What Is the Role of Pretreatment in UV Flatbed Printing
What Is the Role of Pretreatment in UV Flatbed Printing
UV flatbed printing has revolutionized the printing industry, offering unparalleled versatility, precision, and speed. From fashion and beauty products to sports and entertainment memorabilia, tools and home improvement items, raw materials, and maintenance, repair, and operations equipment, UV flatbed printers cater to a diverse range of applications. However, one crucial aspect that significantly impacts the quality and durability of prints is pretreatment. This article delves into the role of pretreatment in UV flatbed printing, exploring its significance, processes, and the technological advancements shaping this critical stage.
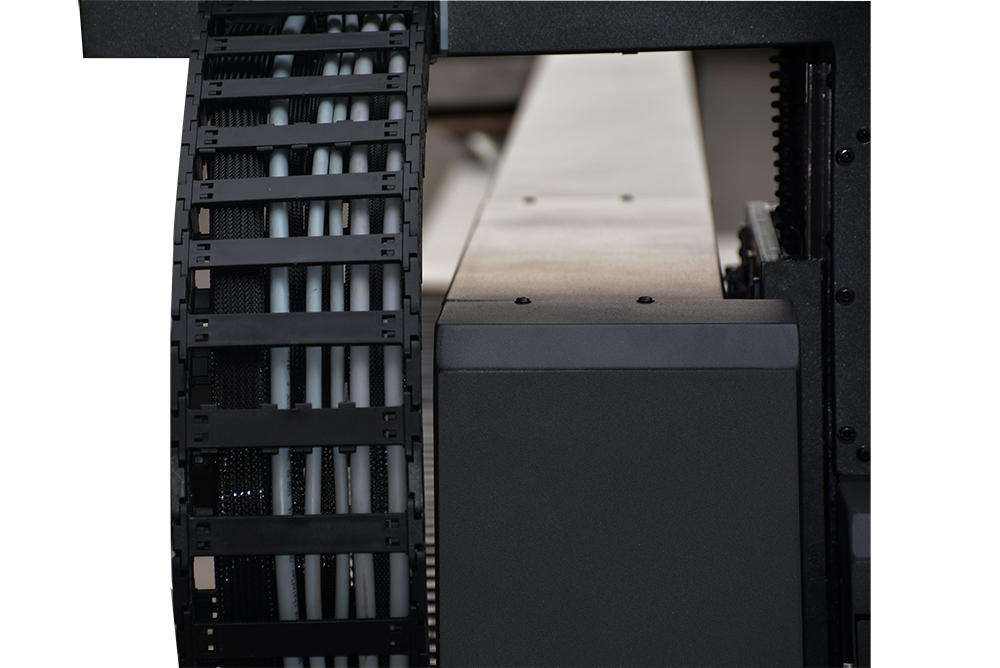
Introduction to UV Flatbed Printing
UV flatbed printing utilizes ultraviolet (UV) light to instantly dry inks onto various substrates. This technology allows for printing on a wide array of materials, including metals, plastics, woods, glass, ceramics, textiles, and more. UV flatbed printers offer high resolution, vibrant colors, and fast turnaround times, making them ideal for short-run and customized printing jobs.
The Importance of Pretreatment
Pretreatment is a vital step in the UV flatbed printing process. It prepares the substrate surface to accept ink evenly and adhere properly, ensuring high-quality prints. Without proper pretreatment, the ink may not bond correctly to the surface, leading to issues such as ink scuffing, cracking, or fading over time.
Surface Preparation
Different substrates have unique surface properties that can affect ink adhesion. For instance, some materials may have a porous surface, while others may be smooth and non-absorbent. Pretreatment modifies the surface to create an optimal environment for ink absorption and bonding.
Cleaning
Removing contaminants such as dust, oils, and grease is crucial. Contaminants can act as barriers, preventing the ink from bonding effectively with the substrate.
Cleaning methods include solvent-based cleaners, aqueous solutions, or mechanical methods like brushing or blasting.
Roughening
Smooth surfaces may require roughening to provide anchor points for the ink. This can be achieved through sanding, plasma treatment, or chemical etching.
