What is the Role of the Media Feeder in a UV Flatbed Printer?
What is the Role of the Media Feeder in a UV Flatbed Printer?
In the world of digital printing, UV flatbed printers have emerged as a versatile and efficient solution for a wide range of applications. These printers are renowned for their ability to print directly onto various materials, including rigid and flexible substrates, with exceptional precision and speed. At the heart of this functionality lies the media feeder, a crucial component that significantly contributes to the printer’s overall performance and versatility. This article delves into the role of the media feeder in a UV flatbed printer, exploring its design, function, and impact on the printing process.
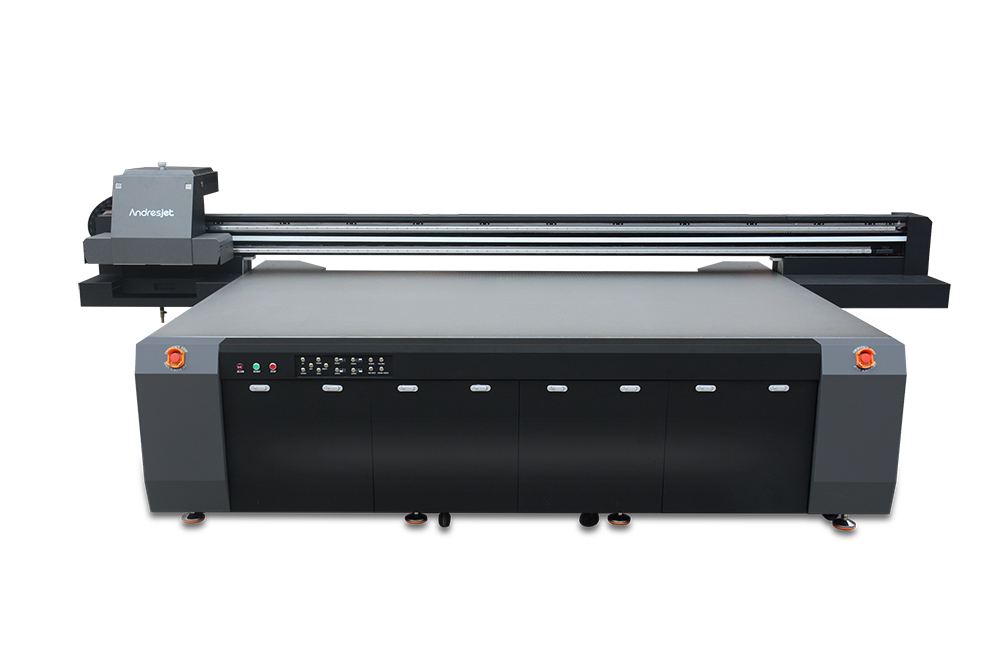
Introduction to UV Flatbed Printers
UV flatbed printers are advanced digital printing machines that utilize ultraviolet (UV) curable inks. These printers are designed to print directly onto flat or slightly curved surfaces, making them ideal for a diverse set of materials such as glass, metals, plastics, woods, and textiles. The UV curing process ensures rapid ink drying, allowing for immediate handling and faster turnaround times.
Key Features of UV Flatbed Printers
Versatility: Capable of printing on various substrates without the need for pre-treatment or specialized coatings.
High Resolution: Offers photo-realistic prints with resolutions up to 1440 dpi or higher.
Rapid Curing: UV inks cure instantly upon exposure to UV light, reducing drying times and improving productivity.
Eco-Friendly: Uses less ink and energy compared to traditional printing methods, making it a more sustainable choice.
Understanding the Media Feeder
The media feeder is a vital component of a UV flatbed printer, responsible for loading and transporting the printing media through the printing path. It ensures smooth and accurate feeding of materials, facilitating precise printing without misalignments or jams.
Design and Construction
The media feeder typically comprises several mechanical and electronic elements, including:
Feed Rollers: These are the primary components that grip and pull the media through the printer. Made of rubber or other high-friction materials, they ensure a firm but gentle grip on the media.
Guide Rails: Guide rails keep the media aligned as it moves through the printer, preventing skewing or off-track movements.
Sensors: Optical or mechanical sensors detect the presence and position of the media, adjusting the feeder’s speed and tension accordingly.
