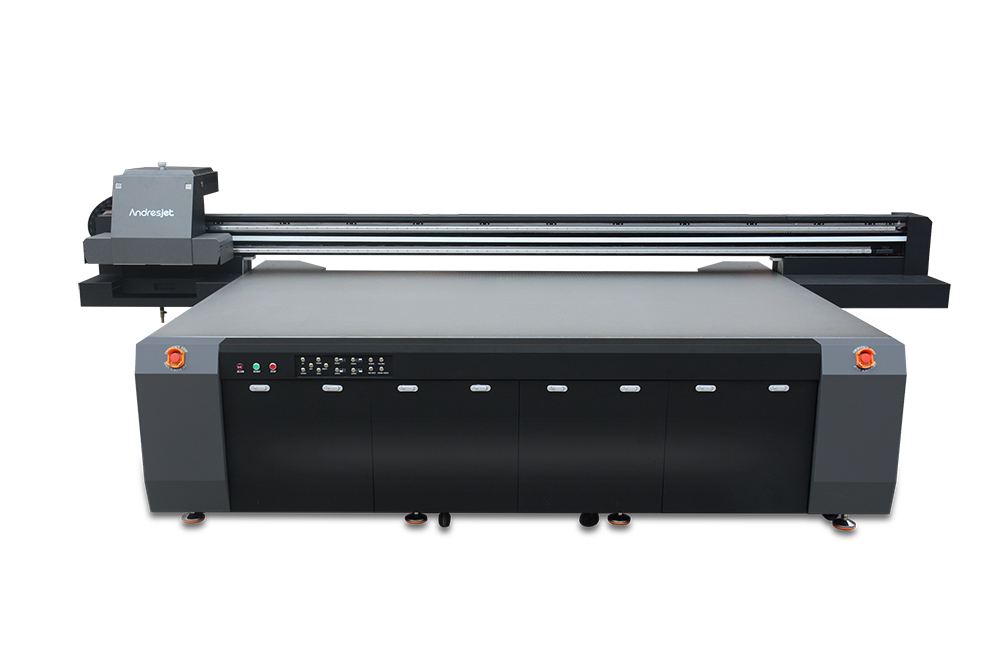
Understanding UV Curing Technology
UV curing is a process where special inks, formulated to be sensitive to UV light, are instantly cured or dried when exposed to high-intensity UV radiation. This technology is particularly advantageous in flatbed printing as it enables the printer to produce vibrant, durable prints on various substrates, including plastics, glass, metal, and even flexible materials. The rapid curing process minimizes the risk of ink smudging, bleeding, or running, ensuring sharp and precise prints.
Ink Drying Time: A Critical Factor
Ink drying time, or the time taken for the ink to fully cure under UV light, is a critical determinant of print quality in UV flatbed printers. Ideally, the ink should cure instantly upon exposure to UV radiation, resulting in a hard, durable surface that resists fading, scratching, and chemical degradation. However, several factors can influence this drying time, ultimately affecting the print’s quality and performance.
Factors Influencing Ink Drying Time
Ink Composition: The chemical composition of the UV ink significantly influences its curing speed. Inks with higher photoinitiator concentrations tend to cure faster as they are more responsive to UV light. Additionally, the viscosity and pigment load of the ink can also impact drying time.
UV Light Intensity: The intensity of the UV light source is directly proportional to the ink’s drying time. Higher intensities lead to faster curing, while lower intensities result in slower drying. The wavelength of the UV light also plays a role, with certain inks curing more efficiently under specific wavelengths.
Substrate Material: The material being printed on can affect ink drying time. Porous materials, such as certain types of paper, may absorb more ink, requiring longer exposure times to fully cure. Non-porous surfaces, like glass or metal, generally allow for faster curing.
Printer Settings: The printer’s settings, including the speed of the print head and the distance between the UV lamps and the substrate, can impact ink drying time. Optimal settings ensure that the ink receives sufficient UV exposure for complete curing.
Ambient Conditions: Environmental factors such as temperature and humidity can influence ink drying time. High temperatures and low humidity generally facilitate faster curing, while cold or humid conditions may slow down the process.
Impact on Print Quality
The ink drying time in UV flatbed printers has a profound impact on the final print quality. Here are some key aspects:
Durability: Properly cured inks exhibit exceptional durability, resisting fading, scratching, and chemical attacks. Insufficient drying time can lead to ink that remains tacky or soft, compromising the print’s longevity.
Color Accuracy and Vibrancy: UV inks are known for their vibrant colors and ability to reproduce a wide color gamut. However, inadequate drying can result in muted colors and poor color accuracy as the ink may not fully solidify, leading to a dull appearance.
Resolution and Detail: Fast and consistent ink drying ensures sharp lines and high-resolution prints. Slow or uneven drying can cause ink to spread, resulting in blurred edges and loss of detail.
Adhesion: Proper curing promotes strong adhesion between the ink and the substrate, preventing cracking or peeling. Insufficient drying can lead to poor adhesion, especially on non-porous surfaces.
Strategies to Optimize Print Quality
To achieve optimal print quality in UV flatbed printers, it is essential to manage ink drying time effectively. Here are some strategies:
Ink Selection: Choose UV inks that are specifically designed for your printer and substrate material. Inks with faster curing properties can significantly reduce drying time while maintaining print quality.
UV Light Optimization: Ensure that your printer’s UV light source is operating at peak efficiency. Regular maintenance and replacement of UV lamps as needed can help maintain consistent and intense UV output.
Printer Calibration: Regularly calibrate your printer to ensure optimal settings for ink deposition and UV exposure. This includes adjusting the print head speed, UV lamp intensity, and the distance between the lamps and the substrate.
Environmental Control: Maintain a stable printing environment by controlling temperature and humidity levels. This can help stabilize ink drying time and overall print quality.
Testing and Experimentation: Conduct tests on different substrates and ink combinations to determine the optimal drying time for each application. This empirical approach can help fine-tune your printing process for consistent, high-quality results.
Conclusion
Ink drying time is a crucial aspect of UV flatbed printing that significantly impacts print quality. By understanding the factors influencing drying time and implementing strategies to optimize this process, printers can achieve vibrant, durable, and high-resolution prints on a wide range of materials. As technology continues to advance, so too will our ability to precisely control and harness the power of UV curing, further pushing the boundaries of print quality in UV flatbed printers.