Roughening increases the surface area, allowing better ink penetration and mechanical interlocking.
Priming
Priming coats are applied to create a uniform surface that enhances ink adhesion. Primers can be water-based, solvent-based, or UV-curable.
They fill in pores and imperfections, providing a smooth, even surface for the ink to adhere to.
Chemical Pretreatment
Chemical pretreatments involve applying specific chemicals to alter the substrate’s surface chemistry. These treatments can enhance wettability, improve ink adhesion, and provide a durable print.
Surfactants
Surfactants lower the surface tension of the substrate, making it more wettable by the ink. This ensures even ink distribution and minimizes beading.
Adhesion Promoters
Adhesion promoters create chemical bonds between the substrate and the ink. They can be reactive or non-reactive, depending on their mechanism of action.
Reactive adhesion promoters form covalent bonds with the substrate and the ink, providing strong adhesion. Non-reactive promoters, on the other hand, create physical interactions like hydrogen bonding or van der Waals forces.
Crosslinkers
Crosslinkers enhance the durability of prints by forming crosslinks between ink molecules. This creates a more robust ink film that is resistant to scuffing, cracking, and fading.
Pretreatment Techniques for Different Substrates
The pretreatment process varies depending on the substrate being printed. Here’s a closer look at some common substrates and their respective pretreatment techniques.
Textiles
Textiles, especially wool, require meticulous pretreatment to ensure high-quality digital prints. The preparation and pretreatment stages involve several critical steps.
Preparation
Wool fibers are cleaned to remove natural oils, dirt, and impurities.
Chlorination is often used to improve wettability and ink absorption. However, researchers are developing environmentally friendly alternatives to chlorination.
Pretreatment
Textiles are pretreated with a solution containing surfactants, adhesion promoters, and crosslinkers.
The pretreated fabric is then dried and ready for printing.
Plastics
Plastics, such as polyethylene (PE) and polypropylene (PP), are non-polar and have low surface energy, making them challenging to print on. Pretreatment techniques for plastics include:
Flame Treatment
A brief exposure to an open flame oxidizes the surface, increasing its polarity and wettability.
Plasma Treatment
Plasma treatment creates a highly reactive surface by bombarding the substrate with ionized gas. This modifies the surface chemistry, enhancing ink adhesion.
Chemical Etching
Chemical etchants roughen the surface and increase its surface area, providing better ink penetration.
Metals
Metals have a smooth, reflective surface that can repel ink. Pretreatment techniques for metals include:
Anodizing
Anodizing creates a porous oxide layer on the metal surface, which improves wettability and ink adhesion.
Priming
Primers are applied to metals to provide a uniform surface for ink adhesion. These primers can be either water-based or solvent-based.
Silication
Silication treatments create a silicon-based layer on the metal surface, enhancing ink wettability and durability.
Technological Advancements in Pretreatment
The pretreatment process is constantly evolving, driven by technological advancements and the need for more sustainable practices.
Environmentally Friendly Pretreatments
The printing industry is increasingly adopting environmentally friendly pretreatments to reduce its carbon footprint. Researchers are developing aqueous-based pretreatments that are less harmful to the environment and easier to dispose of.
Automated Pretreatment Systems
Automated pretreatment systems are becoming more common, improving efficiency and reducing labor costs. These systems can clean, roughen, and prime substrates in a single, continuous process.
Advanced Chemical Formulations
New chemical formulations are being developed to enhance ink adhesion, durability, and environmental performance. These formulations offer better control over surface chemistry, enabling more predictable and consistent print quality.
Conclusion
Pretreatment plays a pivotal role in UV flatbed printing, ensuring high-quality prints that adhere well to various substrates. By preparing the surface and modifying its chemistry, pretreatment creates an optimal environment for ink absorption and bonding. As technology advances, the pretreatment process is becoming more efficient, sustainable, and adaptable to different materials and applications. By understanding and mastering the pretreatment process, UV flatbed printers can deliver outstanding prints that meet the diverse needs of their clients.