Drive Motors: Powerful motors drive the feed rollers, providing the necessary torque to move the media through the printer, even with heavy or thick substrates.
Functions and Benefits
The media feeder performs several critical functions that contribute to the overall performance of the UV flatbed printer:
Media Loading: The feeder facilitates the easy and secure loading of media onto the printer bed. This ensures that the media is positioned correctly before the printing process begins.
Smooth Transport: By maintaining a consistent speed and tension, the feeder ensures that the media moves smoothly through the printing path. This prevents misalignments, smudges, or other printing defects that can compromise print quality.
Accurate Positioning: The feeder’s precise control over media movement ensures that the print head aligns perfectly with the media, resulting in accurate and consistent printing.
Versatility: The ability to handle various media types and thicknesses is a hallmark of UV flatbed printers. The media feeder plays a crucial role in this versatility, adapting to different materials without compromising print quality.
Productivity: By automating the media loading and transport processes, the feeder significantly enhances the printer’s productivity. This reduces manual intervention, allowing operators to focus on other tasks or prepare for the next print job.
The Impact of the Media Feeder on Printing Quality
The media feeder’s performance directly impacts the quality of prints produced by a UV flatbed printer. Any issues with media handling, such as misalignments, jams, or inconsistencies in speed and tension, can lead to defects in the final product.
Precision and Consistency
The feeder’s precision in positioning and transporting the media is crucial for achieving high-quality prints. Even slight misalignments can result in blurred edges, color shifts, or other visible defects. By maintaining a constant speed and tension, the feeder ensures that the print head moves accurately across the media, resulting in crisp, sharp images.
Media Compatibility
The ability of the media feeder to handle a wide range of materials is essential for UV flatbed printers’ versatility. Different substrates require different handling characteristics, such as varying degrees of grip and tension. The feeder must adapt to these requirements without damaging the media or compromising print quality.
Productivity and Efficiency
Media jams and misfeeds can significantly disrupt the printing process, leading to downtime and increased labor costs. An efficient media feeder minimizes these issues, allowing the printer to operate continuously at peak performance. This not only improves productivity but also enhances the printer’s cost-effectiveness over time.
Challenges and Solutions
Despite its critical role, the media feeder faces several challenges in UV flatbed printers. These challenges, along with their potential solutions, are discussed below.
Challenge: Media Handling Complexity
Handling a wide variety of media types and thicknesses can be challenging for the media feeder. Different materials require different levels of grip and tension to move smoothly through the printer.
Solution: Manufacturers design feeders with adjustable settings and advanced sensors that can detect and adapt to different media types. This ensures that the feeder can handle a wide range of materials without compromising print quality or causing jams.
Challenge: Accurate Positioning
Maintaining precise positioning of the media throughout the printing process is crucial for achieving high-quality prints. Even slight misalignments can result in visible defects.
Solution: High-resolution encoders and linear guides are integrated into the feeder’s design to ensure accurate positioning. These components work in conjunction with the printer’s control system to monitor and adjust the media’s position in real-time.
Challenge: Jam Prevention
Media jams can significantly disrupt the printing process, leading to downtime and increased costs. Identifying and preventing jams before they occur is crucial for maintaining productivity.
Solution: Advanced sensors and algorithms are used to detect potential jams early on. The feeder’s control system can then adjust its speed and tension settings to prevent jams from occurring. Additionally, easy-access panels and intuitive maintenance procedures make clearing jams quick and efficient when they do occur.
Conclusion
The media feeder plays a pivotal role in the performance and versatility of UV flatbed printers. By facilitating the smooth and accurate loading, transport, and positioning of printing media, the feeder ensures that the printer can produce high-quality prints on a wide range of substrates. Its design, construction, and functionality are critical to achieving precision, consistency, and productivity in the digital printing process.
As UV flatbed printers continue to evolve and expand their applications, the media feeder will remain a vital component, driving innovation and enhancing the overall printing experience. Manufacturers will continue to refine and improve the feeder’s design, incorporating advanced technologies and materials to meet the evolving needs of the digital printing industry.
In conclusion, the media feeder is more than just a mechanical component; it is a key enabler of the UV flatbed printer’s exceptional capabilities and the driving force behind its success in the digital printing market.