What Is UV Curable Ink and How Does It Work in a UV Flatbed Printer
In the vast landscape of printing technologies, UV curable ink stands as a beacon of innovation and efficiency. This advanced ink formulation, combined with UV flatbed printers, has revolutionized the printing industry, offering unparalleled precision, durability, and environmental friendliness. This article delves into the intricacies of UV curable ink and its workings within a UV flatbed printer.
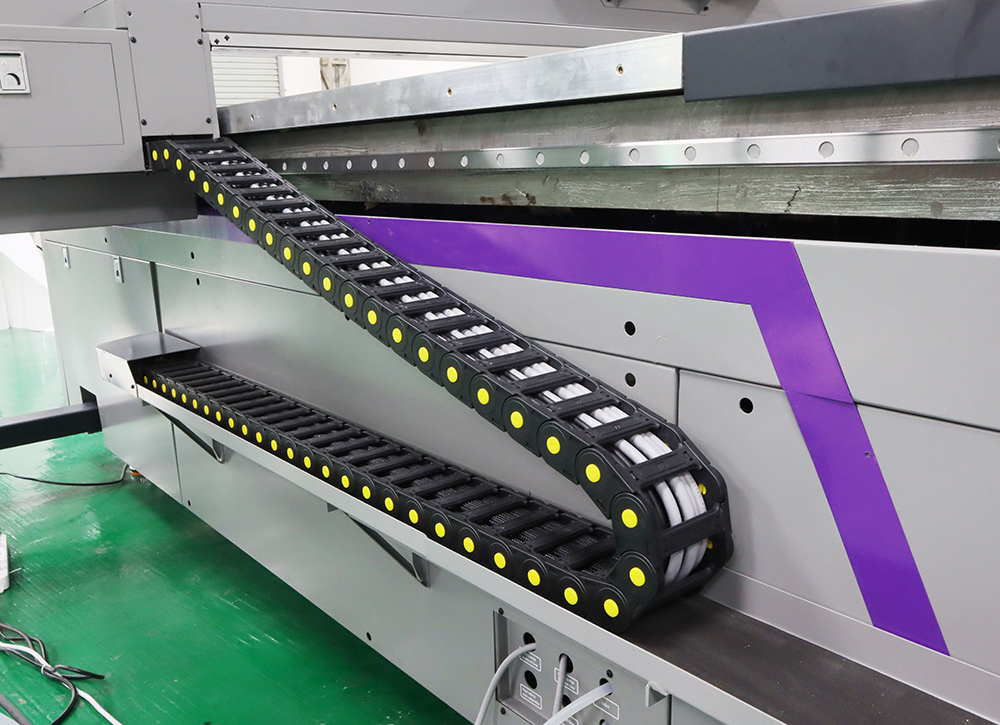
Understanding UV Curable Ink
UV curable ink, also known as ultraviolet-curable ink or UV ink, is a type of ink that undergoes a chemical reaction when exposed to ultraviolet (UV) light. This reaction causes the ink to solidify almost instantly, creating a durable and high-quality print. Unlike traditional inks that rely on evaporation or heat to dry, UV curable ink leverages the power of UV light to cure, making the process faster and more efficient.
The composition of UV curable ink is meticulously designed to facilitate this rapid curing process. It typically consists of several key components:
Pigments or Dyes: These provide the color to the ink. In UV curable inks, pigments are often preferred over dyes due to their superior lightfastness and durability.
Prepolymers or Oligomers: These are low-molecular-weight polymers that act as the backbone of the ink. When exposed to UV light, they undergo polymerization, forming a high-molecular-weight polymer network.
Monomers: These are small molecules that fill the gaps between the prepolymers, enhancing the physical properties of the cured ink film.
Photoinitiators: These compounds absorb UV light and generate reactive species that initiate the polymerization reaction.
Additives: These include stabilizers, flow agents, and other compounds that improve the ink’s performance and processing characteristics.
One of the most significant advantages of UV curable ink is its low volatile organic compound (VOC) emissions. VOCs are harmful pollutants that can contribute to air quality issues. UV curable inks, however, cure almost entirely through a chemical reaction, releasing minimal VOCs into the atmosphere. This makes them an excellent choice for environmentally conscious printers and end-users alike.
The Working Principle of UV Flatbed Printers
UV flatbed printers are specialized devices that utilize UV curable ink to produce high-quality prints on a wide range of materials. These printers are designed to handle flat substrates, such as wood, metal, glass, plastics, and even some flexible materials like textiles and leather.
