What Is the Impact of Ink Viscosity on UV Flatbed Printing Quality?
In the realm of digital printing, UV flatbed printing has emerged as a versatile and efficient technology, revolutionizing the way images and designs are transferred onto a myriad of substrates. This innovative process utilizes ultraviolet light to cure inks almost instantaneously, providing a durable and high-quality finish. One critical factor that significantly influences the outcome of UV flatbed printing is ink viscosity. Understanding the intricacies of ink viscosity and its impact on print quality is essential for achieving optimal results in this advanced printing technique.
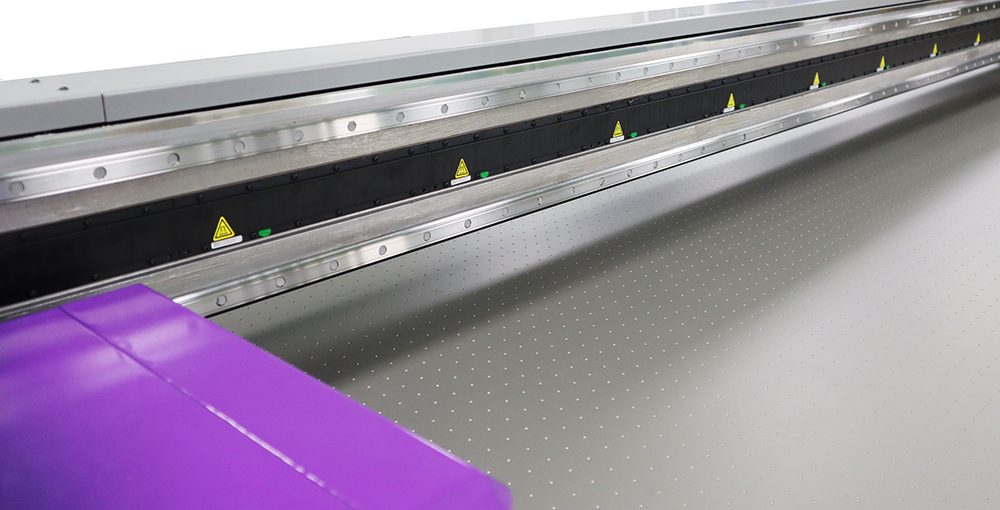
The Fundamentals of Ink Viscosity
Viscosity, in simple terms, refers to a fluid’s resistance to flow. In the context of UV flatbed printing, ink viscosity plays a pivotal role in determining how the ink behaves during the printing process. Inks with low viscosity flow more easily, spreading out smoothly and evenly on the substrate. Conversely, inks with high viscosity are thicker and tend to resist spreading, requiring more force to be dispensed.
The ideal ink viscosity for UV flatbed printing is a delicate balance. It must be fluid enough to flow through the printer’s nozzles without clogging, yet viscous enough to adhere properly to the substrate and maintain the desired print characteristics. Manufacturers carefully formulate their inks to achieve this optimal viscosity, taking into account factors such as the type of printer, the nozzle size, the printing speed, and the nature of the substrate.
The Role of Ink Viscosity in Print Quality
Ink viscosity directly affects several aspects of UV flatbed printing quality, including image resolution, color accuracy, and overall appearance. Let’s delve into these aspects in more detail:
Image Resolution: High-resolution prints require inks that can be precisely controlled and deposited onto the substrate. Inks with the correct viscosity flow smoothly and evenly, allowing for sharp, well-defined edges and intricate details. If the ink is too thin, it may spread uncontrollably, leading to blurred images and loss of detail. On the other hand, if the ink is too thick, it may not flow properly, resulting in uneven coverage and potential nozzle clogging.
Color Accuracy: Achieving accurate color reproduction is crucial in any printing process. Ink viscosity influences how well the ink mixes and adheres to the substrate, affecting the final color output. Inks with optimal viscosity ensure consistent and uniform color distribution, leading to vibrant and true-to-life prints. Deviations in viscosity can cause color shifts, banding, or uneven color saturation, compromising the overall aesthetic appeal of the print.
Overall Appearance: The appearance of a printed piece is a combination of its resolution, color accuracy, and surface finish. Ink viscosity plays a significant role in determining the surface finish of the print. Inks that are too thin may penetrate the substrate too deeply, causing a loss of gloss and potentially showing through on the reverse side. Inks that are too thick may not level properly, resulting in a rough or uneven surface texture. The ideal viscosity ensures that the ink forms a smooth, even layer on the surface, enhancing the visual and tactile quality of the print.
Factors Affecting Ink Viscosity
Ink viscosity is not a fixed property; it can be influenced by various external factors. Understanding these factors and how they interact with ink viscosity is crucial for maintaining consistent print quality. Some of the key factors include:
Temperature: Temperature has a profound effect on ink viscosity. As the temperature increases, ink viscosity decreases, making the ink more fluid. Conversely, lower temperatures cause the ink to thicken. Printers often incorporate temperature control systems to maintain a consistent ink temperature, ensuring optimal viscosity and print quality.
Humidity: Humidity levels in the printing environment can also affect ink viscosity. High humidity can cause the ink to absorb moisture from the air, thinning it out and potentially causing spreading issues. Low humidity, on the other hand, can cause the ink to dry too quickly, leading to clogging and poor adhesion. Maintaining a controlled humidity level is essential for preserving ink viscosity and print quality.
Ink Age: Over time, inks can undergo chemical changes that affect their viscosity. Inks that have been stored for extended periods may thicken or separate, compromising their performance. Regularly checking and replacing aged inks can help maintain consistent viscosity and print quality.
Printer Settings: The printer’s settings, such as the printing speed and the pressure applied to the ink, can also influence ink viscosity. Faster printing speeds may require thinner inks to ensure proper flow, while higher pressures may necessitate thicker inks to prevent dripping or splattering. Adjusting these settings in accordance with the ink’s viscosity can help optimize print quality.
Managing Ink Viscosity for Optimal Print Quality
To achieve the best possible print quality in UV flatbed printing, it is essential to manage ink viscosity effectively. This involves a combination of proper ink selection, environmental control, and printer maintenance.
Ink Selection: Choosing the right ink for the job is crucial. Different inks have varying viscosity characteristics, and selecting an ink that is specifically formulated for the printer and the type of substrate being used can make a significant difference in print quality.
Environmental Control: Maintaining a controlled printing environment, with consistent temperature and humidity levels, can help preserve ink viscosity and ensure consistent print quality. Investing in climate control systems, such as heaters, coolers, and humidifiers, can be beneficial for achieving this.
Printer Maintenance: Regular printer maintenance, including cleaning the nozzles, checking for clogs, and replacing aged inks, can help keep the ink viscosity within the optimal range. Following the manufacturer’s recommended maintenance schedule can prevent potential issues and prolong the life of the printer.
Calibration and Testing: Regularly calibrating the printer and conducting test prints can help identify any viscosity-related issues before they affect the final print quality. Adjusting the printer settings and ink viscosity as needed can ensure that the prints meet the desired standards.
In conclusion, ink viscosity is a critical factor in UV flatbed printing quality. Understanding its importance and how it interacts with other variables can help printers achieve optimal results. By selecting the right ink, maintaining a controlled environment, performing regular maintenance, and conducting thorough calibration and testing, printers can ensure that their UV flatbed prints are of the highest quality, meeting the demands of even the most discerning customers.