The core of a UV flatbed printer lies in its printing head and UV curing system. Here’s a detailed look at how these components work together to produce stunning prints:
Printing Head
The printing head of a UV flatbed printer is equipped with a series of nozzles that dispense the UV curable ink onto the substrate. These nozzles are controlled by a sophisticated inkjet system that ensures precise deposition of the ink droplets.
The inkjet system works by rapidly ejecting ink droplets from the nozzles, guided by digital signals that correspond to the image being printed. This digital control allows for extreme precision, enabling the printer to produce intricate designs and fine details.
UV Curing System
Immediately after the ink is deposited onto the substrate, it passes under the UV curing system. This system consists of one or more UV lamps that emit high-intensity UV light.
When the UV light strikes the ink, it activates the photoinitiators within the ink formulation. These photoinitiators then generate reactive species that initiate the polymerization reaction between the prepolymers, monomers, and other components of the ink.
The polymerization reaction proceeds rapidly, forming a high-molecular-weight polymer network that solidifies the ink almost instantly. This curing process not only fixes the ink to the substrate but also enhances its durability and resistance to scratching, fading, and other forms of wear and tear.
The Advantages of UV Curable Ink in UV Flatbed Printers
The combination of UV curable ink and UV flatbed printers offers a multitude of advantages over traditional printing methods:
High Production Speed
The rapid curing process of UV curable ink significantly reduces the production time required for each print. Unlike traditional inks that can take hours to dry, UV curable ink cures almost instantly upon exposure to UV light. This allows UV flatbed printers to achieve high production speeds, making them ideal for high-volume printing applications.
Enhanced Durability
The cured film of UV curable ink is highly durable and resistant to scratching, fading, and other forms of wear and tear. This makes UV prints particularly suitable for applications that require long-lasting and high-quality prints, such as signage, packaging, and promotional materials.
Environmental Friendliness
As mentioned earlier, UV curable inks have low VOC emissions, making them an environmentally friendly choice. This is particularly important in today’s increasingly eco-conscious world, where reducing pollution and conserving resources are top priorities.
Versatility
UV flatbed printers can handle a wide range of materials, from rigid substrates like wood and metal to flexible materials like textiles and leather. This versatility makes them an excellent choice for printers who need to produce prints on a variety of materials.
Precision and Detail
The digital control of the inkjet system in UV flatbed printers enables extreme precision in the deposition of ink droplets. This allows for the production of intricate designs and fine details that would be difficult or impossible to achieve with traditional printing methods.
Challenges and Considerations
While UV curable ink and UV flatbed printers offer numerous advantages, they also come with their own set of challenges and considerations:
Initial Investment
UV flatbed printers and UV curable inks can be more expensive than traditional printing equipment and inks. This can make the initial investment in UV technology a significant hurdle for some printers.
Maintenance and Operation
UV flatbed printers require regular maintenance and calibration to ensure optimal performance. Additionally, operators need to be trained in the proper handling and use of UV curable inks to avoid potential issues such as clogging or improper curing.
Material Compatibility
While UV flatbed printers can handle a wide range of materials, not all materials are compatible with UV curable inks. Printers need to carefully select the right ink and substrate combination to ensure the best possible print quality and durability.
Health and Safety
While UV curable inks have low VOC emissions, they can still pose health and safety risks if not handled properly. Operators need to wear appropriate personal protective equipment (PPE) and follow proper safety protocols to minimize exposure to UV light and ink components.
Conclusion
UV curable ink and UV flatbed printers represent a significant advancement in the printing industry. Their combination of high production speed, enhanced durability, environmental friendliness, and versatility makes them an excellent choice for printers who need to produce high-quality prints on a variety of materials.
While UV technology comes with its own set of challenges and considerations, the benefits it offers far outweigh the drawbacks. As the printing industry continues to evolve, UV curable ink and UV flatbed printers are poised to play an increasingly important role in meeting the demands of modern printing applications.
In summary, UV curable ink is a remarkable innovation that leverages the power of UV light to cure ink almost instantly. When combined with UV flatbed printers, this technology enables the production of high-quality prints on a wide range of materials at unprecedented speeds. As the printing industry moves towards more sustainable and efficient practices, UV curable ink and UV flatbed printers are set to become even more integral to the industry’s future.